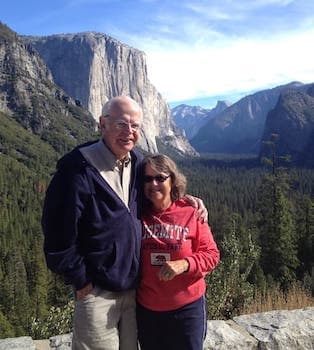
Curated with aloha by
Ted Mooney, P.E. RET
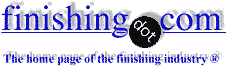
The authoritative public forum
for Metal Finishing 1989-2025
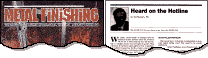
-----
Mixed metal pretreatment configuration
Quickstart:
Painting and powder coating will only work well on properly pretreated materials. The conventional pretreatment for bare steel is iron or zinc phosphatizing; for aluminum it is chromate conversion coating; and for galvanized materials it is zinc phosphatizing.
When practicality demands a single pretreatment for mixed-metal, zinc phosphatizing is the usual choice; even though it's suboptimal for aluminum, it at least cleans and etches it.
Q. Greetings!
I have a question on how to reach a favorable compromise in a situation where you have to chemically treat two kinds of metals prior to powder coating: aluminum and galvanized steel.
My jobshop does window/door and ventilated aluminum glazing systems. Next year we are supposed to launch a powder coating line.
The material to be powder coated is primarily aluminum linear extrusion (about 85% of the volume). The smaller part (about 15%) is galvanized steel from which metal sheets are made to later be installed in doors/windows (much like glass, but painted galvanized steel in this case).
It is worth mentioning that conversion coating is only needed for aluminum extrusion. The surface of galvanized steel does not need to be activated prior to coating, it just needs decreasing and rinsing, so that it can be coated right after this process. To cut it short, there is no point in high level pretreatment of galvanized steel in the context of our manufacturing.
That being said, we are planning to launch immersion baths for aluminum profile to be dipped it. That of course will include degreasing/etching and conversion coating with a rinsing stage after each function. The aluminum to be treated has little to no oil and grease on it. The galvanized steel has the standard amount of protection oil/grease in its surface (it is pretty greasy).
Right now it is unclear what kind of decreasing solution can be used to effectively clean and etch aluminum extrusion without attacking it too aggressively while also effectively degreasing galvanized steel (likewise, not eating up the zinc layer). As I understand, aluminum is usually cleaned and etched with acid solution instead of alkaline. And galvanized steel on the contrary is usually cleaned with alkaline solutions.
A separate series of baths for galvanized steel is not an option right now.
Can this configuration work in a typical layout that includes:
(1) Degreasing
(2) Rinsing with tap water
(3) Conversion coating
(4) Rinsing with tap water
(5) Rinsing with DI water
What kind of problems may appear if we are to exclude the stage (2) and rinse the material after degreasing in a stage (4)?
Will be very grateful for an answer or an advice.
Regards,
Employee - Dubai
November 13, 2024
by Samuel Spring
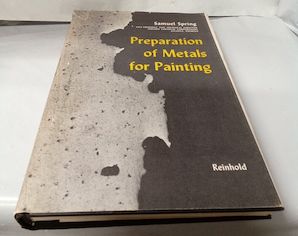
on eBay
(currently)
or AbeBooks
(rarely)
or Amazon
(rarely)
(affil links)
A. Hi Manbaa.
Although it is certainly best to give metals the most appropriate pretreatment for each individual type of metal, mixed metal treatment is fairly common. However, the usual mixed metal pretreatment is to do phosphatizing, even though the phosphate doesn't "take" on the aluminum. So in the case of aluminum and galvanizing, the usual mixed-metal approach would be zinc phosphatizing. Your situation is unusual though, because you intend to process far more aluminum than galvanized. I wonder if you could obtain aluminized steel or Aluzinc steel rather than galvanized and chromate it all.
Personally, unless you have strong experience to prove it, I do not share your confidence that you will be able to properly powder coat non-phosphated galvanized steel. It would come as a great surprise to me if galvanized steel "just needs degreasing and rinsing".
Luck & Regards,
Ted Mooney, P.E. RET
Striving to live Aloha
finishing.com - Pine Beach, New Jersey
Thank you Mr. Mooney.
Your answer was very helpful.
Q. After a deeper research I realized my initial approach would not consistently produce reliable pretreatment results to both aluminum and galvanized steel, which is the opposite of what we want to achieve.
We chose a short (and smaller tank volume) but completely separate line of tanks to degrease and apply a conversion coating based on zirconium to galvanized steel.
Aluminium extrusion would go through acidic degreasing/etching and trivalent chromium conversion coating steps. The TCP we plan to use is among the most common products which are mentioned on this forum.
Right now I am supposed to calculate project cost and cost efficiency. The cost of building this pretreatment line is petty straightforward to me.
What puzzles me is the methodology of how to calculate the cost efficiency of this process A.K.A. how much money the shop is going to spend on refilling conversion tank each month/quarter/year, knowing the estimated amount of square feet that is going to be powder coated.
I know my tank volume, and I know the appropriate concentration of the trivalent chromium which 3-6%. What is also known is the conversion coating weight that we aim to achieve which is 0,2-1 gr/m2. Recommended immersion time is 0,5 to 10 minutes. From this I can easily count the cost of the initial bath make-up.
I don't see how from these parameters it is possible to calculate how much surface area 1 gram of trivalent chromium concentrate can pretreat, if, for example, we choose to aim at the middle of each parameter (example: coating weight of 0,6 gr/m2).
Since what mentioned above is unclear to me, I chose another method of process cost calculation, which is to estimate the amount of carryover. Each 100 square meters immersed would theoretically produce 3,65 to 6,1 liters of carryover to the next tank. If 20 000 square meters is to be powder coated (and therefore pretreated prior to it) in one month, it means that the conversion tank carryover would amount to 730 to 1220 liters. We would therefore compensate this carryover and add deionized water with the addition of 3-6% trivalent chromium concentrate.
Please correct me if I am wrong. Which is the correct approach to such calculation in your opinion? I presume the factual result will differ from theory, but approximate knowledge of cost to operate is what I want to achieve now. Thank you in advance, hope it was not too confusing :-)
Shop employee - Dubai
December 9, 2024
A. Hi again. That is a followup question where I have no experience, never having been involved in day-to-day operation of such process lines. Hopefully a reader with such experience will jump into the conversation.
With your revised approach, though, the subject is no longer "mixed metal pretreatment" so you can search the site for "pretreatment of galvanized surfaces" and "pretreatment of aluminum" and see if those searches yield any helpful answers.
Trivalent chromating of aluminum is a well established process; however, it is usually proprietary, so I would expect that the vendors trying to promote it as an alternative to hexavalent chromating would be able to offer general numbers on cost to process per square foot compared to phosphating.
Zirconium pretreatment in lieu of phosphatization is relatively new, and I have no personal experience with whether it is fully compatible with galvanized surfaces, producing good adhesion of powder coating. It may be perfect -- sorry, I just personally don't know.
Luck & Regards,
Ted Mooney, P.E. RET
Striving to live Aloha
finishing.com - Pine Beach, New Jersey
Q, A, or Comment on THIS thread -or- Start a NEW Thread