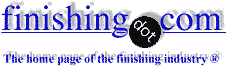
-----
Rust on 304 SST
Completely by accident, I discovered topic 34 on your website.
What Mr. Albom describes is very similar to a condition that we've discovered with some 304 flexible conduit that we purchase. Incidentally, an independent lab verified the material. The outside color turned dull gray and rainbow-ish in places. The inside was full of loose rust particles. We were completely baffled, as was the company that made the product, why it was rusty when it was SST. As I said, the lab verified that it was 304, but they also stated that the rust was oxidation of base material. After, reading your response to Mr. Albom's letter I now know that a high pH can dissolve the chromium. Without the chromium, and in the presence of oxygen, could that cause the conduit to rust? Also, what other affects will this have on the material. Will it weaken it or make it brittle?
David Posner- San Diego, California
2000
David:
I am with Ted Mooney on this one. 304SS is used all over the world for high pH use and I have never heard of this before. There is something else going on here.
I would be happy to discuss this with you.
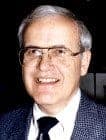

Lee Kremer
Stellar Solutions, Inc.

McHenry, Illinois
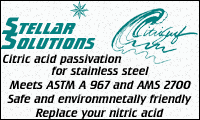
2000
Stainless is a misnomer. All steel will rust and does under conditions that encourage it. You can use the annealed condition (304L) for maximum corrosion resistance in that material; you could have the stainless passivated or you could plate the surface with something.
For food and phammaceutical instruments 304 would never be used because of its corrosion susceptibility. They are more likely to use 316 or 17-4ph.
In your instance I suspect the conditions were ripe for corrosion, or maybe there was some material contamination at the foundry.
engineering - Vista, California, USA
2005
Q, A, or Comment on THIS thread -or- Start a NEW Thread