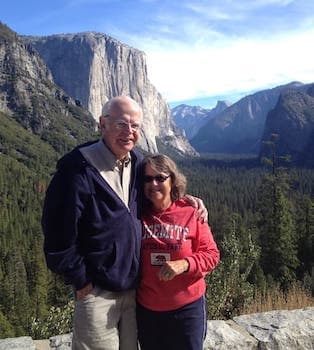
Curated with aloha by
Ted Mooney, P.E. RET
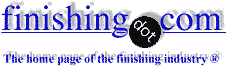
The authoritative public forum
for Metal Finishing 1989-2025
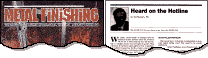
-----
Meaning of "Zinc electrolyte plating + leaching"?
Q. Hello.
I'm a engineer working on a fastener specification, but I have a limited knowledge about coatings.
I came across a fastener coating specification (A relatively old specification, from 1998) that states:
Electrolytic zinc coating + Leaching
I have no problem with the zinc specification, but what could be this Leaching post-processing?
Many other questions arise in my head: Is it some type of passivation? What is its purpose? Is it still used nowadays? There are better options? Is "leaching" a known and correct term? May it be a hexavalent chromate conversion coating?
This leaching follows a company's internal standard. Here are some additional details about it:
- Observation: Treatment as final operation of a component, piece or fixing element already submitted to a superficial treatment. As a post treatment, the surface protection characteristics applied on the component can't be damaged.
- Product 1
- Chromatic White
- Water dilution: g/L 1-40
- Application Temperature °C: ambient temperature
- Immersion time sec: 5-30
- Allowed agitation: Light
- Reservoir material: Carbon steel, polyethylene or PVC
- Product 2
- Chromatic yellow
- Water dilution: g/L 7,5-45
- Application Temperature °C: 16-43
- Immersion time sec: 5-30
- Allowed agitation: mechanical or solution movement
- Reservoir material: Steel, polyethylene, PVC or ceramic tank
- As it is alkaline salt, this product must be used only with safety gloves, safety eyeglasses, and
the necessary safety equipment for individual and collective protection, avoiding any contact of
the product with eyes or skin. In the case of contact, wash the area immediately with clean water
and go to the doctor.
- Processes sequence:
- 1 Electrodeposition
- 2 Washing at ambient temperature
- 3 Washing at ambient temperature
- 4 Nitric acid, 2-5 %
- 5 Washing at ambient temperature
- 6 Passivation with product 2
- 7 Washing at ambient temperature
- 8 Leaching with product 1
- 9 Washing at ambient temperature
- 10 Washing at ambient temperature
- 11 Washing at ambient temperature
- 12 Drying, centrifugal process or other.
- Notes:
- If balanced properly, it doesn't remove the chromate layer, giving a better resistance to corrosion."
Thank you very much for your attention.
Luiz SouzaEngineer - Sao Paulo, SP Brazil
January 16, 2025
A. Hi Luiz.
The effective hexavalent chromates were yellow/amber/honey colored -- the natural color of hexavalent chromate. It was fairly common to bleach out the yellow color, turning them more of less clear, by immersing in either hot water or a special leaching bath. Some people say if the color is gone the corrosion resistance is gone, but that's probably a moot point for you because this is probably no longer an acceptable specification anyway.
With few exceptions the world has moved on to trivalent chromates because of the toxicity of hexavalent chromate. So, depending on who your customer is, you probably need to switch to a trivalent chromate with topcoat. These are clear anyway and do not require leaching.
If you don't wish to retain a finishing consultant, a good starting point for a new specification is probably ASTM B633.
Luck & Regards,
Ted Mooney, P.E. RET
Striving to live Aloha
finishing.com - Pine Beach, New Jersey
Q, A, or Comment on THIS thread -or- Start a NEW Thread