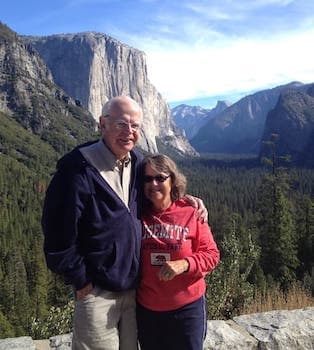
Curated with aloha by
Ted Mooney, P.E. RET
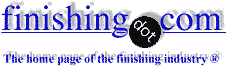
The authoritative public forum
for Metal Finishing 1989-2025
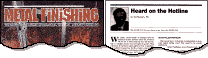
-----
Sealing over cured Zinc Plating + Chromate
Quickstart (no readers left behind):
Zinc plating is a very popular surface treatment because it is inexpensive, decorative, and offers sacrificial protection to steel. However, the zinc itself would quickly develop white rust, so it is virtually always "chromated".
Until the early 2000s the only chromates with significant corrosion resistance were based on hexavalent chrome, which is toxic & carcinogenic. New technology plus European RoHS (reduction of hazardous substances) standards precipitated a world-wide shift, and most chromating of zinc today is trivalent.
Trivalent chromating is higher technology than hexavalent chromating, is almost always proprietary, and almost all such proprietaries require an additional proprietary "post-sealer" step, probably involving zirconium or silicate based technology.
"Salt spray hours" refers to the fact that coatings are often required to pass a certain number of hours of standardized corrosion testing under ASTM B117 or ISO 9227 specifications without undue corrosion ("undue corrosion" being specified in the plating specification).
Q. We have a customer that is looking to switch all hardware to a 96-hour salt spray requirement. We originally quoted sending all current inventory out for stripping and re-plating with Fe/Zn 5ANS. The customer is asking if it's possible to just add the sealer over the existing parts to save cost of stripping and re-plating. So my question is:
Is it possible to add a sealer to parts after they have been plated, packed, and shipped?
I spoke with one company that said they only add sealer on wet chromate, the sealer would just spin off the dry parts. I have read a few comments on here that mention water based lacquer, is that different from a sealer?
Thanks for any input!
Applications Engineer - Spartanburg South Carolina
February 10, 2025
A. Hi Patrick,
Thanks for a very interesting question. It involves many factors, so we added a Quickstart to help readers of differing experience levels get up to speed -- please read that first.
Water soluble lacquer and today's proprietary topcoats on trivalent chromate are not the same thing, so that's where the confusion probably starts. Water soluble lacquers have been used before today's trivalent chromates even existed, and I don't see why they wouldn't help -- although whether you would achieve 96 hours remains an open question which would have to be tested.
There are many issues with your question though ...
• Some customers will not accept water soluble lacquers, perhaps because of conductivity or brightness issues.
• I wasn't aware that shops ever skipped the suggested topcoats.
• Are you sure the parts weren't hexavalent chromated, rendering them unfit for OEM automotive use, shipment to Europe, etc.?
• If water soluble lacquer doesn't offer enough protection, perhaps coatings like Protectaclear from Everbrite [a finishing.com supporting advertiser] will.
Luck & Regards,
Ted Mooney, P.E. RET
Striving to live Aloha
finishing.com - Pine Beach, New Jersey
Q. Hi Ted and thanks for such a quick response!
To address your questions,
1. I am not sure if they would accept a lacquer. I am not yet familiar with lacquer coatings, but reading up on them currently.
2. These parts were originally specified as clear zinc trivalent with no other criteria. Just commercial off-the-shelf parts.
And to my original post, I am aware that the most correct way to go about this issue is by stripping and re-plating (including the sealer) to the new requirements. But taking a literal approach to their requirement, they are looking for salt spray resistance of 96 hours to white rust. The Zinc plating just needs to be protected from corrosion by use of the initial clear coat and a sealer. Obviously the initial clear coat has been compromised in shipping and handling, but my thought is sending the parts for a sealer should provide some greater protection. We have said we cannot guarantee the 96 hours on these reworked parts, but it would be better than current performance until we can deplete the existing stock and order new parts to the new requirements.
Is there more to the chemistry and adhesion of the sealer than just being applied to the parts?
Or since I was told by one company that their sealer needs to be applied to a wet conversion coat, can we just have the parts go through another conversion coat prior to the sealant?
Applications Engineer - Spartanburg, SC
A. Hi again.
Hopefully all have learned that ordering plating to no specification, just "clear zinc trivalent" was a mistake and frequently leads to contract disputes because there is no industry understood & acknowledged "commercial" plating, and there are even old-fashioned trivalent chromates with expected corrosion at 12 hours of salt spray. Further, high strength hardware requires baking for hydrogen embrittlement relief, and if it's not sped'd it may not happen.
Unfortunately, chromate conversion coatings involve and require contact with the zinc itself because the zinc surface is what they "convert"; a chromate on top of an existing chromate or topcoat sealer won't work. When you don't know quite what you've got, applying a water soluble lacquer or a coating like the Everbrite one makes more sense to me. Today's trivalent chromates are so proprietary that I hate to make a prediction whether the reapplication of the "topcoat" portion must be done while the chromate is still uncured or not, but I tend to believe what you've been told about the wet conversion coat.
Luck & Regards,
Ted Mooney, P.E. RET
Striving to live Aloha
finishing.com - Pine Beach, New Jersey
Q, A, or Comment on THIS thread -or- Start a NEW Thread