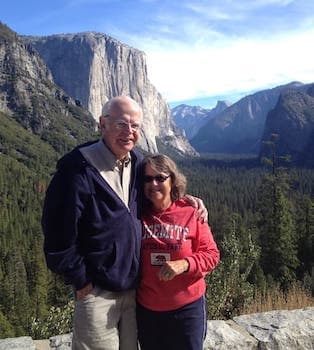
Curated with aloha by
Ted Mooney, P.E. RET
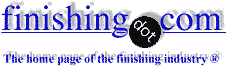
The authoritative public forum
for Metal Finishing 1989-2025
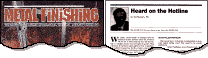
-----
White dots on an anodised finish

Q. Hello,
I've recently graduated as a chemist, and I'm working at an anodizing company in France. We are encountering the same issue with tiny dots on certain aluminum alloys (2017A, 2024, 7075), which are rich in copper and zinc. I believe these dots are caused by inclusions of Zn and Cu oxides that are not effectively treated by standard metal pretreatments (phosphoric acid, caustic soda, nitric acid).
I was wondering if the proposed reinforced post-oxidation treatment with nitric acid could work in my case. I would also like to hear opinions on possible additives that could help remove these oxides, such as oxalic acid or tartaric acid in the phosphoric acid bath, or BONDERITE C-AK 62203 in the caustic soda bath.
/p>
P.S.: There is also a difference between the face and the sides of the anodized object. The largest face is machined perpendicular to the "grain" of the alloy to minimize dimensional variations during mechanical surfacing. This difference in material composition is revealed by chromization in a Cr6+ bath, as seen in the golden-colored object in the attached photograph.
Then, when I anodize the part, I achieve very good results on the sides, but not on the main face of the aluminum piece.
Thanks for your responses!
Chemical Engineer - France, Isère, Le Versoud
February 6, 2025
A. Hi Jegou Klim,
The problem I am having here is that you seem to be asking if a rather undefined post-treatment with nitric acid, or additives in your pretreatment, will solve a problem with your current rather undefined pretreatment cycle.
Still, I don't think that's the problem. I think there are probably two problems:
First, yes, poorly extruded aluminum creates anodizing problems. We have many comments on that issue, and I suggest you search the site with the search term "anodizing extrusion problem" to locate those discussions and decide whether you side with those who say such extrusion problems can't be fixed in the anodizing shop, or those who propose things to try such as satin brushing.
Second, there are many possible causes of white spots, and you might start with Robert Probert's article "WHERE DO "WHITE SPOTS" ON ANODIZED ALUMINUM COME FROM?"
But if you are able to describe your pretreatment cycle, readers may be able to suggest improvements.
Luck & Regards,
Ted Mooney, P.E. RET
Striving to live Aloha
finishing.com - Pine Beach, New Jersey
Q. Hello Ted Mooney,
First of all, thank you for your quick response.
I indeed forgot to provide the line parameters and durations:
Phosphoric acid 7.5% vol -- 900 sec
Bondérite C-ak STL 10% vol relative (=5% vol NaOH) -- 30 sec at 40-60 °C
Nitric acid 25% vol -- 120 sec
Sulfuric acid 225 g/L at 18-21 °C, with 3 to 9 g/L dissolved aluminum (usually 8 g/L) -- 1800 sec, 12.5V, 150 A/m², rectifiers: 16V 500A and 16V 1000A in automatic CV mode
Nitric acid 5% vol -- 20 sec
Pigment adsorption coloring (Clariant brand, no electricity)
Sealing in water at 98 °C + Bonderite M-ED 11001 (acrylic acid + sodium phosphinate)
All steps are separated by two static rinses and one recycled DI rinse.
The racks supported by the automation system are made of aluminum. Titanium racks/pins are attached to these frames to hold the parts. All tanks are plastic, except for the sealing bath, which is stainless steel 304L. The entire system is supplied with city water, but this water contains no chlorine as it is treated by UV. Many other alloys pass through the process without issues.
From what I have read on Finishing.com, sacrificial anodes or laboratory rectifiers could be solutions, but my defects appear more uniformly distributed than those discussed in topic 15/94 regarding galvanic corrosion.
My issue strongly resembles the effects of aluminum sulfate accumulation. I haven't yet tried extending the time in the post-oxidation nitric acid bath -- do you think this could be an interesting approach?
As already said, there is a difference in surface structure between the large face, which is machined perpendicular to the fibers of the 2017A material, and the sides faces that are machined along the fibers. This difference is slightly visible (only at a certain angle under the light) when the surface is neither chromated (first step) nor anodized (second step).
Chemical Engineer - France, Isère, Le Versoud
A. Hello,
I wanted to share the root cause of the issue we identified regarding this question. The 2017A alloy is particularly sensitive to corrosion due to its copper content. The parts we were asked to anodize had been stored for a long time, leading to the formation of copper oxides within the alloy, especially around inclusions (both concentrated and dispersed). These oxides are more stable and cannot be easily removed with standard pre-treatments.
Additionally, it is possible that the matrix grain detaches during the process, creating the white spots observed. We have not tested oxalic acid or the electro-etching method, as we currently do not have the necessary equipment.
For now, we are waiting for the client to provide freshly manufactured parts to confirm or rule out this theory. However, we are successfully anodizing other 2017A parts without any issues. If no further messages are posted by me on this topic, it will confirm this theory, as I will not need any additional explanations regarding this alloy.
Chemical Engineer - Le Versoud
February 19, 2025
Thanks very much for the feedback!
Luck & Regards,
Ted Mooney, P.E. RET
Striving to live Aloha
finishing.com - Pine Beach, New Jersey
⇩ Related postings, oldest first ⇩
Q. I am working with an anodiser here in the UK. Lately, I have noticed parts are coming back with white dots. The anodisers are blaming the material and its finish. The part is heavily etched as it is not bead blasted.
I can't help but think it is not the material or finish to blame as in certain sections of the metalwork you have sections of exposed metal. It was not like this before. So I think it's likely to be down to the process itself.
Any advice would be greatly appreciated
- Devon Exeter
July 28, 2021
by Runge & Kaufman
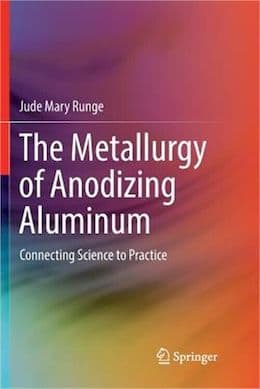
on AbeBooks
or eBay or
Amazon
(affil links)
A. Hi Joseph. We'll see what the practical anodizers and anodizing consultants have to say, but for my opinion ...
It sounds possible that the tiny white dots might have something to do with the material (see Robert Probert's article here: What Causes White Spots).
But your anodizer is certainly stretching my credulity in asking us to believe that those large white blotches where water, chemicals, or acid can collect -- or more likely where air collected, depending on which way is up -- were caused by a defect in the material :-)
Luck & Regards,
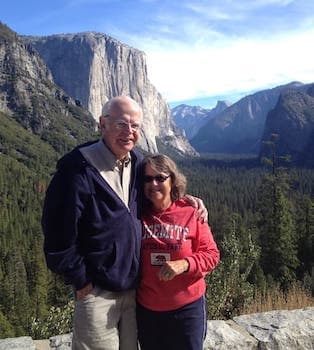
Ted Mooney, P.E. RET
Striving to live Aloha
finishing.com - Pine Beach, New Jersey
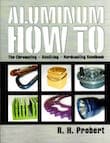
Aluminum How-To
"Chromating - Anodizing - Hardcoating"
by Robert Probert
Also available in Spanish
You'll love this book. Finishing.com has sold almost a thousand copies without a single return request :-)
A. I see two different kinds of white "spots" in your picture. (1) gas entrapments with no anodic film to adsorb dye. (2) tiny white aluminum sulphate which pops out of the (too large) pores when it hits the hot seal. Make the pores smaller by lower temp, lower free acid and/or higher current density, then use a 5% nitric acid post dip to flush the aluminum sulphate out of the pores ahead of dye.
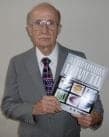
Robert H Probert
Robert H Probert Technical Services

Garner, North Carolina
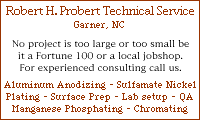
A. I have only one guess...Most likely it seems "gas entrapping" problem.According to pic I think it had been loaded as longitudinal(vertical). Thus, in that recessed areas had been filled by air. That means no anodizing layer and no coloring....
Alaattin TunaAnodizing Supervisor - TURKEY Sakarya
A. Joseph,
it most assuredly looks as though the larger white spots are resultant of air entrapment (a slight angle backwards with the honeycomb surface on the outside will most definitely aid in eliminating the air pockets). The smaller white spots look material related. It is very common for cast material to display these white spots which become even more evident after the dye process. Returning parts to the anodize tank for 5 to 10 minutes and then dying again will usually improve the cosmetics dramatically. You will generally see this condition greatly magnified on surfaces that have been machined.
I do have to admit, I greatly appreciated Robert's in-depth explanation of the science behind the spotting.
supervisor - Cicero, Illinois
Saporito Finishing Co.

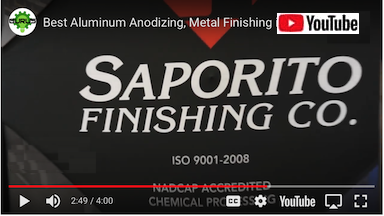
Treatment &
Finishing of
Aluminium and
Its Alloys"
by Wernick, Pinner
& Sheasby
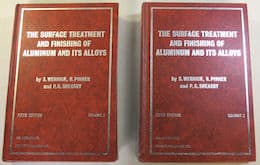
(note: this book is two volumes)
on eBay or
AbeBooks
or Amazon
(affil links)
Thank you very much to everyone for their advise. I should have been more precise. The large white dots I understand are down to processing issues.
Q. It is the small little ones I was unsure on.
We use a material called 5754 plan cast which is specifically formulated for anodising.
All of the advice you have all given me will be fed back. I will let you know how we get on.
- Devon Exeter
August 23, 2021
Q. Hello Joseph Stack,
i wondered if you solved the white dots problem you had? if yes, how did you manage to solve it? thank you!
Chemical Engineer - France, Isère, Le Versoud
February 11, 2025
Q, A, or Comment on THIS thread -or- Start a NEW Thread