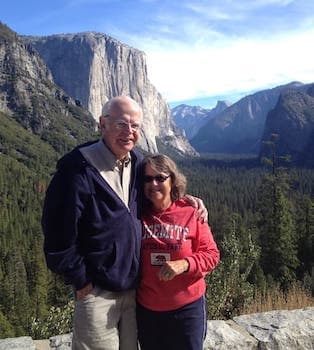
Curated with aloha by
Ted Mooney, P.E. RET
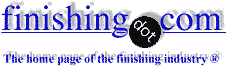
The authoritative public forum
for Metal Finishing 1989-2025
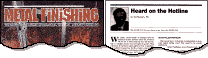
-----
Powder coat over galvanization

Q. I work at a powder coat facility and we are seeing this coming in from a customer (see pics). We know nothing about galvanization here so we're not sure what is going on.
⇧ Pic 1 is after 45 seconds blasting (glass bead) ⇧
⇩ Pics 2, 3, 4, is prior to blasting ⇩
What could be causing the peeling of the galv.?
B A Muse- DeWitt Iowa
May 22, 2024
A. Hi B A,
The proper pre-treatment between galvanizing and powder coating is zinc phosphatization, not bead blasting, but I'm not sure that I understand the background. This is not rework of old material which has been in the field, but these are brand new components with poorly adhering galvanizing?
Sorry that I do not have enough experience to know whether galvanizing should be able to survive 45 seconds of bead blasting; we'll have to wait for someone who has done it and can comment -- but pics 2 through 4 don't seem to my eye to illustrate poorly adhering galvanizing. Perhaps some adhesive tape testing would be a good indicator, but I'm not familiar with the specific testing tapes which are used. The AGA suggests a "stout knife test" at
https://galvanizeit.org/inspection-course/types-of-inspection/additional-tests#:~:text=Adherence%20Test&text=Testing%20of%20the%20zinc%20coating,or%20whittle%20the%20zinc%20coating
In general, it is problematic to galvanize material and then try to "simply" powder coat it because adhesion onto galvanizing tends to be a serious issue.
The AGA offers free booklets introducing the procedures for "duplex" finishing (galvanizing, then painting or powder coating) ⇨
Luck & Regards,
Ted Mooney, P.E. RET
Striving to live Aloha
finishing.com - Pine Beach, New Jersey
Q. This looks (from the images) more like the powdercoating is peeling off the galvanizing.
Bead blasting is not a good pretreatment for Powder coating (PC) over Hot Dip Galv (HDC).
Conversion systems where a chemical changes the surface to allow for better adhesion is better, but some companies do blast, not usually "bead" blasting, moreso shot blasting using garnet, or chilled iron. The blast needs to be very gentle or it removes the zinc.
You could test the peeling by using a thickness gauge on the parts where coating has been removed. If there's still 50-100 µm left, then that's likely zinc. If you don't have that available, then a drop of acid on the exposed metal (carefully) would fizz if that's zinc.
Alternately take some of the peeled coating and put in HCl acid and if its Zinc, then it is indeed the HGD coming off. If nothing happens, then this is likely the polyester (or whatever polymer was used in the OC process.
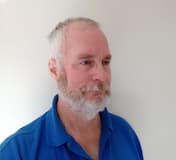
Geoff Crowley, galvanizing consultant
Crithwood Ltd.

Bathgate, Scotland, UK
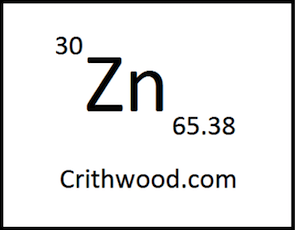
May 30, 2024
A. Dear B A,
Your blaster has worked at high pressure that is why the zinc layer has come off and if you paint then you should do sweep blasting not sand blasting otherwise you will see again; we are following same procedure in our company, sweep blasting after galvanizing.
- Doha, Qatar
June 15, 2024
Q, A, or Comment on THIS thread -or- Start a NEW Thread