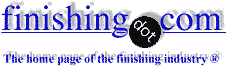
-----
Aluminum in the 1930's: "Deplated Finish"
Q. Finishing folks,
I work designing restorations of old buildings and have been researching something that may be of interest. I am also hoping this group can help me understand it!
For a brief period in the early 1930s, prior to the introduction of their 'Alumilite' anodized finishes, Alcoa advertised a 'deplated' finish for architectural purposes. (See their 1932 publication 'Aluminum in Architecture', available online at HathiTrust ⇨
The finish was described as dark, slate gray, and the process was proprietary. This has puzzled me and people in my world, since these features have long since weathered and the term has disappeared from use (at least in this context). The big question: what did these elements look like when new?
Fortunately, I was finally able to find some instructions in Alcoa archives out in Pittsburgh. I am not a metal finisher, but I am overconfident, so I followed the directions in my backyard. I am not sure if I can attach the original text so here is the gist:
-bath of 7.5% by vol. sulfuric acid
-work is anode, 1100 aluminum is cathode
-applied current density of 0.3 amps per square inch for 20 minutes at ~75° bath
-Worked as described. Here is a photo of the result.
The key to the process seems to be that the work was Alcoa's #43 alloy (today 443), 95% Al / 5% Si, which was hard for me to get. The 'deplating' removes the aluminum from the surface and exposes the silicon, resulting in the dark gray appearance.
My questions to you all:
-Anyone ever heard of this specific way of finishing aluminum before? Or did it completely die out?
-My big question: this process, to my untrained eye, seems very similar to anodizing. But why was I 'deplating' my aluminum instead of anodizing it? At first I assumed the anode and cathode were reversed in the two processes, but that doesn't seem to be the case.
Hope this is perhaps interesting. I can't tell if this process was a step on the way to modern anodizing, or a weird offshoot. Thanks in advance for any thoughts.
Architectural Conservator - Philadelphia, PA
November 15, 2024
A. Following up on my own thread because I may have found the answer to my own question.
If I am doing my math correctly, I think I was applying roughly twice the current density to my aluminum samples as is typically done when anodizing today. I found a 1987 article (Thompson, Xu, Skeldon, Han, & Wood, "Anodic Oxidation of Aluminium" Philosophical Magazine B 55, no. 6: 651-667) that states that at a critical current density, the Al from the anode goes into solution faster than the O2/OH can bond with it at the surface. So that's my best guess -- perhaps this finish came first because it was easy to see the results, and it took Alcoa awhile to figure out that if they ratcheted back the current, they were developing a coating that was actually protective. Don't know how they could have really known what was going on at the surface in the early 1930s, at the micron-level. Anyway, I welcome corrections if anyone knows better.
- Philadelphia, Pennsylvania
Preston, this sounds very interesting. I was wondering, if this is indeed not creating a protective anodize layer, how you were planning to protect it against further corrosion? I imagine that is the reason that the original pieces you researched this for need restoration. I hope to hear what solution you come up with!
Lab Rat - Fort Wayne, Indiana
December 19, 2024
Q. Great question! While replicating the deplated finish should be valuable as a visual benchmark for restoring buildings from this era, you are correct that it is unclear the best way to actually replicate the finish. I am hoping that others in my field will be able to figure this out, but a few stray thoughts:
-To your point about protection, my instinct is that it would probably be better to replicate the finish using a pigmented anodization process rather than a true "deplating" in order to get some durability of appearance.
-That said, the features most commonly deplated apparently large aluminum castings. If I were hired to restore the Empire State Building, I doubt anyone would let me take off all of the spandrel panels to immerse them --either for deplating or anodizing. Not sure how either method could be performed in situ.
-Barring immersion in a bath, people might have to develop workarounds to approximate the finish on site, maybe using patination protects such as are commonly used on bronzes. But then you get into clear protective coatings like lacquers and waxes and associated maintenance.
All of that said, I am far from an expert on the alternatives as my research was narrowly focused on this historic finish. I welcome suggestions!
- Philadelphia, Pennsylvania
January 2, 2025
A. Hi, Preston. We probably shouldn't let the name 'deplating' derail our thinking -- a bit of deplating does occur in anodizing, and the polarity is opposite of that used for plating, which may account for the name. You are correct that this process is in fact anodizing (although we usually use twice as high acid concentration and much lower current density these days).
The slate gray is a function of the material being anodized because silicon and other alloying materials don't anodize. Anodizing of castings does tend to produce a slate gray appearance today, and hard anodizing (which is thicker anodizing) of even most wrought or extruded alloys usually results in a slate gray to light charcoal appearance. Per the '420 rule' pf anodizing, 20 minutes at 0.3 ASI should give 1.2 mils thickness which is quite thick and would be expected to be quite gray except on exceptionally pure aluminum.
If you do a google search for "hard anodizing", then pick "Images" you'll see dozens of examples of the color of hard anodizing.
Luck & Regards,
Ted Mooney, P.E. RET
Striving to live Aloha
finishing.com - Pine Beach, New Jersey
Q. Hi Ted,
Thank you, this is helpful. It occurs to me that the gentleman who wrote the instructions for "deplating" in 1930 might not actually have understood what was going on, and misattributed the source of the color to the silicon.
My question to you: if you had to bet, would you guess that my "deplated" samples actually have an anodic coating on them? Or do you think they have simply been stripped of aluminum at the surface, as the author of the instructions believed?
I may be able to have the samples analyzed to find the answer!
- Philadelphia, Pennsylvania
January 30, 2025
A. Hi again. Even though the acid concentration and current density are not what we consider optimum after decades of experience, I'm confident that the parts which you 'deplated" are in fact anodized.
A simple V-O-M should indicate high resistance rather than good conductivity, and an eddy current thickness tester will actually tell you the thickness of the non-conductive anodized coating.
Luck & Regards,
Ted Mooney, P.E. RET
Striving to live Aloha
finishing.com - Pine Beach, New Jersey
Q, A, or Comment on THIS thread -or- Start a NEW Thread