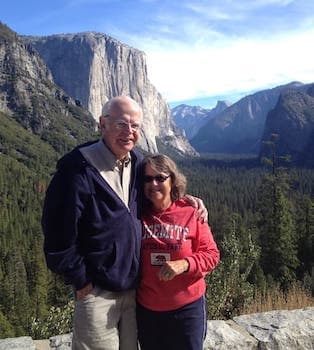
Curated with aloha by
Ted Mooney, P.E. RET
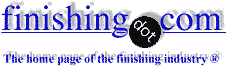
The authoritative public forum
for Metal Finishing 1989-2025
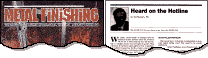
-----
ZrN has sufficient salt spray test resistance but TiN doesn't
Q. Hi all,
I have a question regarding my situation.
I'm producing pvd coating for decorative purpose on the following substrate: brass raw material + galvanic Ni-Cr layer (thickness 20 µ for Ni, and 0,4 µ for Cr) + manual brushing procedure with Scotch Brite.
The deposition process has the following steps: heating step, Etching step, metal interlayer, top coat of nitride.
I've noticed that TiN top coat is not able to reach 50 hours in NSS Corrosion test but ZrN is able to reach that exposure time without corrosion phenomena on surface.
Do you have any suggestion to improve the resistance of TiN topcoat to this test? Is it possible to reach 100 hour in NSS?
Thanks in advance for your time.
- Novara Italy
March 19, 2024
? Hi E,
I don't have an answer for you but I do have a question: When you say it fails NSS test, what is the evaluation criteria? Do you quote any accepted standard for the evaluation or, if not, can you tell us exactly what your internal spec says regarding acceptance vs. failure?
Most standards seem to quote specific evidence of corrosion as failure, and it seems unlikely that 20 µ plus 0.4 µ of chrome would allow any corrosion in 50 hours, so I'm assuming you have some sort of visual standard for how well the PVD top layer should look?
Luck & Regards,
Ted Mooney, P.E. RET
Striving to live Aloha
finishing.com - Pine Beach, New Jersey
![]() |
Q. Hi Ted, - Novara Italy March 20, 2024 A. What is the PVD technique used? The arc technique produces macroparticles which renders coating rough and may also make it porous especially when the coating is thin. However this effect would be quite less for ZrN compared to TiN as the melting point of Zr is higher. Increasing the thickness of TiN coating may help. This would not be an issue if you are using sputtering technique. - Bangalore Karnataka India March 20, 2024 |
![]() |
Q. Interesting about the Zr melting point. - Novara Italy March 20, 2024 A. We did some salt spray testing more than a few years ago comparing ZrN, TiN and TiAlN deposited on carbon steel test coupons. TiAlN was about the same as uncoated carbon steel, the TiN was better (lasted about two hours). ZrN lasted about 16 hours without any rust, though the 8 hour sample showed a bit of rust. Best consider increasing your nickel layer or going to a duplex nickel plating. ![]() Jim Treglio - scwineryreview.com PVD Consultant & Wine Lover San Diego, California March 20, 2024 |
Q. Thank you Jim for your experience.
The ISO 10289 that I've cited before explains the differences between the NSS and ASS, and it defines the scope in this way:
- NSS as a test regarding the good quality of the coating and its corrosion;
- ASS as a test regarding the barrier effect of the coating and its protective qualities.
What do you think about it?
Thanks
- Novara Italy
March 20, 2024
A. Let me answer your question this way: I worked with a faucet manufacturer for a few years. The bulk of their substrates were brass, plated with nickel and chrome as you describe. They did not use TiN on any of their faucets because 1) it is too hard to strip and 2) no one likes the color on faucets. So even if TiN can pass the corrosion test, why would you want it?
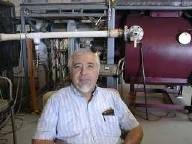
Jim Treglio - scwineryreview.com
PVD Consultant & Wine Lover
San Diego, California
March 22, 2024
Q, A, or Comment on THIS thread -or- Start a NEW Thread