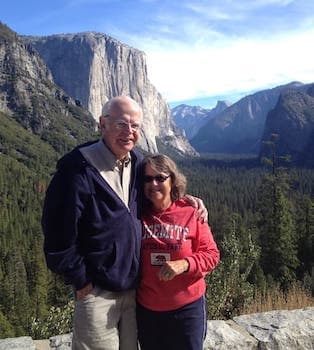
Curated with aloha by
Ted Mooney, P.E. RET
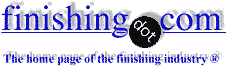
The authoritative public forum
for Metal Finishing 1989-2025
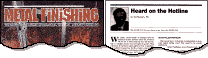
-----
Hazy white tips on long pins... alkaline zinc plating
Q. We have been having an issue with zinc plating pins on a rack line. They are approx. 3/8" dia and 16" long. The very tips on some (not the entire rack) have a matte, silvery-white grainy appearance. Zinc content is 1.9 oz/gal and caustic is 16.8 oz/gal.
I do not believe it is a bath quality issue. We have perfectly fine parts right next to bad ones.
I am new to the plating world and trying to learn as much as I can. Thanks in advice to any replies.
Mike A- Pennsylvania
July 29, 2024
Tip: This forum was established to build camaraderie among enthusiasts through sharing of tips, opinions, pics & personalities.
The curator & some of the readers who publicly share their info are unlikely to engage with posters who don't.
A. Hi Mike,
because the defect is on tips which are the high current density area of the pins, and
because it's a matte, grainy appearance
But if you're trying to learn as much as you can, please search the site for "Hull Cell" to learn how this can give you a better idea whether it is a bath quality issue.
Luck & Regards,
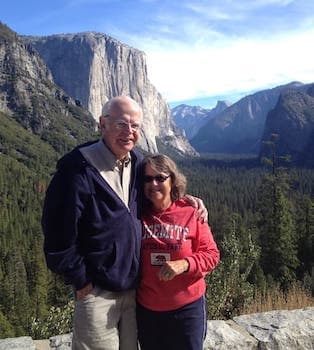
Ted Mooney, P.E. RET
Striving to live Aloha
finishing.com - Pine Beach, New Jersey
![]() |
A. Alkaline zinc bath, Electroplating consultant - Sterling Heights
Lab Tech - Pennsylvania |
Q. When we lowered the voltage, the LCD area (mid shank) would not plate properly. We could not find a voltage that was the sweet spot for these longer pins. We have much less issue running the shorter pins.
MikeALab Tech - Pennsylvania
August 1, 2024
A. Hi again,
As you recognized and as Popat suggested, the current density at those points is too high for proper plating. If reducing it causes improper plating in the low current density areas, there seem to be only two solutions:
1. Extreme agitation to allow higher current density, probably impractical in this case (you would need some sort of jets to create high velocity impingement of solution onto the tip area).
2. Reducing the ratio of high to low current density by racking differently or by using current grabbing thieves or current diverting shields of some sort. I personally think plastic shields are more practical than plating out onto thieves.
If the problem is very complicated, there is electrochemical modeling software available for purchase. I haven't used it but it apparently does something similar to finite element analysis to predict the current density at the various locations when you input your racking situation.
Luck & Regards,
Ted Mooney, P.E. RET
Striving to live Aloha
finishing.com - Pine Beach, New Jersey
A. Hello dear,
It's burning on high Current area. Please check voltage supply and distance between anode to cathode, after doing this if problem persists then please contact your chemical supplier. I have faced this problem when I was using Atotech chemistry, and problem was resolved after adding 3100 make (Atotech Product).
- Dubai
September 24, 2024
Q, A, or Comment on THIS thread -or- Start a NEW Thread