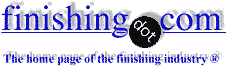
-----
Hard Chrome Plating: Hardness vs. Thickness
Q. I would like to know if there is a way to determine what thickness of hard chrome plating will yield a hardness of 69-71 Rockwell C on a substrate of 32-36 Rockwell C.
I am attempting to achieve this surface hardness with a thickness of 1.5 mils. Is this possible.
Also, in general, where could I find data on the correlation between coating thickness and surface hardness for various coatings and substrates.
Barry M. Burnett- Pacolet, South Carolina
2000
A. Hi Barry. All chrome plating is hard. Nor does it, to my knowledge, get harder as the thickness increases. Rather, the indentor simply encounters more difficulty in cracking through the "egg shell".
So your question may really be: "How thick does chromium have to be before my thickness tester will correctly measure what it's supposed to?" :-)
I can't answer that specific question, but maybe a reader who is more skilled in the met lab than I am will help you.
Regarding your more general question, most platings are at their hardest right at the interface with the substrate because the atoms of one metal (the plating) are trying to match the crystal spacing of a different metal (the substrate), but they can't. The result is a multitude of small discontinuous crystals which don't flex like larger crystals. As the plating gets thicker, all other things being equal, the grain gets larger and softer as it increasingly is able to adopt its own natural structure without interference from another metal.
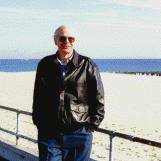
Ted Mooney, P.E.
Striving to live Aloha
finishing.com - Pine Beach, New Jersey
2000
A. Ted's comments above are excellent and valuable for those who always wonder why hardness varies with thickness or why some measurements are lower than expected.
I would like add that the minimum coating thickness at which you could measure the hardness with above 90% accuracy depends on the substrate hardness, surface smoothness, as well as the type of instruments used to measure hardness. Our observations on near-mirror finished smooth surfaces using microhardness tester indicated that, for a relatively soft substrate with about 20 to 25 HRc, you need at least 1 mil coating thickness. I suggest using a polishing method and microhardness tester to get accurate data. You will probably need to develop your own data for various coatings and substrates.
Mandar Sunthankar- Fort Collins, Colorado
2000
A. To expand on the comments above:
The accuracy of an indentation hardness test, such as Rockwell or microhardness methods, is a function of the depth of the indentation and the thickness of the material to be tested. The test will be affected by material within a depth of about 10 times the depth of the indenter penetration.
For Knoop microhardness, the load can be varied to test very thin coatings. At typical test loads, Mandar's recommendation of a 0.001 in. minimum thickness is about right. Specialized testers with capability for very low loads can test coatings with much lower thickness, i.e. down to a few microinches. These tests, however, cannot be readily converted to Rockwell hardness values.
ASTM gives minimum thickness requirements for each of the test scales based on the material hardness. The thinnest material or coating that can be tested by the Rockwell method is 0.006 in. for a material that is at least 60 HRC. This test could be done using the Rockwell 15N superficial hardness scale. Direct Rockwell C testing will test to a depth of 0.022 in. at a hardness of 69 HRC. Any thinner than this, and you will have substrate effects.
Hope this helps.
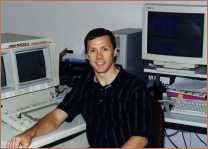
Larry Hanke
Minneapolis, Minnesota
2000
A. We have this problem to measure the chrome hardness. We are package producers, so we engrave our rotogravure cylinders. After engraving, we chrome plate the cylinder with a 6 micron layer; this is the recommended thickness for chrome because a wide chrome layer affects the engraved cell size. Measuring the Micro cracks per linear inch is an indirect method to measure the chrome hardness.
Enrique Nunez- Mexico, Ocoyoacac
October 27, 2010
Ed. note: to make the site's information most easily accessible, finishing.com merged together four formerly separate threads about hard chrome plating. Please forgive any repetitiveness that has resulted. The commenters below did not have the comments above to refer to :-)
Q. Hi,
I heard that in hard chrome plating for steel, the hardness increases as thickness increases. But wouldn't it be brittle when the coating reaches certain thickness? If this is so, then there must be specific thickness that gives best hardness, really hard and not brittle. I'm really puzzled. If thickness increased, would that mean the wear resistance increase too? I'd like to know the best coating thickness and hardness that give best wear resistance for steel.
Thank you very much, really hoping for your reply.
Tan Haning- Southbank, Vic, Australia
2001
A. No, the hardness is the same all of the way thru.
But, on a thin coat, a heavy pointed pressure over soft steel will allow the steel to give and the chrome will crack badly, probably peeling.
Typical thickness in the aerospace industry is 0.003 to 0.005 inches, i.e., 3-5 mils. Chrome has a terrible compressive internal stress, so that when you get up to 0.010" , it tends to get a few massive cracks all by it self after a while. So, the 3-5 mils is fairly close to an optimum.
Thicker does not have more wear resistance, but it has more thickness to wear, so it can wear longer.
James Watts- Navarre, Florida
2001
A. Chrome does not really get harder with increasing thickness. But one issue that may be confusing you is that chrome plating is like an eggshell on an egg: if it's too thin on a soft substrate, it cannot really offer hardness because it will simply crush. So a key issue in determining the required thickness is the hardness of the underlying steel.
A hard component where the loading and wear is spread over a large area, like the piston on a strut or shock absorber, may only require a few ten-thousandths of an inch of chrome; a heavily loaded component may require 3-5 mils as James explains; a soft component like plain steel or copper may require about two thousandths of an inch before the chrome plating becomes useful.
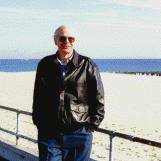
Ted Mooney, P.E.
Striving to live Aloha
finishing.com - Pine Beach, New Jersey
A. Hi Tan,
It always depends what's causing the wear, hence where the chrome plated part is going to be used and with what it is in contact to cause wear. Micro-cracks in the chrome layer actually have a positive effect on wear (always depends the type of wear).
As previous postings have mentioned, if the deposit is too thin and you perform a hardness measurement with incorrect load weight you will measure the softer substrate. To get reliable hardness measurements you either plate thick hard chrome and after "settling" time you measure the hardness, or you keep the thickness where it is and perform cross sectional analysis in order to perform a micro-hardness measurement within the structure to get reliable data.
Cheers
- Melbourne, VIC, Australia
July 4, 2012
Q. Is it possible to have an extremely abrasion resistant and durable hard chrome coating of thickness 0.3-0.5 mil . If so what should be the minimum substrate hardness for the same with the required surface hardness of 68 Rc.
Gaurav Garg- New Delhi, India
2001
A. Hello, Gaurav. Although I cannot answer your question exactly, I can rephrase it a little and say that I believe that hard chrome plating thicknesses of 0.3 to 0.5 mils are widely used on hard substrates if the point loading is not too high. I think if you look into the ubiquitous "air springs" that are used to support automobile lift gates and hoods that you will find chrome thicknesses in this range and lower.
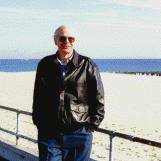
Ted Mooney, P.E.
Striving to live Aloha
finishing.com - Pine Beach, New Jersey
2007
Q. There had been many inquiries like this. Now this is quite clear like an eggshell, we need to have a strong substrate to have a wear resistance and hardness advantage of "hard chrome".
Is there any empirical formulae or relation between substrate hardness vs. contact stresses vs. coating thickness for durable wear resistant coating.
I have been trying with 50-55 RC substrate hardness , 4 mil coating thickness (because of geometrical limitation to 5 mil max.) and around 4 kgf pressure in my roller dies with limited success.
Please comment if I need to improve my process or change my parameters.
Gaurav Garg- India, New Delhi
2001
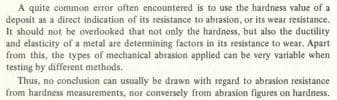
9th Edition, Vol. 5
"Surface Cleaning, Finishing & Coating"
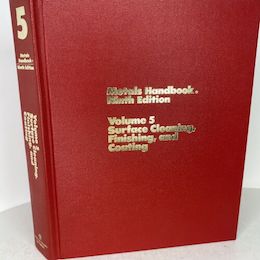
on eBay or Amazon
or AbeBooks
(affil link)
A. Hi Gaurav. Although I was never a hard chrome plater, and can't answer your question, it sounds like your operating parameters may not be right, so your wear resistance is not what it should be. Weiner and Walmsley claim that hardness cannot be converted to wear resistance or vice versa.
Weiner and Walmsley also do not recommend hard chrome plating of steels over 57 to 62 RC, which offers a hint that you can't go too much higher with your substrate hardness. Good luck.
The suppliers of proprietary hard chrome catalysts and processes often claim that the hardness of their processes is greater than the conventional Sergeant bath, and this is supported in the literature, with ASM Metals Handbook Vol. 5 asserting Vickers diamond pyramid hardness of 900 to 1000 for the conventional Sergeant bath, and 1000 to 1100 or higher from mixed catalyst baths.
Readers may be interested in thread 35184, "Hard chrome plating catalysts -- sulfuric acid vs. fluorides (SRHS) vs. MSA (HEEF-25)".
Regards,
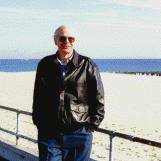
Ted Mooney, P.E.
Striving to live Aloha
finishing.com - Pine Beach, New Jersey

Q. We are experiencing short life of hard chrome. The chrome is coming off in less than 50%(usage) of what it did in the past.
We have three suppliers for our chrome plating and we are experience the same problem with each of them.
Chrome is applied to A2 steel molds for rubber molding. The molds are heat treated, then we send them out for chrome plating. Our suppliers glass bead the molds before they are plated.
We use ultra sonic and alkaline to clean the molds.
Any suggestions?
Thanks,
Darrell Elkins- Elgin, Illinois, USA
A. Hi Darrell, I think you already realize that the odds of three different plating shops losing control of their process is remote. You are probably just looking for confirmation that there hasn't been a sea change in the chrome plating process that would account for this drop in performance. There hasn't been.
It certainly sounds like you must have changed the substrate metal in some way that rendered it less hard: maybe it's not really A2 or it used to be something else. Maybe a heat treatment has been altered. Maybe you used to shotpeen or polish and you no longer do. If I were you, I'd probably concentrate on reviewing internal records and interviewing long term employees rather than wasting time at the plating shops because all three almost surelydidn't change. Good luck.
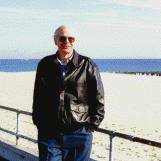
Ted Mooney, P.E.
Striving to live Aloha
finishing.com - Pine Beach, New Jersey
Q. I would like to know if anyone has knowledge on how to get a denser hard chrome coating or how to make the coating achieve a higher hardness rating.
Mark OBrienplating shop employee - Ontario, California, USA
December 2, 2008
December 2, 2008
A. Hi, Mark. Harder than what you are presently achieving? I have heard Atotech claim that HEEF-25 is harder than conventional chrome; you could inquire of them. I have also heard people claim that their "thin dense chrome" is harder than the usual, so you could ask them for hardness ratings. Good luck.
Regards,
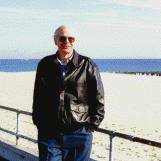
Ted Mooney, P.E.
Striving to live Aloha
finishing.com - Pine Beach, New Jersey
Q. Our chrome plating shop is taking on a new product line and customer that has certain hardness requirements. The customer is convinced that the hardness he requires offers much greater wear resistance than the hardness we routinely produce. Is there any quantitative information correlating chrome hardness vs. wear resistance?
George Tuttle- Owensboro, Kentucky, USA
June 1, 2012
by William Safranek
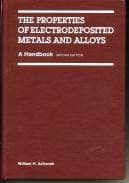
on eBay or Amazon
or AbeBooks
(affil link)
A. Try to get a copy of the excellent book "Properties of electroplated metals and alloys" by William Safranek.
You will find many references and valuable data in it including some about your query.
Monterrey, NL, Mexico
June 6, 2012
Q. Hi, I'm grinding pump shafts for civil aircraft. Basically it's a system that trims up the fuel in the wings of the A380 and the Dreamliner, keeping an even distribution of fuel in the tanks as the engines use it.
Thing is the hard chrome thickness is around 0.255 mm. Normally I'm used to achieving about 0.150 mm on landing gear pins and housings. Just wondering why these pumpshafts need so much on? Any ideas?
- Dorset, UK
September 28, 2013
A. Because someone thought that it was needed.
Possible reasons might be they have a hard time repeatedly centering the shaft, so they make it a bit smaller to insure a desired minimum of chrome on all sides. the shaft might be a bit soft, so they are using more chrome to get it to wear better. IE: not deform under load. It could even be that the original design was mis stated and they used more chrome rather than admit the problem.
My guess is that the engineer thought that if a little chrome was good, more was better.
- Navarre, Florida
October 1, 2013
Q. That sounds like it could be a reason for the amount of chrome on these shafts. I am constantly straightening them to achieve concentricity of less than 0.01 mm in order to keep the job in limit they are quite flexible with two long thin diameters either end. The base material is some kind of magnetic stainless not sure of the exact spec.
With the large chrome thickness I'm getting faces/shoulder with over 1.5 mm of chrome on that is a real bitch to grind off plus a lot of them don't clean up in the corners which means they have to be stripped and re-chromed. I sort of assumed that with the large chrome thickness dimension this massive build up on the faces is the norm? Or can the platers do better?
- Bournemouth, Dorset, England
October 4, 2013
A. For tough chrome plating, you cannot beat using conforming anodes. They have the ability (with tweaking) of putting the chrome where you want it.
Making the racks and anodes takes a bit of time, but the shorter plating time will more than make up for it in the long run. Couple that with less rejects and it becomes a great deal.
A lot of old time chrome shops are hung up on using tank anodes and they have the exact problems that you talk about.
It honestly takes someone to show them how.
- Navarre, Florida
October 7, 2013
A. Hello,
I've read what you are typing about, how to measure a thin hard chrome deposit. Hard chrome has the same hardness with same time you start the rectifier. To measure a thin thickness, you go beside and measure the hardness.
And listen to what Mr. James and Ted say because I'm in agreement with them about what they have told you.
Regards,
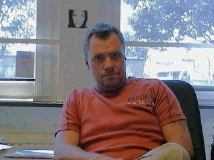
Anders Sundman
4th Generation Surface Engineering
Consultant - Arvika,
Sweden
October 8, 2013
Chrome hardness varies across the part
Q. Hi all.
I got lack of uniformity regarding to hardness, during hard chrome plating.
I got more hardness at the areas that are close to the rod than the parts are hanging on, and less hardness at rest of areas.
What can be the reasons for that?
- Tel Aviv, Israel
July 25, 2018
Q, A, or Comment on THIS thread -or- Start a NEW Thread