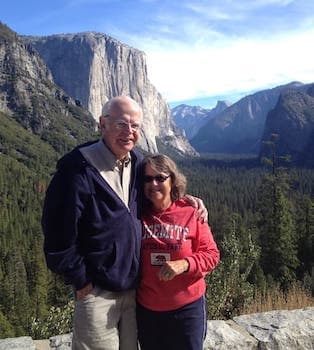
Curated with aloha by
Ted Mooney, P.E. RET
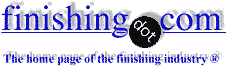
The authoritative public forum
for Metal Finishing 1989-2025
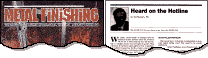
-----
Zinc adherence defect on edges of galvanized steel sheet

Q. I'm an intern and my mission is to find the root cause of a zinc adherence default. The problem is that in one line the zinc deposit is higher in thickness by 20 times in the extremities than in the middle of the galvanized steel sheet, this causes the zinc on the edges to peel off during the bending test.
What do you recommend for me to base my research on? And what could be the cause of this defect ?
- Casablanca, Morocco
February 17, 2023
A. Hi Asmae. As our teachers & professors constantly teach us, always make sure you clearly understand your own question before asking it and that the person answering the question properly understands the situation, or the answers you receive will only mislead you :-)
Some people sometimes call zinc electroplating 'galvanizing'. But you are speaking of "post-fab hot dip galvanizing" -- dipping discrete individual sheets of steel into a kettle of molten zinc -- right?
Luck & Regards,
Ted Mooney, P.E. RET
Striving to live Aloha
finishing.com - Pine Beach, New Jersey
Q. Thank you Mr. Mooney for your answer.
I'm talking about continuous hot dip galvanizing process in molten zinc alloy (2 % Aluminum). Sorry for the usage of the word 'steel sheets', the product to be galvanized are low carbon steel coils.
They are first of all chemically treated with chlorhidric acid to remove iron oxides and then are cold rolled, then the coils are thermally treated to degrease and restore the coils' mechanical characteristics lost by cold rolling. The adherence defect was first noticed in the edges of low thickness coils but now it's noticed also in higher thicknesses. I'm not sure of the later statement all of the data I have are from past campaigns. There were some issues with the furnace and now they installed a new analyzer for pollutants. Yes the frequency of the defect is lower now, but they are still looking for its root cause.
Thank you for your time
Regards.
- Casablanca, Morocco
February 19, 2023
A. Hi again. Thanks for the clarification; I think readers now understand your situation clearly enough to not mislead you.
Unfortunately I have no actual experience in continuous hot dip galvanizing, but my understanding was that the thickness is "wiped" down to the desired value by various sorts of wipers & knives as the sheet exits the zinc kettle -- so the originally described problem of thickness 20X as great on the edges sounds to me like a mechanical defect in the wiping arrangement.
In the finishing processes with which I am most familiar, although poor cleaning/degreasing is not the only cause of poor adhesion, it is the most common. Is there any visible oil in the acid tank? There may not be a good cleaning test available on your continuous processing line, but a common way to test whether cleanliness is the problem is to do a good pumice scrub of a piece or a section immediately before processing. Beyond that, is there a flux step before the hot dip?
Luck & Regards,
Ted Mooney, P.E. RET
Striving to live Aloha
finishing.com - Pine Beach, New Jersey
Q. Hello again
No, there's no oil visible in the acid tank nor a flux treatment ... I think if the problem was in the pickling process it would affect all of the surface of the coil not only the edges.
Note : There's two hot dip galvanizing lines; one shows the defect and the second doesn't the only difference is the thickness of coils, the line in question treats lower coil thicknesses.
Regards
- Casablanca, Morocco
February 20, 2023
Q, A, or Comment on THIS thread -or- Start a NEW Thread