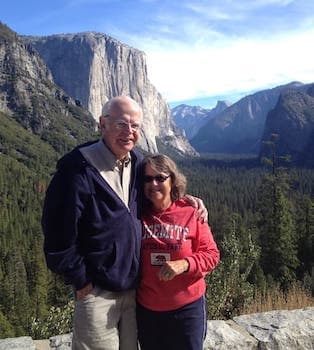
Curated with aloha by
Ted Mooney, P.E. RET
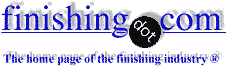
The authoritative public forum
for Metal Finishing 1989-2025
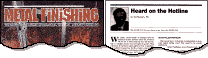
-----
How to get a bright / reflective surface after etching?
Q. Hi Folks,
I'm an artist working on manufacturing a piece I've developed that uses very fine lines etched into metal to reflect light in specific directions. Here's a video showing it in action:
The problem is my prototypes are created using a diamond bit on a CNC, which takes 10-30 hours for each piece, making it prohibitively expensive. I've had a photochemical machining shop try to replicate the process with chemical etching (using ferric tricloride), but the pieces produced this way are 5-10 times less reflective than the ones produced via diamond bit.
I think the problem is that the etched metal is matte rather than shiny. The ideal surface would resemble a mirror. I've tried both stainless steel and brass. The etch lines are 0.1 mm wide and II've tried both 0.04 mm and 0.08 mm deep etches. (I expect there are a range of scales this would work at, but I wouldn't want to make it much bigger).
My questions:
1. I'm very flexible in what metal I use. Is there some combination of metal and etching process that produces a shiny surface?
2. Is there any kind of post processing that can be done to make the surface shiny? Say electropolishing?
3. If not, can anyone suggest an alternative manufacturing process to create these etch lines? I'm looking into femtosecond laser ablation and dry etching but know nothing about these processes (other than that they look far more expensive than chemical etching.)
Much appreciated.
- San Francisco, California
January 11, 2021
A. Hi Raum. Surely the pieces could be made reflective by electropolishing or nickel plating. Bales Metal Surface Solutions [a finishing.com supporting advertiser] does precision machining and plating of this type and you may wish to speak to them.
But to your question of doing it a different way, it strikes me that the pieces could relatively easily be electroformed in nickel or nickel-cobalt rather than etched. This way they would be an exact duplicate of the master. CD & DVD as well as vinyl phonograph record molds are made this way, as are micromachines. The required precision is not even a challenge, and you would not have to compromise on the exact pattern you want. My good friend Berl Stein at NiCoForm [a finishing.com supporting advertiser] might be able to set this up for you.
Luck & Regards,
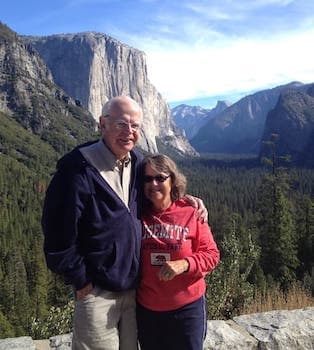
Ted Mooney, P.E. RET
Striving to live Aloha
finishing.com - Pine Beach, New Jersey
January 2021
Q. Thanks Ted. I'll try Electropolishing. Is there a specific type I should look for?
Out of curiosity, what's the typical texture of an electroformed part? On a scale of 'matte' to 'mirror-like' how would you describe it? How does the cost compare to photo chemical etching?
Appreciate the vendor recommendations as well...
- SAN FRANCISCO, California
January 12, 2021
A. Hi again. You're welcome! But your question, "What's the typical texture?"
says that I haven't made clear what I meant by electroforming. This is what would happen:
1. We'd electroplate a very heavy layer of nickel onto your diamond-cut master, but with deliberately low adhesion because ...
2. We'd pull off the electroplated layer, and for now at least we put aside your master; but now we have a perfect 'mirror image' of the master, with of course protrusions where the engravings were.
3. Now we electroplate a very heavy layer onto that mirror image and separate it again.
4. This new, now freestanding, electroplated layer is one of the the electroforms you'll be installing in the scintillator and is an exact duplicate of the original master.
5. We'd keep repeating step 3 & 4, generating as many exact duplicates of the original diamond-cut master as you want. (I'm simplifying just a tad because at some point the 'mirror image' item will start wearing out and you have to go back to step 2 and make more mirror images so you can continue step 3 and 4).
So the answer to the question of "matte to mirror-like?" is: whatever the finish on your diamond-cut master, that's the finish on the electroformed pieces. I can't give a cost comparison to photo-chemical etching, but can say that millions of components are made this way; and that the pieces would scintillate like the diamond-cut master because they'd be identical to it. If the idea sounds complicated, read up on the manufacturing process for records, CDs, and DVD's where these 'mirror images' and 'perfect copy' molds are electroformed all the time.
Luck & Regards,
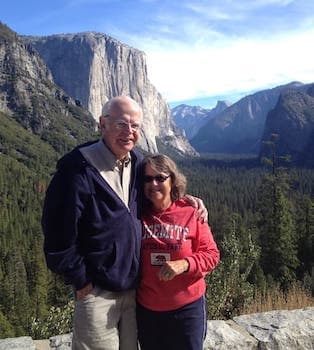
Ted Mooney, P.E. RET
Striving to live Aloha
finishing.com - Pine Beach, New Jersey
That's clear enough. :) I'll investigate this. Thanks again.
Now I'm wondering if there's a better way to produce the original so I can get the most mirror like finish for the copies... Maybe I'll experiment with electropolishing the CNC'd version.
- SAN FRANCISCO, California
January 13, 2021
Q. Hi Folks,
I'm developing jewelry and art pieces using a technique where thousands of tiny grooves are carved into a metal surface. Here's an example:
The grooves are roughly 0.12mm wide and 0.07mm deep.
A challenge that I'm running into is that these parts are quite difficult to clean because dirt and oil get trapped in the grooves. I imagine the best solution would be to coat it in a transparent layer that fills up the grooves creating a flat surface, but I'm not sure what would be best for this. I'm also concerned about the reflectivity of the coating subtracting from the visual effect that's being created by the grooves.
Would appreciate any suggestions,
Thanks
- San Francisco, California
February 29, 2024
A. Hi again. "A peek is worth a thousand finesses".
Surely it would be simpler to clearcoat 3 or 4 small sample pieces with 3 or 4 different clearcoats than to conjecture. I'd suggest trying a brass lacquer
⇦ this on
eBay
or
Amazon [affil links]
, a coating made for jewelry like Protectaclear from Everbrite [a finishing.com supporting advertiser], and a 2-part automotive clearcoat.
Luck & Regards,
Ted Mooney, P.E. RET
Striving to live Aloha
finishing.com - Pine Beach, New Jersey
Q, A, or Comment on THIS thread -or- Start a NEW Thread