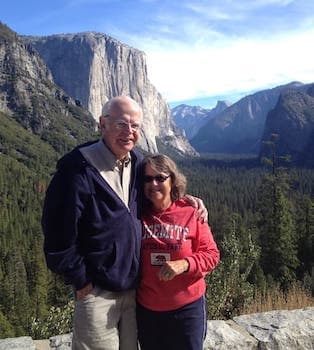
Curated with aloha by
Ted Mooney, P.E. RET
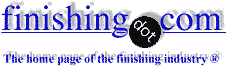
The authoritative public forum
for Metal Finishing 1989-2025
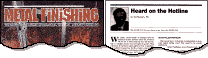
-----
Inexpensive In-Process Rust Protection/Plating
Q. We have a product that is comprised of (2) pieces of carbon sheet steel (HSLA Grade 50). They are welded together and we need to provide rust protection. After welding they are shipped out of the country for assembly. We had considered using pre-galvanized material, but are apprehensive about welding galvanized material (not only does it produce poisonous gas, but it would also introduce raw weld bead and a HAZ with compromised plating). The items being welded together have a tunnel which, if electroplated, would leave a section un-plated.
We are looking for a plating or dip coating that we could apply post welding and provide in process rust prevention (beyond a basic water based rust preventative that we apply post tumbling). We thought of a zinc phosphate, but have not had great luck with that to date. Any suggestions?
- Rochester New York
June 16, 2021
A. Hi Jake. You may realize this, but for the benefit of other readers, zinc is far less 'poisonous' than, for example, aspirin. Galvanized material does not produce 'poisonous gas', but welding it can release large amounts of zinc oxide fumes and -- although zinc is an essential nutrient and helpful in combating colds -- inhaling too much can certainly give you metal fume fever, and perhaps worse (like too much of almost anything). With good ventilation and proper welding hoods though, welding probably presents no significant risk to the welders.
The component can probably be hot dip galvanized after welding if you wish, but zinc or manganese phosphate followed by a corrosion inhibiting oil may be your best bet. Acres of sheet metal is zinc phosphated every day, so it may be more a matter of optimizing the process than writing it off.
Luck & Regards,
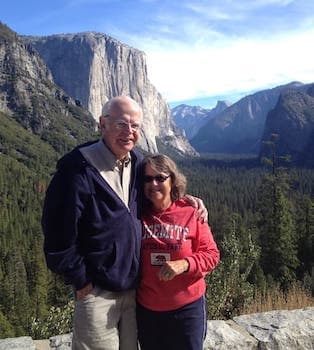
Ted Mooney, P.E. RET
Striving to live Aloha
finishing.com - Pine Beach, New Jersey
June 2021
Hi Ted,
I appreciate the input - I will definitely reach out to a few suppliers to see if any of them have a higher volume phosphate line than we do (we have a small batch line).
We'll also investigate just welding the galvanized material. That might be the easiest option in the long run since this is going on an automated welding line, we might be able to add a rust inhibitor station for a minor cost to the program.
Thanks,
Jake
- Rochester New York
June 17, 2021
Q, A, or Comment on THIS thread -or- Start a NEW Thread