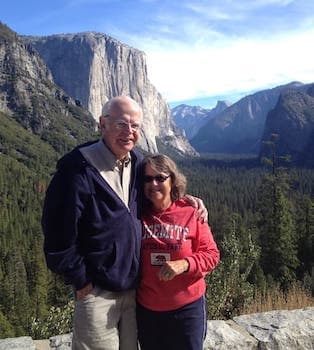
Curated with aloha by
Ted Mooney, P.E. RET
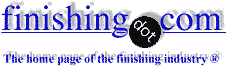
The authoritative public forum
for Metal Finishing 1989-2025
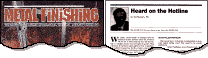
-----
Electroplating Copper onto PVD/Sputtered Gold Substrate
Q. Hello I am a Systems Engineer with a degree in Physics.
Currently we are attempting a subtractive process where we sputter titanium on glass and then sputter gold, then electroplate the gold with copper in a sulfuric acid bath.
If the electroplating is successful I place the now mostly copper substrate into Hydrofluoric acid to etch away the glass. This also seemingly removes any titanium.
However inconsistently we have been having some issues with electroplating, we have been seeing strange reactions such as our cathode (our glass/gold sample) seemingly oxidizing any copper that does electroplate successfully, this happening with a fresh anode of 99.995% copper, fresh sulfuric acid and using new tubing for our pump. Other issues include a non-uniform electroplating surface where the surface that successfully electroplates is bumpy and has texture differences throughout the sample.
Not sure what to make of it, going forward we will try electroplating copper onto sputtered copper. However if someone could help us with these problems or point us in the right direction for learning resources that would be great as we still have some remaining samples to experiment with and to improve our process in case we don't understand something. I will list out the conditions of the bath below:
Current source pulse generator: unipolar, 50mA, .05V, 5mA/cm^2 current density
sulfuric Plating: copper sulphate
⇦ this on
eBay or
Amazon [affil links] 25%, H2O 65%, Sulfuric Acid 10% bought from transene
Peristalic pump
Glass container with teflon lid
Magnetic hotplate spinner (only spinner on)
Copper Anode: 99.995%
Process:
Condition anode with receiving cathode to remove oxide on anode, 10 min.
Clean gold sample with acetone
⇦ this on
eBay
or
Amazon
[affil links] Warning! highly Flammable!
and IPA
Place sample in sulfuric bath as cathode.
I appreciate the help. If I am missing any important information let me know.
- Ann Arbor, Michigan
March 22, 2022
A. Hi Ricky. As you know, when you have a complex problem, the thing to do is try to segment it into separate smaller problems which can be addressed and solved individually. Not being from the industry, what you might not yet know, is how to best divide that problem into that set of smaller steps.
I would suggest that a good way to do that division might be to:
1). first prove to yourself that you have a workable plating solution;
2). then that have developed a workable methodology for employing that plating solution to electrodeposit onto 'easy' substrates; and
3). if necessary, figure out what if anything is special about your sputtered gold substrate that will require adjustments to what you've learned.
I think you should try to address step 1 by obtaining a Hull Cell and clean brass hull cell panels, and see if you can get your plating solution to deposit a satisfactory plating layer. Then you can move on to step 2 and see if those clean brass Hull Cell panels, perhaps snipped and/or shaped can be successfully plated with your methodology. After the first 2 steps are solved, you will know if your substrate presents new issues that remain to be resolved.
Luck & Regards,
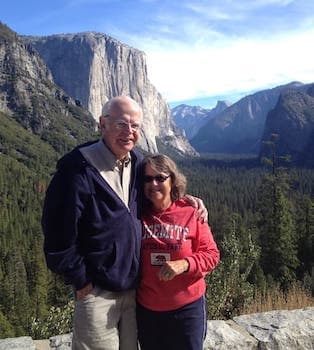
Ted Mooney, P.E. RET
Striving to live Aloha
finishing.com - Pine Beach, New Jersey
Q. Hi Ted.Thank you for your reply,
I had not seen your comment before progressing forward but I have decided to try and electroplate copper on sputtered copper rather than copper on gold. We are seeing some good results; in the future we may sputter copper on gold and electroplate from there, as the electroplating onto gold is what has given us weird results.
With that being said do you have any comments about a bipolar pulse for electroplating? We have found success with unipolar but bipolar in literature seems to indicate a potential for better results, better seemingly meaning smaller grain size of the deposited metal and better uniformity. Bipolar as far as my understanding seems to be forward and reverse electroplating in one pulse, typically the forward pulse being 75% of the pulse time. The portion of time where the pulse is reversed indicates to me that electropolishing would occur, but I am having a tough time understanding How the chemistry would occur as electropolishing usually has different cell chemistries as opposed to forward plating.
Employee - Ann Arbor, Michigan
March 30, 2022
A. Hi again. In the days before pulse plating was available it was not uncommon to use 'periodic reverse' in copper plating. Lowenheim's "Electroplating" and "Modern Electroplating" mention it, as does "The Canning Handbook" and other classics. It doesn't electropolish the substrate, but is thought to smooth the asperities in the plating by selectively dissolving the prominences which would be the points of highest current density.
I am no expert in pulse plating, but in addition to doing the same things as periodic reverse current, it is also believed to provide very good agitation in the boundary layer, probably thinning it, and thereby allow successful higher current density plating.
Our knowledge of precisely what is happening in the boundary layer seems largely empirical which in turn means that if some particular pulse form is found to be superior to some other pulse form, we probably have to also accept that as empirical knowledge rather than being able to explain it :-)
Luck & Regards,
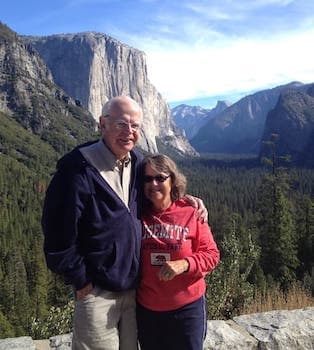
Ted Mooney, P.E. RET
Striving to live Aloha
finishing.com - Pine Beach, New Jersey
A. I am not sure if titanium coating has any critical role in your scheme. If not, you may directly deposit copper on glass either by sputtering or by cathodic arc - two popular variants of PVD process.
With cathodic arc process I have deposited copper up to 50 microns on different substrates. It should not be difficult to deposit still thicker coatings. It should also be simple to electro-deposit Cu on PVD coated Cu, but I do not have any expertise on this.
Bangalore Plasmatek - Bangalore Karnataka India
September 8, 2022
Q, A, or Comment on THIS thread -or- Start a NEW Thread