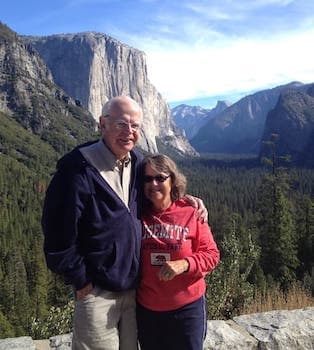
Curated with aloha by
Ted Mooney, P.E. RET
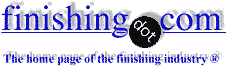
The authoritative public forum
for Metal Finishing 1989-2025
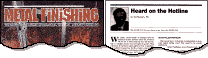
-----
Burned-out and Bluish/Cloudy Chrome plating
2000
We are having a problem with our chrome plating process (after bright nickel plating). If we turned on the rectifier (and set it to 7 Volts DC) before putting the rack on the cathode, we have a burned-out at high-current area of the plated part.
However, if we turn on the rectifier after we put the rack on the cathode, we have a bluish/cloudy plating on the part.
Should we use a special kind of rectifier ?
We appreciate it if you could share your experience with us.
Thanks,
Irwan.
Irwan Nusantara- Jakarta, Indonesia
Dear Irwan,
I think there is nothing wrong with your rectifier.If you are plating decorative nickel chrome, consider the following which might be relevant to your present problem:
1)sulfuric acid content might be too high which causes burnt at high current density area.Add Barium Carbonate to reduce H2So4(To lower 0.05g/l H2SO4 add 0.01g/l Baco3)
2)Your temperature is too high.I have operated between 40-50 degrees C..but you have to vary your current.Current density is between 10-20A/dm2. Normally, when temp.is high, current should be increased and when temp. is low, current should be decreased.From experience and the parts you plate, you should be able to determine the required current corresponding to your bath temperature.
3)When your racks enter your bath it should be "hot-entry".This means the current is on when your rack enters the chrome bath although the current should be low.You then adjust to your required current.
SK Cheah- Hong Kong
2000
Dear Mr. Cheah,
Thanks for your help.
Regarding your suggestion No. 3, I found that if I first set the voltage at 4.5 Volts, then put down the rack, and then increased the voltage up to 7 volts, I did not get much burned-out nor the cloudy plating. But this method is very sensitive of trial and error for each different parts.
Is there a rectifier that we can set the voltage at certain value, and then we just vary the current ?
Thanks for your help.
Irwan.
Irwan Nusantara- Jakarta, Indonesia
2000
2000
Dear Irwan,
In the finishing industry, one should always know the surface area of each part that is to be plated.I might agree that the surface area of some parts are not easy to calculate but an approximate figure would suffice.
- To your first question,I have the following suggestion :
- 1)Try plating the same parts in one batch followed by a different part in the succeeding batch.Parts having the same surface area can be racked or plated together.
- 2)Parts that have too much difference in current requirements should not be plated together.In this case, your bath should be empty before the next batch of racks enter the bath.
- 3)Parts that do not have too great a difference in current requirements can be plated together although you have to determine this from experience or trial and error.
- 2)Parts that have too much difference in current requirements should not be plated together.In this case, your bath should be empty before the next batch of racks enter the bath.
To your second question:
To the best of my knowledge,I have not heard or seen a rectifier that have a fix voltage and the amperes can be varied.According to OHMS LAW, voltage is directly proportional to current and resistance.This means that if the resistance remains a constant(the parts you are plating in the bath),voltage will increase if your amperes increase and the voltage will decrease if your amperes decrease.
Perhaps if there is such a rectifier maybe someone from finishing.com may be able to help you out.
Regards.
SK Cheah- Hong Kong
Dear Mr. Cheah,
Thank you for your help.
Currently, we plate the same parts for each rack, and we plate only one rack for each batch.
However, yesterday, we noticed that the length of the plating anodes is longer than the racks, so that the current density at the bottom side of the rack is higher. Therefore, we shortened the anodes, and we got less burned-out.
Now, We are thinking to put an "Inductor" in series between the rectifier and the plating anodes, hoping that the inductor (coil of wire) will damp the currents sudden increase. Does it make sense ? Is it necessary ?
Thank you,
Irwan Nusantara- Jakarta, Indonesia
2000
2000
Dear Irwan,
Honestly, I don"t know whether it makes sense but I don"t think it is necessary. I am more convinced you should take a hard look at your solution and operating conditions. Perhaps, I will be able to help better if you supply the following information :
Bath composition: - Chromic acid : ? g/l - H2SO4: ? g/l - Cr+3: ? g/l Operating conditions: - Temperature : ? - Plating time: ? - Current density: ?
By the way, responding to your letter 6439 concerning trivalent chrome :
Trivalent cannot be replenished with chemical. It is produced naturally by electrolysis and its volume is determined by the ratio between Anode area and Cathode area.
Anode area equals Cathode area - Cr+3 is consistent
Anode area greater than Cathode - Cr+3 decreases
Anode area smaller than Cathode - Cr+3 increases
Regards
- Hong kong
Q, A, or Comment on THIS thread -or- Start a NEW Thread