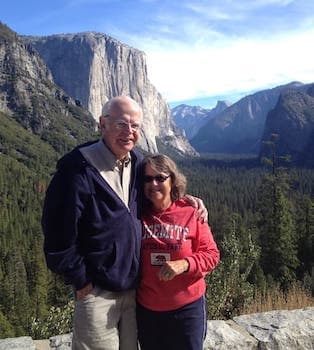
Curated with aloha by
Ted Mooney, P.E. RET
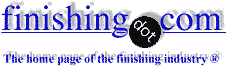
The authoritative public forum
for Metal Finishing 1989-2025
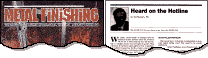
-----
Iron Phosphating - burner tube attack
Good Afternoon,
Richard, RGB Metallurgical UK.
I have a customer who is asking me why his mild steel burner tubes in an iron phosphating pre-paint bath are pitting and corroding after only 6 months. I do not have hands on experience of phosphating but it seems to me that when he tells me he has 1-2% phosphoric acid in the tank attack is going to take place , however, I also believe that the materials are an industry norm . Any ideas please?
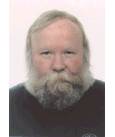
Richard Buster - Wolverhampton, United Kingdom
2000
Richard - I would first check to see if scale has started to build up in the burner tubes. If scaling is present, the trapped acids then start to corrode and pit. Usually, the turnover of an iron phosphate bath keeps the attack to a minimum, although many washers now are being built of SS or plastics. If your customer has scale, I would recommend descaling with an inhibited HCl to remove the scale and then start with a fresh charge of chemicals. Also, check to see that the operating temp isn't too high - this can cause premature scaling and the resulting corrosion.
Dan Brewerchemical process supplier - Gurnee, Illinois
2000
2000
Re burner tube pitting, a few thoughts:
1. pH of the phosphate process may be low due to excessive physical losses of solution form the spray zone requiring larger additions of chemical.
2. If process is Mo-free they are inherently more corrosive and should only be operated at low strength in mild steel equipment.
3. If sludge starts to cover the tube corrosion will occur
4. There may be inclusions in the tube material setting up corrosion sites.
Hope this helps
R
Roger Bridger- Croydon, UK
Have your customer check his MSDS sheet for the products in use. If he's using a phosphating product containing bisulphate or if his pH is below around 4.0 he can expect the problems you describe. Be sure he measures his pH with paper strips at least once, because fluoride ion on the tank can ruin pH electrodes, making them read incorrectly. I've seen a new steel washer almost ruined in less then a year by poorly chosen process chemicals, and a vendor unwilling or unable to realize what the problem was. MO, or Molybdenum, is a crutch. It is a rust inhibitor used in water treatment that should be left there. Molybdenum compounds interfere with good iron phosphate coatings and are only chosen for lines with very low operator effort or mechanical problems. How's that for firing up a lively discussion?
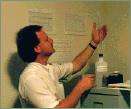
Jeff Watson
- Pearland, Texas
2000
Q, A, or Comment on THIS thread -or- Start a NEW Thread