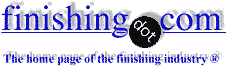
-----
Black Anodize Blemishes & Spots
Q. I have a part that is turned from an extruded bar of 6061-T6 Aluminum. The finish is black anodized per MIL-A-8625, TYPE II, CLASS 2. Per the specification the dye shall be uniform. My supplier is having issues with blemishes described as "speckled dye".
There are areas on the part which have bright blemishes where the dye is incomplete. The problem is intermittent, not showing up on every part in a batch. The blemishes also do not show up in the same surface from part to part. I have used a continuity test to verify the anodic coating (an insulative barrier) is present where the blemishes exist. So, I believe the part has corrosion resistance and this seems to be a cosmetic issue. Nonetheless the dye is not complete and is failing visual inspection.
My supplier has changed some process variables and procedures but has not found root cause.
I am here to ask for direction/suggestions/solutions to this issue.
- Richland, Michigan, USA
October 8, 2024
A. Hi Bill,
Thanks for letting us know that you did a continuity test. If you are doing quality control on incoming parts you might also get hold of a eddy current thickness tester
⇦ on
eBay
or
Amazon [affil links] so you can see how much anodizing there is on the part, rather than that just that it isn't totally lacking.
![]() |
The following example doesn't apply specifically to you but explains "walking the line", which is an obligation of the anodizing shop's management. Back when I was doing consulting I was retained by a shop whose erratic barrel nickel plating defects drove them bananas for weeks. They had a full time statistical process control guru who spent all day every day poring over his charts to no avail. |
Unfortunately it can be difficult to figure out what's wrong when neither you nor we are at the anodizing shop because the first step in troubleshooting is to walk the line, watching what the operators and machines may actually be doing differently from time to time that may be causing variations -- poor contact on some racks, bad hooks, some parts partially out of solution in some process tank, additions being made at the wrong time, processing on hold during coffee break -- the possibilities are endless and just looking around often needs to be the first step.
That gouge in the first picture, if the photo isn't deceiving me, is a great example because something dramatic probably happened :-)
My bet is if you schedule a trip there for yourself or someone in your company the problem will go away before you get there because the shop's management will check out the line to make sure all is looking & running well for your visit
Luck & Regards,
Ted Mooney, P.E. RET
Striving to live Aloha
finishing.com - Pine Beach, New Jersey
A. As an anodizer, when I see something like this (and in particular, if it is only these parts), I look at the incoming goods as well. There is a rather short little checklist to start off with.
1. Are the parts cleaned before arrival (Minimum free of chips, etc.)
2. How greasy do they feel? (Washed, or not?)
3. Does the surface appear flawless? (No water damage, etc.)
If that's not cause for issues. Then we go through the line, step by step. First verbally, talk about where potential issues could be. From cleaning/degreasing and all the way to Seal Rinse.
Then a physical trip to the Line, see what is going on. It's much more of a come-and-go task, as there is no point in lingering over an anodizing bath for 45 minutes, just to wait for the parts to re-emerge from the bath. Visually inspecting parts after each process. This doesn't have to be a "Down, off the rack, check EVERYTHING" but more of a "Look at the parts on the rack, between processes" kind of thing. See when the issue can be seen for the first time. And using that information to further our troubleshooting.
Some of it, looks like it could be poor rinse after anodizing and before colouring, which can give splotchy colouring. Some of it looks like White Spots, which -can- be galvanic corrosion.
The first of these issues is easy to combat. More rinse before colour, rinse with air agitation, multiple quick succession dips of the racks. What ever the anodizing notice making a difference.
The second issue can be one hell of a bear to deal with. It can be a tiny creeping current in a rinse bath, to mixing Titanium, Aluminium and Stainless Steel during processing. If this is the case for the tiny specs, one solution, can be a magnesium plate that the anodizer attaches to the bar (that holds the racks), before rinse after anodizing, and letting them stay there until the end of processing.
In regards to White Spots, there are many great articles on the World Wide Web that can help provide you with solutions and insights beyond this, as my suggest for a solution may not work. As it could also be caused by chlorides and about a dozen other things. As I said, one hell of a bear!
I hope this provides some insight and help in combatting the issues you are having. If it is indeed white spots, I do feel sorry for you.
Production Technician - Horsens, Denmark
Ed. note: As a starting point on the white spots, Robert Probert uploaded an article "White Spots on Anodized Aluminum".
Q. Thank you for the responses and detailed explanations. I will look into our capabilities on measuring the thickness of the anodized surface with an eddy current thickness tester.
Our quality engineer "walked the line" and made some progress with the anodizing vendor, but we have not eliminated all blemishes yet.
"That gouge in the first picture"; a gouge can refer to a deep cut or scratch made on a surface. In this case, it is a 'swipe' of undyed surface. I cannot feel this blemish with my fingernail. No material was removed. Something, a contaminate, leads to the separation of the dye from the anodized surface in this area.
- Richland, Michigan, USA
A. Hi again.
Glad it is only missing dye, not a gouge in the article. White dots in black anodizing are one thing, and between Robert Probert's article and M. Stammerjohann's insights you should have some good ideas. Totally random areas of no dye, as shown in several of your photos is something else though.
I think the most likely explanation is poor cleaning. I would suggest two ideas:
First is a serious investigation of whether silicone is being used anywhere. The cleaning sequences used in conventional anodizing lines will not remove silicone, so if a silicone spray is being used anywhere in the shop you will likely get splotches like this.
A second suggestion would be to manually preclean a batch of parts by scrubbing them with a tampico scrub brush
⇦ on
eBay or
Amazon [affil links] and a solution of pumice
⇦ on
eBay or
Amazon [affil links] and a small amount of detergent in warm water before racking them for the anodizing cycle. If the problem completely goes away, it is a cleaning problem.
Luck & Regards,
Ted Mooney, P.E. RET
Striving to live Aloha
finishing.com - Pine Beach, New Jersey

Q, A, or Comment on THIS thread -or- Start a NEW Thread