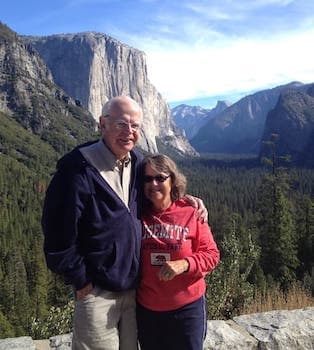
Curated with aloha by
Ted Mooney, P.E. RET
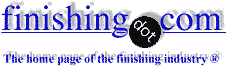
The authoritative public forum
for Metal Finishing 1989-2025
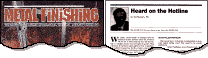
-----
Coating for very low resistance, high corrosion/weathering resistance, and hardness due to mechanical cycling
Q. I have an application where spring loaded pins engage with pad to make an electro-mechanical switch and complete the circuit. Looking for some suggestion on what coating can provide very low resistance 0.1-0.3 Ohms (maybe 0.5 Ohms max after 5-10 year use). Coating stable to ambient environment (application is door windows) so resist corrosion/oxidation.
Have used electroless Ni + P, and perhaps heat treatment (vendor in China).
In-coming parts have varying resistance, abrasion after cycle test, and resistance usually going high up to 2-4 Ohms after.
Should I just go with thicker EN+P + heat treatment? Or titanium nitride (TiN) may help? Any suggestions?
- Milpitas, California
February 23, 2021
A. Hi Ahmed. It's commonplace to want all the best across a range of properties (including low cost of course) but we can rarely get everything we want :-)
If cost is no object, rhodium or hard gold would be pretty good because precious metals can deliver reliably low contact resistance, and rhodium is very hard. Nickel would give lower contact resistance than electroless nickel, but isn't as hard. Chrome meets most of your needs, but not the electrical resistance. A low-boron electroless nickel would not offer as low resistance as electrolytic nickel but would be harder and more corrosion resistant.
It's sad that you couldn't find an electroless nickel plater in America, leaving you in this tough situation of trying to do a development project while suffering limited communication, and having to wait for samples sent back and forth while your test values are varying with no easy path to knowing why -- it's certainly doing things the hard way :-)
To my knowledge a non-metallic coating like TiN would not offer acceptable contact resistance.
Luck & Regards,
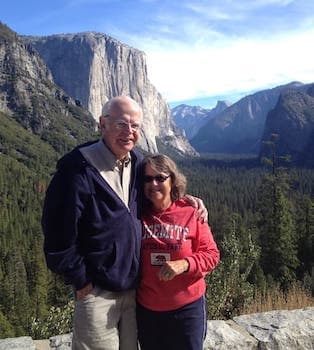
Ted Mooney, P.E. RET
Striving to live Aloha
finishing.com - Pine Beach, New Jersey
February 2021
Many thanks Ted.
As far as Rhodium, that will be last resort -- not sure if my CM can even do that. For now, I am going to work with supplier ensuring they do it better, more uniform, more consistently.
Best Regards, Ahmed
- Milpitas, California
February 26, 2021
A. Ted has some excellent suggestions with recommending hard gold and other coatings and I fully endorse his comments. There are a few other possibilities, including using the old automotive specifications for chromium plating -- namely plate with copper, followed by duplex nickel and then chromium. The old specifications were for hexavalent chromium, although this has now been superceded by trivalent chrome Another alternative is to deposit a thick layer of tin -- either hot dip or electroplate. Tin is pretty corrosion resistant, but it can migrate into the base material, so you may need to put an intermediate layer of nickel between the substrate and the tin.
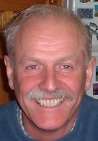
Trevor Crichton
R&D practical scientist
Chesham, Bucks, UK
March 18, 2021
April 9, 2021
A. You can look at a Tin-Nickel alloy for your contact material.
It has great corrosion resistance and excellent electrical contact resistance. Plus good hardness, 650+ HV. It has tin conductivity but with nickel hardness.
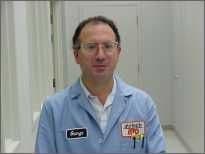
George Shahin
Atotech - Rock Hill, South Carolina

Q, A, or Comment on THIS thread -or- Start a NEW Thread