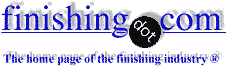
-----
Aluminum Anodizing Black Color Matching Problem

Q. Hello everyone
I mounted 2 racks of aluminum 110 pieces each to be colored black 40 minutes in machine. One rack on Monday and another is on Wednesday. Required thickness from customers is 15 µm. It came out very different in colors. One whole rack became black and another rack became blue. (Temperature was OK. pH was 6.14)
Now I'm very confused and nobody knows the right answer. I hope I get it here. I need your brain now
William Shatner [fictitious]- Stockholm, Sweden
May 25, 2024
Tip: This forum was established to build camaraderie among enthusiasts through sharing tips, opinions, pics & personality.
The curator & some readers who publicly share their info will be less likely to engage with those who don't.
combo magnetic & eddy-current coating thickness tester

on eBay or Amazon
(affil link)
A. Hi William. When black anodizing comes out blue the first step is to actually measure the thickness of the anodizing rather than assuming its thickness from the spec and supposed anodizing time. What is the actual anodizing thickness on the black and the blue pieces? Thanks.
Luck & Regards,
Ted Mooney, P.E. RET
Striving to live Aloha
finishing.com - Pine Beach, New Jersey
Q. The actual anodizing thickness found on the black pieces was 14 µm and on the blue pieces was 8 µm max. This was what I found. But does it make any difference if I found 15 µm on a blue piece ? Or what do you mean?
William Shatner [fictitious]- Stockholm, Sweden
![]() |
RECOMMENDED ANODIZING & CHROMATING BOOKS
for Shops, Specifiers & Engineers ![]() avail from eBay, AbeBooks, or Amazon ![]() avail from eBay, AbeBooks, or Amazon ![]() avail from eBay, AbeBooks, or Amazon ![]() avail from eBay, AbeBooks, or Amazon ![]() avail from eBay, AbeBooks or Amazon (as an Amazon Associate & eBay Partner, we earn from qualifying purchases) A. Hi again. I don't know why the thickness is only 8 microns (maybe the rectifier power failed or maybe there was bad contact to the rack for part of the cycle) ... but the lack of anodizing thickness *IS* the problem which made the parts blue. Q. It happened like this. We dyed the same material with same chemicals on 2 different times and we get 2 different results. All pieces on one rack was black which is approved but pieces on another rack are all blue which is not approved and make a big question mark. - Stockholm, Sweden |
Q. Hello everyone.
It says that a pH of 6.00 is an ideal for anodizing. My questions are:
What are the effects of low pH (less than 6.00) and high pH (above 6.00) on aluminum black anodizing during the process of sealing the pores on material? Does low/high make shift the color or what will be the reactions of low and high pH on material?
- Stockholm, Sweden
May 27, 2024
? What kind of sealing bath do you use? Most likely you use cold sealing. Up to me, source of problem is cold sealing. Please let me know your sealing
ALAATTIN TUNA- TURKYE Sakarya
June 5, 2024
We use warm sealing method.
William Shatner [returning]- Stockholm, Sweden
June 6, 2024
A. Agree with Ted. this color difference should be mainly caused by the ano film thickness.
Clark YuANO Engineer - Shanghai
June 13, 2024
A. I suspect source of problem is "low micron as 8 mic". Normally, even if a profile black anodized as 8 micron you would not get blue/purple color as your inquiry. My quess is this rack which got blue/purple one cold sealing duration time is much more normal sealing duration. As similar reason we always keep blackened anodized racks in cold sealing bath less than normal time such as instead of 15 min we keep 10 min due to prevent this problem. So even if you anodized 8 mic profile you will get brownish color instead of black color due to small pore structure
ALAATTIN TUNA- TURKYE Sakarya
June 26, 2024
If you guys can figure out how to dye anodizing a good black when it is 8 microns thick and less, hundreds of shops around the world who are bearing the substantial extra cost of anodizing to 15 microns thickness will thank you!
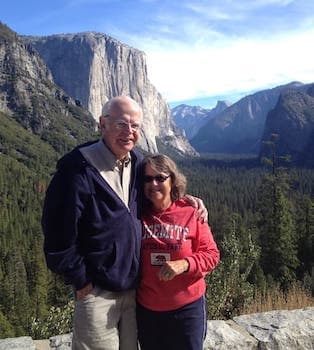
Ted Mooney, P.E. RET
Striving to live Aloha
finishing.com - Pine Beach, New Jersey
A. Alaatin, the color you get with too few microns depends entirely on how the black dye is made. Some blacks are Blue, some blacks are Red. Black in itself is not "Black" but simply a high enough concentration of a dark pigment. If Black was actually BLACK, you'd probably see a grey with too few microns.
And you speak of Cold Sealing while replying to a post that states that they use Warm/Hot Seal.
Also, by lowering your sealing duration, are you not sacrificing longevity of the anodizing and colouring? There are typically a thousand good reasons why someone has dictated the longer sealing time, contrary to your shorter time.
- Horsens, Denmark
July 1, 2024
Thanks, M Stammerjohann.
Alaatin is an architectural anodizer who uses, if I recall correctly from previous threads, two-step anodizing which relies on inorganic dyes. I am not very familiar with that technology, but I imagine that he may be correct about brown color in two-step anodizing with inorganic dye. I think most architectural anodizing is greater than 15 microns anyway.
But I 100% agree with you regarding the colors when anodizing and using organic dyes.
Luck & Regards,
Ted Mooney, P.E. RET
Striving to live Aloha
finishing.com - Pine Beach, New Jersey
![]() |
A. Absolutely, Two-Step Coloring or Electrolytic tends to go more brown-ish if using Copper or Tin as the metal salts. I am not quite sure what a cobalt would produce however. - Horsens, Denmark A. Stammerjohann, I have been using inorganic dye (tin sulphate) more than 15 years on anodizing line. I have not any experience in organic black dye process. If you use organic dye then your comment can be true. I respect your criticism and comment but I responded to this inquiry according to only my own experience. I insistently say again low coating thickness means as 7-8 microns narrow pore structure so tin deposit won't be enough for black coloring; that means you will get brownish color. Therefore to obtain black color, anodizing thickness must be 15-20 mic as Ted said. It's proven scientific fact... - TURKYE Sakarya July 4, 2024 |
Q, A, or Comment on THIS thread -or- Start a NEW Thread