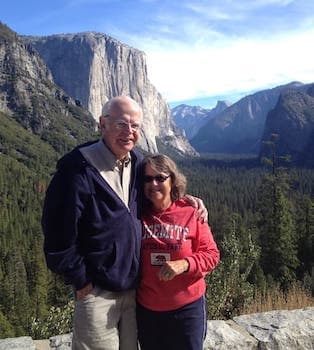
Curated with aloha by
Ted Mooney, P.E. RET
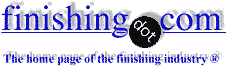
The authoritative public forum
for Metal Finishing 1989-2025
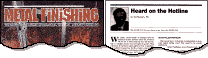
-----
Chrome Failure, Microgalvanic Cell
My name is Evan. I am currently working on a project to establish the root cause and solution of a corrosion problem. I work in the timber industry in regard to medium density fibre board products. We basically mould a mixture of wood fibre and resin in a high temperature press to obtain a hard textured product. The moulds are basically mild steel with a hard chrome coating. The purpose of the chrome is to give good wear an release characteristics.
The problem: It is corrosion pitting of the chrome surface. It is contained to only some areas of our dies where the most amount of pressure is applied. In time this pitting then produces a product defect. We believe that the root cause is the formation of a microgalvanic cell between the chrome and the base metal. This occurs because our fibre/resin is very moist and some of the liquid is forced through the micro cracking of the chrome. This liquid acts as a electrolyte between the chrome and nickel to cause a corrosive reaction.
The obvious answer is to apply a nickel underlay under the chrome, but in our circumstance this is not practical. Basically we need to make do with what we have got in regard to moulds. We have also determined that a sacrificial anode will also not be practical.
All of the components in our mixture, that are pressed, have been analysed to determine if we have any corrosive components. So far we have found absolutely nothing.
Are there any simple methods of stopping the activation of this cell. Should we de-ionise our water? Are there any ways of disrupting the corrosive current?
Evan Goodman- NSW, Australia
2000
I do not have the solution to your problem, but I can tell you right now that the solution is NOT deionizing the water. Deionized water is more aggressive and will corrode your dies quicker.
You can disrupt the corrosive current by using a barrier coating like chrome plating. Your problem is that you are damaging the chrome or the chrome is too porous.
It would be helpful to know why a nickel strike and why external anodes will not work.

Tim Neveau
Rochester Hills, Michigan
2000
I would certainly agree with Tim that DI water is more corrosive.
I don't think I share your galvanic theory, though. Chrome oxidises so quickly and so well that I don't think there is any history showing that chromium plating accelerates corrosion of steel. Rather, I think the steel is simply chemically corroding, as steel does, under the cracked areas and porosity areas.
More chrome plating might help. Higher quality microcracked or microporous chrome plating will disperse the corrosion, resulting in less pitting. But in the end, as Tim implies, chrome alone cannot usually adequately protect steel in corrosive environments. A nickel undercoat, or possibly some kind of teflon impregnation of the plating, or stainless steel molds with a chromium plating seems to be the answer.
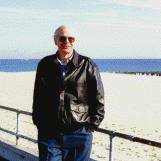
Ted Mooney, P.E.
Striving to live Aloha
finishing.com - Pine Beach, New Jersey
2000
2000
I agree that a sacrificial anode will probably not work in this instance because you will probably will not be able to get the anode placed close enough to the potential corrosion areas. There is certainly potential for corrosion under the chromium plating, especially if it is thin. There is probably enough ionic content in your water to create an electrolyte that will corrode steel, even if you don't find anything terrible in the water.
It is interesting to me that the damage is occurring to only some dies in the areas of greatest pressure. Are you sure that the failure mode is not some type of mechanical failure of the plating?
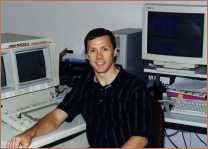
Larry Hanke
Minneapolis, Minnesota
Q, A, or Comment on THIS thread -or- Start a NEW Thread