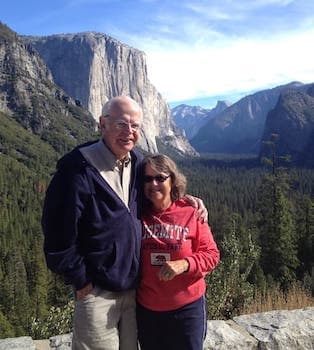
Curated with aloha by
Ted Mooney, P.E. RET
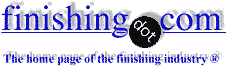
The authoritative public forum
for Metal Finishing 1989-2025
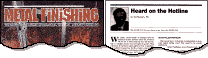
-----
Problems in thick nickel electroforming onto PVC
January 10, 2022
Q. Hello, I am an electrical engineer and hobby chemist. I have been following your fine site for many years, and could, to this date, solve all my problems through reading previous articles. But with my current project, I'm kind of stuck, and am not sure whether what I'm trying to do can, in practice, work at all. I hope you can give me some kind of advice despite my hobbyist approach.
I am trying to perform nickel electroplating on PVC. In fact, I'm trying to replicate the process of preparing metal stampers for vinyl records, so I need a nickel layer that is at least in the 0.1 mm thickness range. (This is purely for private, educational purposes, so I'm not expecting to obtain a perfect or commercially usable result.)
What I've been trying so far was the following:
- de-greasing with KOH solution / rinse
- applying a wetting agent (I used saponine) / rinse
- immersing the PVC in SnCl2 solution
- two-part silvering with double airbrush following the recipe mentioned by Trevor Crichton (here).
- nickel plating with Watts electrolyte (I'm using 240g NiSO4 / 40g NiCl2 / 30g H3BO3 at 42 °C / 107 °F, my pH is 4.2)
My first attempts were completely unsuccessful, and the nickel layer started to flake off almost immediately.
After immersing the PVC in highly concentrated SnCl2 solution (about 5 g/100 ml) for 10 minutes, and spraying the silver directly onto that (without rinsing), then plating at extremely low current (~0,1A/dm2) the layer was much more stable, but started to peel again when it reached about 0.01 mm thickness.
I understand that in commercial vinyl record production, the original material is not PVC, but a nitrocellulose lacquer, and the nickel coating is done using nickel sulfamate.
My questions are:
- It it at all possible to obtain such a thick layer on PVC using classic Watts electrolyte, or are the internal stresses simply too high? If it is, what can I do to further reduce the stresses? As I understand, the main factors are temperature, chloride concentration and pH. Does the current have a substantial effect on internal stresses? That is, is it unadvisable to use very low current for anything other than time efficiency and optical imperfections (both of which are not important factors for me)?
- Is there anything I can do to make the silver stick to the PVC any better? (Preferably not using palladium chloride, since that is very hard and expensive to get for me.) Unfortunately, I couldn't find much information on correct activation of PVC, which is why I'm still working on a rather unsatisfying trial-and-error basis.
Any help is greatly appreciated!
Arthur
- Berlin, Germany
A. Hi Arthur. I suspect that you know more about this subject than me, but I think your problem centers on trying to do this with a Watts bath, which I believe will remain highly stressed no matter what you do, rather than nickel sulfamate where the stress can be controlled from tensile, through zero, to compressive through adjustment of the plating current.
While PVC is a poor substrate when you want adhesion, it doesn't sound like adhesion is the main issue here, but stress causing the nickel plated silver layer to pull away.
Luck & Regards,
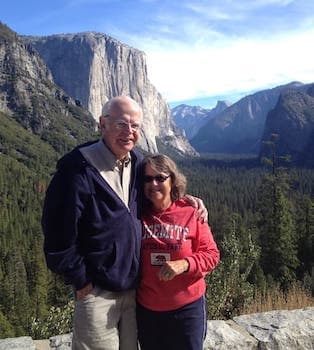
Ted Mooney, P.E. RET
Striving to live Aloha
finishing.com - Pine Beach, New Jersey
January 2022
January 13, 2022
Thank you very much, Ted. Your answer was very helpful, even though it did confirm my fears of having to change my course altogether.
I'll have to move to nickel sulfamate then.
Q. Even though I'm sure adding stress reducers to the Watts bath will not be enough to solve my problem, I'd like to learn more about them. According to Trevor Crichton's detailed post in thread 15268,; saccharin is out of question in my case, since the nickel layer will not withstand temperatures much higher than 170 °C, which is well below the 300+ °C melting point of most plastics I'm planning to use on the nickel surface.
Are there any other stress reducers that do not have as strong negative effects on thermal resistance?
Also in this same post, cobalt is mentioned. In what chemical form/quantity is that usually added to Watts electrolyte as a hardener, and does it also have considerable effect on internal stress?
Many thanks
Arthur
- Berlin, Germany
Q, A, or Comment on THIS thread -or- Start a NEW Thread