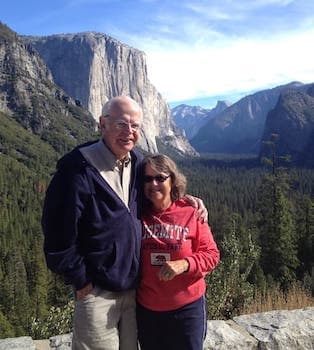
Curated with aloha by
Ted Mooney, P.E. RET
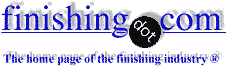
The authoritative public forum
for Metal Finishing 1989-2025
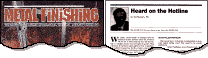
-----
Electroplating as forge welding prep
Q. I'm attempting to Nickel plate stainless steel or high Cr steel parts (440-C, AEBL, D2). It is very important for my process that I prevent oxide formation, as it will cause welds to be weak or to fail entirely.
Would adding Ammonium Chloride (as I've seen in brass plating) to an electrolyte of distilled water and baking soda remove oxide during Ni electroplating?
Are there alternative chemicals (that do not contain any Oxygen) which I can use instead of distilled water or white vinegar to make the electrolyte? My thinking is that I can use such a chemical in combination with Ammonium Chloride or instead of it to remove oxide (Ammonium) or prevent it entirely (alt chemical).
- Shelton, Connecticut
March 6, 2024
A. Hello Dyami.
I'm confident that nickel plating is an appropriate step (I once designed a very large nickel plating line for a steel mill which produced stainless-clad hot rolled steel by nickel plating hot rolled steel plates and stainless steel plates, and then rolling them together with a process probably pretty similar to your forge welding.
Although I know nothing of forge welding, I can appreciate its need for oxide-free surfaces. But I think there is a misunderstanding somewhere along the line about electroplating and oxidation. Electroplating does not cause oxidation -- quite the reverse, it's a reduction process. Further, the substrate needs to be free of oxide for the electroplating to work properly. Dipping the parts in HCl, followed by very quick rinsing, and quickly into the plating tank will do it.
But plating onto stainless steel is difficult. You'll need to use a conventional Wood's Nickel Strike (search the site), followed by a conventional nickel plating bath -- no baking soda, ammonium chloride, or vinegar.
I think that minimizing oxide formation on the nickel plating (if necessary) can be achieved by quickly wrapping the parts in stainless steel heat treat foil
⇦ this on
eBay
or
Amazon [affil links] .
Luck & Regards,
Ted Mooney, P.E. RET
Striving to live Aloha
finishing.com - Pine Beach, New Jersey
Q. I will definitely look into the conventional woods nickel strike, but there's something I'd like to clarify.
My understanding is that an incredibly thin layer of oxide forms rapidly on metal immediately upon exposure to oxygen, whether that be in air, water, vinegar, or anything else that contains oxygen. Were it not the case, you could clean and polish metals and then press them together to form a permanent bond, as is possible in the vacuum of space.
I might be getting hung up on words here, but electroplating is an oxidation REDUCTION process. In my mind, reduction is not the same as elimination. Could you clarify for me whether electroplating REDUCES the total amount of oxide to an acceptable level in which plating can occur, or ELIMINATES it completely when performed correctly? I just want to make sure I'm understanding this correctly, as I do not have a chemistry background to speak of.
To add additional context to my interest in nickel electroplating:
When forge welding most common steels you can use flux (Borax) to remove metal scale (oxide) from in between layers that have been tack-welded together (just enough to keep them from moving around. You can even use bailing wire, but with stainless steels the metals need to be thoroughly cleaned and de-greased before being sealed within a metal "canister" to prevent additional oxidation when it is heated. Even then, at least as it was explained to me, the best you can do is heat the billet (layers of cleaned metal you want to weld together) to just under melting point for the stainless steel being used and then deform (hammer it or press it with hydraulics) to break up the thin oxide layer the stainless steel will inevitably have from atmosphere exposure (oxygen in the air) regardless of how well it has been cleaned in preparation. This forms a bond AROUND the oxide, but it still traps oxide within the billet you have just formed.
If possible, I would like to use electroplating to completely remove ALL the oxide between the nickel plating and the metal that has been plated. I hope I'm not becoming too wordy.
- Shelton, Connecticut
March 8, 2024
A. Hi again.
When it is said that electroplating is an oxidation/reduction process it doesn't mean that it reduces oxidation, it means that the process at the anode is oxidation, and the process at the cathode is reduction. And while 'oxidation' can mean formation of oxides, it doesn't necessarily mean that. It actually means that electrons are removed.
I don't know much about forge welding, but I think there is no oxide between the substrate and the nickel plating.
Luck & Regards,
Ted Mooney, P.E. RET
Striving to live Aloha
finishing.com - Pine Beach, New Jersey
I think this clears the process up for me. Thank you for all your help.
- Shelton, Connecticut
March 10, 2024
A. Perhaps rather than looking for a coating of metal that is corrosion resistant, you should look for a metal whose oxide is easily removed with flux. Typically the way corrosion resistant alloys prevent corrosion is by forming a stable oxide coating. From the sounds of it you are looking to make some Damascus steel, so various layers of chemical resistance should not be an issue for you. However, it must be said what you are looking to do sounds very expensive for a relatively minor gain.
I would be looking into metals with reactive oxides, perhaps plain zinc or if you can find someone to do it iron. I would suggest a thin coat of zinc with no sealant/chromate coat, but Ted likely has better ideas.
- Ballarat, Australia
March 12, 2024
Q, A, or Comment on THIS thread -or- Start a NEW Thread