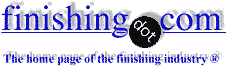
-----
How to deal with galvanizers waste acids
Q. Increasingly, across many countries, I'm finding the issue of disposal of waste acid is a problem for hot dip galvanizers. Mainly in HCl, the most common acid used (exception USA where a few still use H2SO4), the "waste" acid is usually about 2-4% HCl, some Zinc chloride, and iron chlorides all in aqueous solution.
The volumes can be huge, thousands of tonnes a year per plant.
Traditionally contractors have removed the waste by road tanker, where they mostly neutralise, filter off solids and liquid remaining goes to sewer drain, and solids to landfill. Environmental limits on these two outlets have closed up, such that neither landfill nor sewer are attractive, at least not at reasonable cost. This seems to me a great opportunity for someone to resolve this issue for the industry. The application of such a solution is international. The presence of zinc chloride has caused problems in some suggested schemes, but I think that problem is likely to persist. Most galvanizers need to strip something, even if only jigging, and keeping Zn contaminated acid separate is difficult. So who will solve this industry wide problem and become a billionaire in the process?
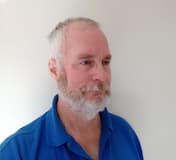
Geoff Crowley, galvanizing consultant
Crithwood Ltd.

Bathgate, Scotland, UK
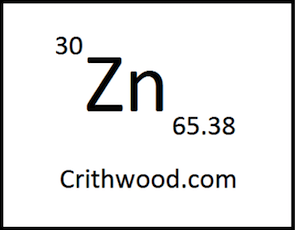
December 12, 2023
A. Hi Geoff,
Welcome to the club. Electroplaters have had to deal with similar waste streams for decades. Zinc is the most commonly plated metal, and zinc chloride based plating baths are one of the most popular. Platers also strip rejected zinc plating in their HCl tanks much as you describe.
There has been little success with treatment methods other than neutralization and precipitation of the solids, filtering the precipitate and landfilling it.
However, you might want to investigate 'acid extenders' -- these are primarily proprietary additives that can be used in the acid tank to make the dissolved metal precipitate in situ, significantly increasing the life of the acid.
Luck & Regards,
Ted Mooney, P.E. RET
Striving to live Aloha
finishing.com - Pine Beach, New Jersey
Q, A, or Comment on THIS thread -or- Start a NEW Thread