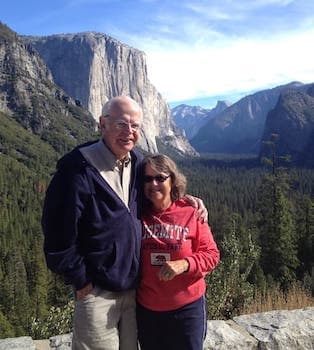
Curated with aloha by
Ted Mooney, P.E. RET
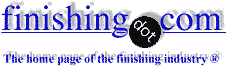
The authoritative public forum
for Metal Finishing 1989-2025
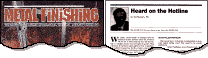
-----
Heat-treatment of ENP Coating reduces corr.resistance
Q. My company makes Ball valves, and ball and seats are Electroless Nickel coated (with 11% Phosphorous solution) as a standard. Since the treatment is same for both Ball and Seat, the resulting hardness is same. One of the customer has asked that Ball must be harder than the seats (Since Seats are cheaper to replace). The suggestion from my colleagues is that we do it by carrying out heat-treatment on the ball (750 °F baking for about an hour). My feeling is that, since this baking crystallizes the coating and there by reduces the corrosion resistance of the coating, we should be going for a EN Coating with less % of Phosphorous, which inherently gives a harder surface. Can somebody guide me whether this reduction in corrosion resistance is significant? or negligible. Any suggestion is highly appreciated. Please give some reference wherever possible, since I need them when I discuss it with others. Thanks
Mahesha- Houston, Texas, USA
2000
A. Heat treatment of high phosphorous EN will reduce the corrosion resistance a lot. On the other hand, using a low phosphor EN will not solve your problem. The low P En is harder but has a low corrosion resistance anyway.
Take a close look at the data sheets of high P and low P EN, they include all the relevant data regarding hardness with and without heating and corrosion resistance.


Sara Michaeli
Tel-Aviv-Yafo, Israel
2000
A. I would suggest a thin layer of hard chrome on the nickel coating.
Mandar Sunthankar- Fort Collins, Colorado
2000
A. Hi Mr. Mahesha,
The corrosion resistance of EN coating is dependent on the environment that they are exposed to. Generally, EN has excellent corrosion resistance and is not susceptible to SCC. High phosphor content coating exhibits superior performance in an acidic medium while low phosphor content coating fails miserably. On the other hand, low phosphor content coating outperforms high content coating in an alkaline environment. First and foremost, it is well documented that EN coatings are not suitable for applications where two EN-coated parts would be in sliding contact with each other(particularly of the same hardness). This is because frictional heating then arises, and the hot-hardness of EN is low. This eventually leads to galling and fretting wear which ultimately accelerates the corrosion process. The 'as-deposited' hardness of low phosphor EN is higher('700 HK) than high phosphor EN coating('450 HK). A one-hour heat treatment at 400 deg C will increase both hardness to '850-900 HK.
In your application, you may only heat treat the ball to a higher hardness and use the seat in the 'as-deposited' condition. Maybe this will help to alleviate the corrosion problem. The effect of heat treatment on the corrosion resistance of EN coating is not significant.High (>10%) phosphor content EN coating has less porosity and its amorphous nature(i.e. without grain boundaries) is advantageous in corrosive environments.Besides, the surface finishing of the substrate can have a significant effect on the formation of porosity in EN coating. For relatively smooth substrates, a thickness of 25 micron will suffice. For rough or sandblasted substrates, a thickness of 50-70 micron is recommended. I hope my reply is of help to you.
Best regards,
Wong Soon Hing- Singapore
2001
Q. Is ENP coating superior to FCC coating over zinc/nickel electro plating.. This is for studbolts for Valves.
George Sebastian- Dubai, UAE
April 24, 2013
A. Hi George. Please spend a couple of paragraphs describing your situation. I don't know what you mean by FCC (face centered cubic? FCC what?). You want a comparison of Electroless Nickel Phosphorous coating to Zinc-nickel electroplating followed by FCC (whatever that is)? Thanks.
Regards,
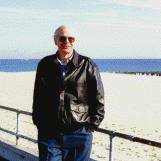
Ted Mooney, P.E.
Striving to live Aloha
finishing.com - Pine Beach, New Jersey
April 25, 2013
Q, A, or Comment on THIS thread -or- Start a NEW Thread