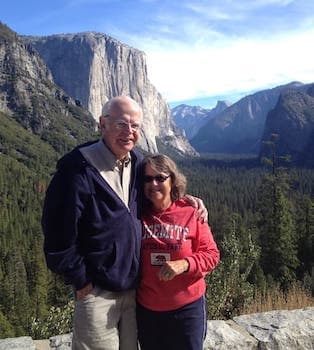
Curated with aloha by
Ted Mooney, P.E. RET
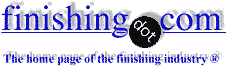
The authoritative public forum
for Metal Finishing 1989-2025
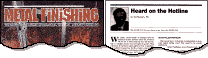
-----
Rack material for Iridite chromate conversion coating
Q. We have a large ordnance program requiring Yellow Chromate Conversion per MIL 7.3.1 of MIL STD 171 spec. on 6061 Aluminum. Color must meet Fed STD Color Spec ranges too.
Should we use titanium or aluminum racks?
If we go with titanium how do we mitigate possible galvanic corrosion between the parts, tooling, and chemistry?
- Palatine, Illinois
December 16, 2021
A. Hi Brian,
Aluminum works great. And because it's not a process that requires electrical conductivity between part and rack, you don't need to be particularly concerned with stripping between uses as you would for anodizing. The racks will strip to a certain extent in the caustic etch anyway, and further in the desmut; how much depends on how long since the rack was last used (yellow chromate continues to set even more stubbornly over time), and the immersion time in the etch, but it's refreshing not to have to keep stripping and thus degrading the racks between uses.
Not part of your question, but since you mentioned it... if you haven't tried to meet color specs before, do some testing on identically finished specimens of the identical alloy/temper... The color does not end up identical to how it looked as it came out of the bath. I find that Cl1A darkens noticeably as it cures.
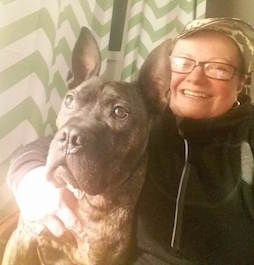
Rachel Mackintosh
lab rat - Greenfield, Vermont
January 31, 2022
⇩ Related postings, oldest first ⇩
Q. I need to build some custom plating racks for iridite baths.
What metal can I use to build them with that won't contaminate the bath?
- Ville saint-laurent, Quebec, Canada
September 14, 2020
A. Hi Fraser. 304 or 316 stainless would probably be fine.
But for the benefit of newbies trying to learn from the conversations, we should note that the Iridite process (a trade name for MIL-DTL-5541 [⇦ this spec on DLA] chromate conversion coating of aluminum) usually involves immersion is a sequence of alkaline cleaning, alkaline etching, and desmutting tanks before the Iridite. The desmut can be a number of different chemicals depending on the aluminum alloy you are processing. So while stainless is likely fine, there is a chance that aluminum or titanium would be a safer bet; aluminum would cost less, titanium more.
Another alternative would be to use plastic (PVC or polypropylene), or if high strength is essential, plastisol covered steel. I'm not clear on whether the parts would be delicately racked vs. dumped & jostled into baskets, sharp edges and all, which would be tough on plastisol coatings.
Luck & Regards,
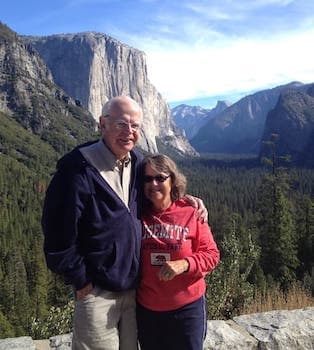
Ted Mooney, P.E. RET
Striving to live Aloha
finishing.com - Pine Beach, New Jersey
September 2020
September 14, 2020
Thanks Ted,
Your info was very useful.
The cleaning sequences you mentioned would be used and the rack would be dedicated to certain parts and not a basket.
Fraser
- Ville Saint-Laurent, Quebec, Canada
Junior Sales Representative - Resintech, Camden, NJ
Nadcap Chemical Processing Auditor - PRI, traveling
Process Engineer / Chemist - Denver Metal Finishing, Colorado
Q, A, or Comment on THIS thread -or- Start a NEW Thread