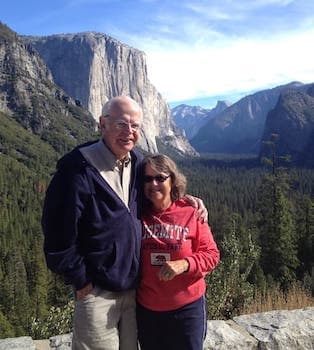
Curated with aloha by
Ted Mooney, P.E. RET
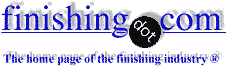
The authoritative public forum
for Metal Finishing 1989-2025
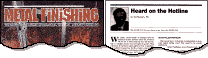
-----
Nitric acid drag-in to dye/seal tank
Q. The subject recently came up on Nitric. I have been a proponent of using a mild nitric dip after anodizing to improve rinsing . I owe that to Robert Probert. But is there a problem dragging the nitric rinse further down the line? Dye/Seal. I have always used a counterflow rinse after the nitric dip but some have noted that is not necessary. THOUGHTS?
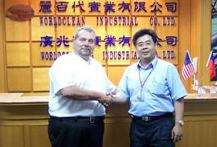
Drew Nosti, CEF
Anodize USA

Ladson, South Carolina
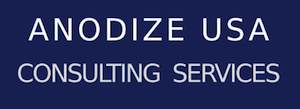
September 15, 2021
![]() |
A. I have not yet encountered a problem with too much nitric in the dye, however, with blind holes and recesses that is a real issue. A tiny bit of nitric in the dye is far less harmful then the same amount of sulfuric, which can pop out out of the pores in the warm dye, so if blind holes are involved, go up/down/in/out several times in the rinse to clear the nitric. ![]() Robert H Probert Robert H Probert Technical Services ![]() Garner, North Carolina ![]() September 20, 2021 September 21, 2021 Hi Drew supervisor - Cicero, Illinois Saporito Finishing Co. ![]() ![]() If I were you I would not use nitric acid dip after anodizing ... never ... there is a big risk of nitric acid solution dragging to sealing and electrocoloring bath by rack/jig. Especially it will inhibit coloring mechanism and you won't get proper black/brown tint. Also it will reduce sealing quality as well ... but biggest risk for electrocoloring bath. Alaattin TunaAnodizing Supervisor - TURKEY,Sakarya September 21, 2021 |
September 2021
Thanks Alaattin. I have no real familiarity with electrocoloring, and I suspect that the other participants are probably also more familiar with dyes than electrocoloring (although there are certainly some architectural anodizers in America, most anodizing is done by jobshops who employ dyes rather than electrocoloring). So I appreciate the warning that the effect of nitric acid on electrocoloring might be acute.
Luck & Regards,
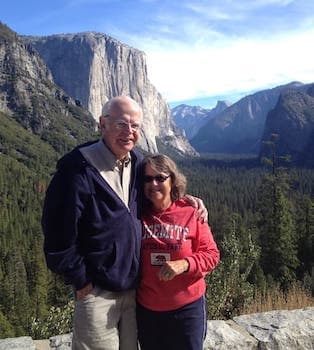
Ted Mooney, P.E. RET
Striving to live Aloha
finishing.com - Pine Beach, New Jersey
A. I'm a huge proponent of WEAK nitric dip. Like, 6% (4-8 range). Followed by aggressive cool to lukewarm DI wash gun for holes and contours, and quick city water rinse (maintained at <100 ppm tds), followed by another blast from the DI wash gun prior to entering the dye.
You need to maintain the pH in the dyes anyway, and they are less sensitive in general (referring to azo dyes) to nitric than they are to sulphate buildup.
You should absolutely not be dragging sulfuric or nitric all the way to the seal. That being said, the seal tank is a consumable just as much as your soap... in my shop, they get changed on the same cycle, and I think that if one looks at throughput, that parallel does make sense. I make up the seal to manufacturer max, and just let it drift over the course of x weeks as the pH drifts down towards manufacturers minimum, which is a good indicator of it being contaminated. This happens faster than the nickel acetate concentration decreases, though your mileage may vary. I don't try to adjust it back up, either in concentration or pH. I do not believe in artificially extending the life of a bath that is as susceptible to contamination as a seal is.
As an aside, this is also how I manage my sodium dichromate seal. When the pH starts to tank, that's the indication that you have excessive metals contamination buildup. Wanna check? Next time you lose half a pH point in a weekend, Take a couple litres out and bring it to pH 11 with naoh... you'll find sludge in the beaker the next morning. Further aside, the non-precipitation of the hex means that if you want to chemically clean a Na-Cr2 seal with sodium hydroxide to pH 6.75 and a strategically placed filter pump, yup it's possible. Just... turn off the heat a day or two before attempting this. It's spicy.
Lab Rat - Greenfield
September 28, 2021
Q, A, or Comment on THIS thread -or- Start a NEW Thread