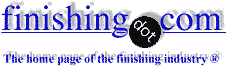
-----
Zinc plating & trivalent black chromate is giving poor salt spray hours
Quickstart:
Zinc plating is the most common finish for fasteners because it is thin, inexpensive, and offers cathodic protection. It is invariably followed by chromate conversion coating to deter white rusting of the zinc. The chromate is usually trivalent, not the older, toxic, hexavalent chrome. One available chromate color is black. The slang term "black zinc" is sometimes used.
A common QA test is that it pass a given number of hours of 'salt spray' as proof of its corrosion resistance. Salt spray tests and how they are conducted is described in specs including ASTM B117 and ISO 9227 ⇨
Q. I am from India, working in a nut manufacturing company doing non-cyanide alkaline Zinc barrel Plating. For the last year we are frequently facing white spray-like spots on our nuts after Plating. We are doing Trivalent Passivation and then top coat also.
We have tried many trials in the same line and offline but problem remains the same. After plating and finishing process, within two days this problem is observed. Initially it starts with two hex sides. After Plating and before passivation this problem is found on the nut. We have three rinses after Plating. A 2% Nitric dip is also given.
Supervisor plating shop - Pondicherry, India
November 27, 2021
P.S. We thank you for originally posting your inquiries on appropriate threads to help keep topics focused rather than wandering. But a better picture of your situation can probably be seen by combining them, so we've done that.
A. Hi Siva. 2% nitric sounds excessive; Robert Probert has noted on other pages that 1/4% to 1/2% would be usual, but I'm not sure whether it has anything to do with the problem.
I don't understand how you can say the problem takes two days to show up, but you can see it before passivating. Please clarify.
Still, little white dots which take a couple of days to appear are probably the beginning of white rust, so it sounds to me like for some reason the chromating isn't right -- but it could still be the rinses before it, the chromate itself, or the drying & packaging. Sorry I can't be of immediate help :-(
Luck & Regards,
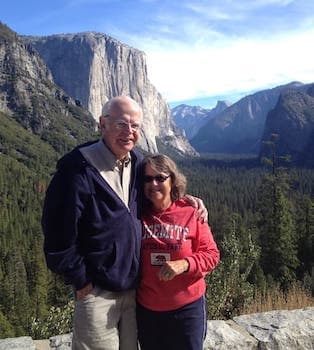
Ted Mooney, P.E. RET
Striving to live Aloha
finishing.com - Pine Beach, New Jersey
A. SIVA,
AFTER ALKALINE ZINC PLATE, NEED 0.5% NITRIC DIP -- MAKEUP NITRIC DIP EVERYDAY.
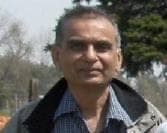
Popatbhai B. Patel
electroplating consultant - Roseville, Michigan
SST failure on alkaline zinc plating nut with trivalent black passivation
Q. We are doing Non cyanide alkaline zinc plating on MS nuts. Thickness is 10 microns to 12 microns.
We did trivalent black passivation with 10% concentrate organic polymer top coat.
We did neutral salt spray test and within 48 hours white rust is found, and then in 96 hrs red rust is observed.
What may be reason for quick sst failure?
Supervisor plating shop - Pondicherry, India
December 6, 2024
Q. What is the procedure to put a zinc Plated nut in SST? What is the minimum requirement with respect to handling?
We have to keep the untouched part in SST, or from any stage like after segregation, or after packaging or customer handling or assembled?
SST guarantee from supplier to Customer is at what stage of sample?
Does any specific standard explain these requirements?
Supervisor Plating shop - Pondicherry, India
December 6, 2024
A. Hi Sivakumar.
The first step is for the supplier and customer to agree what spec the plating is supposed to adhere to. Using accepted ASTM, ASM, ISO, or MIL specs is an excellent starting point, and usually such specs say what is to be tested and how the results are to be interpreted. Some specs are even highly detailed info about lot size, sample size, etc., effectively answering your question about segregation.
While nothing prevents a customer from requiring customized tests, or requiring retesting after packaging & shipping, the generally accepted industry-wide specs do not dictate that -- in fact the salt spray testing instructions usually require test parts be at certain angles, etc. As for handling, clean cotton gloves should be worn by everyone involved.
My suggestion is to find a spec you want to plate to, ask your customer to accept it, and get it written into the PO's and acknowledgement papers.
Luck & Regards,
Ted Mooney, P.E. RET
Striving to live Aloha
finishing.com - Pine Beach, New Jersey
Q. Salt spray failure: Non-cyanide alkaline zinc plating nut with trivalent black passivation and top coat on MS nuts. Thickness 10 microns to 12 microns.
We did trivalent black passivation with 10% concentrate organic polymer top coat.
We did neutral salt spray test and within 48 hours white rust found and then in 96 hrs red rust observed.
What may be reason for quick SST failure?
Supervisor Plating shop - Pondicherry, India
December 17, 2024
A. Hi again Sivakumar.
8 microns is for "moderate exposure" and 13 microns is for "severe", so I would expect 10-12 microns to do better than it's doing. But what does 10-12 microns mean? Is that the average or the minimum? If that is the average, you might find the actual minimum to be substantially less, and it ought to be measured.
Trivalent chromates are tricky, and black probably the most so. Are you using a single proprietary vendor for your zinc plating, chromating, and top coating process -- you probably should be ... and they should be helping you with this.
Luck & Regards,
Ted Mooney, P.E. RET
Striving to live Aloha
finishing.com - Pine Beach, New Jersey
Q, A, or Comment on THIS thread -or- Start a NEW Thread