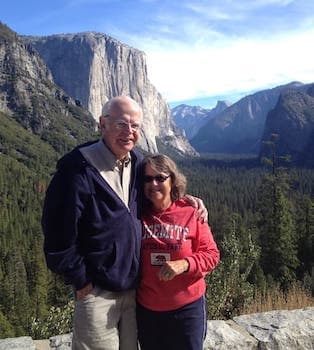
Curated with aloha by
Ted Mooney, P.E. RET
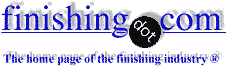
The authoritative public forum
for Metal Finishing 1989-2025
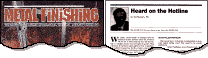
-----
Application where both wear-resistance and corrosion-resistance of coating are important
December 10, 2021
Q. Hi all, I've learned a ton here in the last few months so thank you!
I work in aerospace, but none of what I'm about to share is in production of a part, or in tooling (it's an intermediate step).
We guide carbon fiber thread through nickel plated guides. These guides are pretty thin (.4mm diameter wire, solder coated, then electroplated nickel 8 microns). This thickness is not working for us, the base wire (c30-c50 steel) corrodes (it is also exposed to intermittent watering as part of the process.
The questions I have are:
1. For a wire so thin, is there a practical limit to how thick the plating can be? I want to try to increase the thickness and see if that extends life.
2. If the nickel isn't sufficient (signs of being abraded) would zinc and a passivate EVER be hard enough?
3. Is it possible to coat a zinc layer with a hardened Electroless nickel to get the best of both worlds? That way if the nickel layer is cracked or penetrated, there would be some sacrificial layer?
4. Is there a practical limit to the thinness of duplex nickel?
- Dover, New Hampshire
A. Hi Mike. Could your "base wire" be stainless or some sort of brass or do you think the required hardness of the substrate demands steel? I think most thread guides and wire guides are ceramic rather than plated steel.
I can see from your question that you understand the fact that nickel is cathodic to your substrate and zinc is anodic, but for the benefit of future readers I don't want to gloss over that issue. There is no practical limit to the thinness of anodic or non-conductive coatings like zinc, but if coatings like nickel are too thin they do the opposite of what we wish: if thin enough to be porous or full of pinholes, they force the substrate to corrode to galvanically protect them because they are cathodic to the substrate. The theory behind duplex nickel is that the top layer of bright nickel is anodic to the inner layer of semi-bright nickel which promotes the corrosion spreading laterally in the bright layer rather than penetrating through the inner layer and into the substrate. So duplex nickel is always a good idea regardless of thickness, but if both layers are porous or pinholed such that steel is exposed, it's not really going to do any good.
Nickel-cobalt plating is significantly harder than plain nickel, and Berl Stein of NiCoForm [a finishing.com supporting advertiser] is an expert who would probably entertain a phone call from you about it. Hardened electroless nickel is certainly a possibility. And since these guides are part of a whole machine rather than free-standing items, an electronic galvanic protection system or zinc anodes might be rigged up.
As for thicker nickel you are nowhere near any limits; if you tripled your thickness you are still in the "routine" thickness range. I presume this is an ID where a PVD hardcoating cannot be applied?
Luck & Regards,
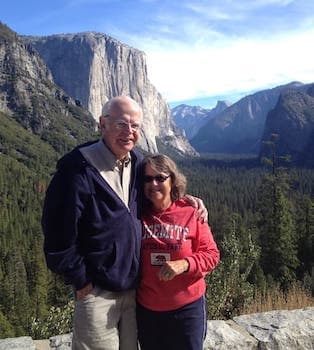
Ted Mooney, P.E. RET
Striving to live Aloha
finishing.com - Pine Beach, New Jersey
December 2021
December 13, 2021
Thank you for your reply and I'll see if I can give him a call.
We've tried to get stainless to work, and I'll see about brass.
Q. One more question if I may. Does increased nickel thickness create a higher risk of cracking? Those that came before me told me that's why we only use 8 microns of bright nickel. The guides are under reverse bending with a lot of cycles. If the corrosion wasn't an issue, the guides would last forever (steel fatigue cycle). Cracking of the finish is part of our problem.
Mike White- Dover, New Hampshire
A. Hi again. I suppose it's possible that thicker nickel plating might possibly tend to be more highly internally stressed or harder. But that's not really the answer to the situation.
The answer is the truism that almost anything is possible, but not everything is automatic & drop-dead easy :-)
The plater who you will be calling makes bellows from electroformed nickel; so: quite thick, very durable, extremely flexible nickel plating is possible. You won't need anything approaching that.
I don't know whether you are in the plating business, or carbon fiber thread business, or in the business of designing machines. But if these guides are something you want to buy rather than make, maybe the whole guide could be electroformed nickel or nickel cobalt.
Luck & Regards,
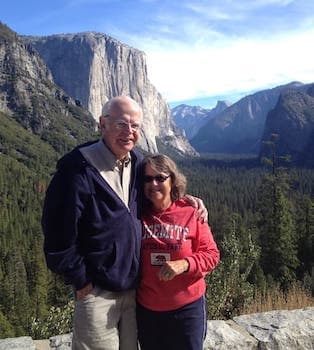
Ted Mooney, P.E. RET
Striving to live Aloha
finishing.com - Pine Beach, New Jersey
December 2021
Q, A, or Comment on THIS thread -or- Start a NEW Thread