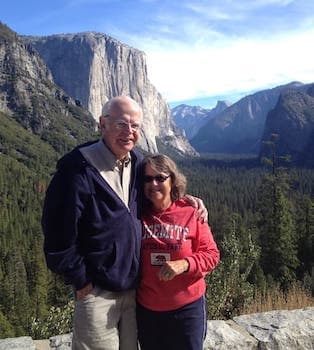
Curated with aloha by
Ted Mooney, P.E. RET
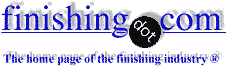
The authoritative public forum
for Metal Finishing 1989-2025
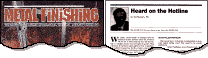
-----
Hobbyist Copper Plating on 3D Plastics: Help Fine-Tuning It

Q. Hey guys. I'm new to electroplating, and I'm working at the hobbyist level. I plan on using electroplating to coat 3d prints with copper (and later on, nickel) to build a personalized, wearable 3d printed replica of the mkII iron man suit from the mcu. However, I am just at the beginning of my electroplating journey, and need advice to get to that end goal. I just recently got my first mostly successful copper plate on a 3d death whistle, which I just thought would be a cool thing to test the plating process with. It went well, but left several questions and areas to improve, which is what I came here seeking advice about, addressed below.
Before I ask questions, here's some info about my setup:
I am using a copper sulfate solution of 0.9 gal distilled water, 28.8 oz copper sulfate, 28.8 ml sulfuric acid, and about 10 ml of midas brightener.
I prepare my 3d printed parts to plate by coating them in graphite paint until resistance is less than 5 kilo ohms, polish the coating, and then clean the surface in a water/degreaser solution, before drying with paper towel.
For reference, these are the anodes I am using.
That said, I have a few questions regarding the fine tuning of the process.
-How do I increase adhesion of the copper plating to the part? the plating on the death whistle wasn't readily peeling off but still scratches off with moderate effort and totally got destroyed when I later tried to burnish in a tumbler with steel shot tumbling media.
-Does anyone know where I can find good quality phosphorus doped copper anodes? Ive read online that these are the anodes you want to use when plating as opposed to fully pure copper because they are better at producing copper ions and reducing waste anode sludge. The amazon link previously shared is of the anodes I am using now; I was also wondering if there is any way to tell if the anodes I have are of sufficient quality or are phosphorus doped.
-Lastly, how can I burnish parts after plating without destroying them? I've seen the steel shot tumbling method done by others with success. In fact, my death whistle even came out shinier in the areas the plating wasn't torn off. How can I prevent this destruction in the future?
Any advice is much appreciated.
Thank you!
hobbyist - Tampa, Florida
January 5, 2025
A. Hi Joe.
Getting good adhesion is one of the prime requirements of electroplating. Many, maybe even most, automotive grills are copper-nickel-chrome plated and must endure temperatures from arctic to blazing tropical sun, as well as car wash brushes and gravel strikes. But special plastics and metallization techniques are employed as described in thread 315/50, "Automotive Quality Plating on Plastics". Getting sufficient adhesion to withstand tumbling by simply painting with graphite sounds a bit unpromising, but I lack personal experience with it, and hopefully another reader will chime in.
There is nothing wrong with buying good phosphorous copper anodes from a supplier like Carter Alloys Company [a finishing.com supporting advertiser], or scraps from eBay, but for a hobbyist plater I'm not surely it's actually necessary or has much to do with the adhesion issue. (The reason production platers use copper phosphorous anodes is that plain copper anodes dissolve a bit faster than the copper plates out, so over time the copper concentration keeps growing; when it gets too high the syrupy solution around the anode no longer conducts properly.)
Phosphorized Copper Anodes
on eBay
(affil link)
Luck & Regards,
Ted Mooney, P.E. RET
Striving to live Aloha
finishing.com - Pine Beach, New Jersey
Q, A, or Comment on THIS thread -or- Start a NEW Thread