|
A. Your customer seems to have a correct understanding.
Passivation treatment alone will not likely be very corrosion resistant at the heat affected zone (HAZ) on either side of the weld (the discolored area). This is because a passivation treatment works to make sure that there is a good layer of the passive chromium oxide on the surface of the metal. At the high temperatures that are reached in the HAZ area during welding, much of the chrome is depleted by reacting with the carbon in the metal and to precipitate a chromium carbide. This precipitated chromium carbide does not react in passivation solutions to form the chromium oxide layer that is desirable. So, that HAZ area ends up not being as resistant to corrosive attack as the stainless steel around it. Using L-grade stainless as a raw material (304L, 316L, etc.) is helpful because there is less carbon in those materials that would be available to react with the chromium, but it is not the entire answer.
There are multiple ways to treat stainless welds to restore a good chemically-resistant surface prior to passivation. Good search terms will tell you what you need to know theoretically- like "stainless heat affect zone", "stainless chromium carbide precipitation", "stainless chromium depletion", "weld treatments for stainless steel", etc. The safest and most effective way in my opinion is to use a stainless steel electrolytic weld-cleaning machine and wand to clean the welds using proprietary solutions that work with the machine. There should be no discoloration when you are done with that step and the entire part is then ready for passivation.
Without a weld-cleaning machine, it is better than nothing if you can at least clean up the heat discoloration using a NEW stainless steel wire brush and remove the discoloration manually before passivation. You would need to do a DI water immersion test after passivation or some other suitable test to make sure that the manual brush treatment of the weld area was sufficient. If you are a job shop that only does the chemical dipping portion of the job, and if you use nitric acid for passivation instead of citric, then some shops are successful if they precede the passivation dip with a stainless steel pickling dip in a nitric-hydrofluoric acid solution. Note that HF is quite dangerous in a different way than other acids, so it is not something I would casually recommend unless you already use some of that acid elsewhere and you have good procedures for HF handling. Also, you will of course want to make sure that the customer accepts whichever method you intend to use before you change your procedures.
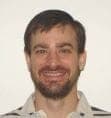
Jon Barrows, MSF, EHSSC
Kansas City
A. Micheline,
I think this is a question that is highly disputed.
First, let's review. Due to the high temperature of welding, on either side of the weld you get a "heat effected zone" (HAZ) where the alloy is not quite to the full melting point, but can be above the melting point of some of the individual metals in the alloy composition. Except for very specific alloy mixes (called "eutectic") this actually does create a semi-liquid condition, and the metal structure will indeed end up something different when the alloy slowly cools again. (Cooling rate can make a huge difference with metals and alloys.) With stainless, the main consequence here is a loss of corrosion resistance due to the crucial chromium getting trapped in the wrong form or wrong structure. I've heard various technical explanations for this, though the one I've seen most often refers to the formation of chromium carbide. The secondary consequence is that this carbide formation (or whatever it is) becomes quite visible on the surface in the form of typically blueish or brown heat discoloration, sometimes called heat scale.
In theory, the weld line itself ought to be similarly affected as it too is cooling down from high temperature, but in reality you do tend to get corrosion more in the HAZ adjacent to the weld than on the weld itself. Not good either way. The severity of the HAZ can also vary greatly.
I think a lot of people associate the visible heat discoloration with the loss of corrosion resistance, and thereby also associate the removal of the heat discoloration with the restoration of corrosion resistance. However, this would be a false syllogism.
Again in theory, if appearance is no concern, one should be able to passivate over the top of the heat discoloration, removing whatever active iron has segregated up to the surface, and the corrosion resistance will be restored. However, under the circumstances it's a little understandable for people to either 1) see discoloration and assume it equates to being a problem or 2) doubt that a process that does not remove the discoloration is adequate. I think the jury will remain out on that without a thorough study on the matter.
On the flip side, merely removing the discoloration may or may not help, corrosion-resistance wise, to varying degrees. Supposedly just beneath the discoloration is a layer of alloy from which the chromium has been sucked out (going to that chromium carbide in the scale layer) which having been exposed is going to be even more susceptible to corrosion. Therefore this layer must also be removed, and again supposedly whatever you are using to remove the discoloration itself may or may not remove it effectively. Personally I think some folks make too much of this layer as a concern, though, and I would expect it to be easier to remove than the heat scale itself, not harder.
Regardless, assuming that all layers affected by the heat are removed, you are still left with a fresh stainless surface of the raw alloy composition, which (depending on the grade) may be decently corrosion resistant already but will still benefit from a passivation treatment, same as any stainless surface after cutting, bending, grinding, polishing, etc.
To sum up, if you prefer to remove the heat discoloration through whatever method, and then passivate, that's great, you will be fine, keep doing it that way. If you want to save a step by leaving the heat discoloration on there and passivating over it, there's a chance it won't be quite as good but probably it will be just fine for most purposes. However there's no strong argument to favor leaving the discoloration there if you'd rather remove it. You're certainly not going to get a BETTER result by leaving the discoloration there.
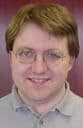
Ray Kremer
Stellar Solutions, Inc.

McHenry, Illinois
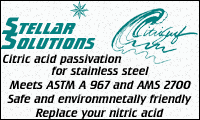
|