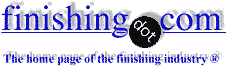
-----
Hard Anodize Tank Design
Q. What is the current state of the art for hardcoat tank design?
What materials are being used for tanks, cathodes, evaporators, refrigerants, and cooling fluids or brines?
Will these materials still be available and viable in twenty years?
Luke Engineering & Mfg. Co. Inc.

Wadsworth, Ohio
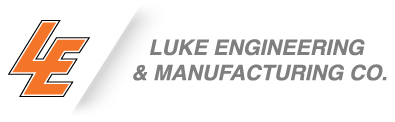
March 10, 2022
March 25, 2022
Chris-
Traditionally, Type III tanks have often been made from polypropylene copolymer, but there have been numerous problems with polypropylene that have emerged over the past few decades (flammability, loss of strength and other properties of time, oxidative chemical permeation etc.) so my employer almost never recommends them as a first choice. A much better tank would be made from 316L stainless (or a carbon steel tank for lower cost) that is bonded with an HP Koroseal lining. In this case, the tank strength comes from the steel and the chemical resistance comes from the lining. There are also higher end options available.
Cathodes should be 6062 T6 Aluminum. Drew Nosti may comment about this.
As far as chilling, indirect glycol chilling is going to be the best. Regulators may continue to regulate older refrigerants out of existence, but there will always be some choice for chilling the glycol. Likewise, the glycol itself could see increased regulation but then some other alternative fluid would rise up to take its place. For the heat exchanger, an external 316L plate and frame exchanger is the best for larger tanks. The plates last relatively long on hard anodize applications at low temperatures, but they do need to be replaced after some years. Other exchanger types are also possible, but plate and frame are generally the most cost effective overall.
I hope this helps.
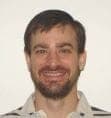
Jon Barrows, MSF, EHSSC
Kansas City
Q, A, or Comment on THIS thread -or- Start a NEW Thread