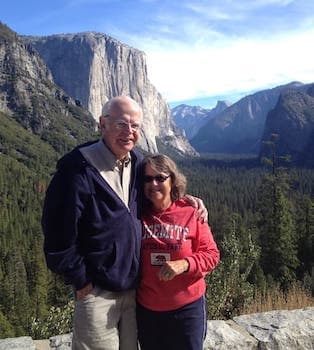
Curated with aloha by
Ted Mooney, P.E. RET
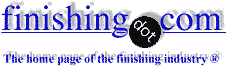
The authoritative public forum
for Metal Finishing 1989-2025
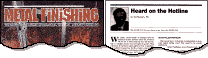
-----
Need 5RA finish on .180" elbowed hole in 316L
Q. We are currently machining a few thousand parts and are running into issues from honing that are causing large delays in our deliveries.
We have a 90° elbowed hole (long side is 1-1/8" deep and short side is 3/8" deep). We currently drill and ream the long hole to .176" and bore the short one to .180". Short one we can achieve the finish in-house off the machine, but long one has been no luck. Customer wants the finish consistent all around the side wall of the long hole including the bottom where it intersects the short one; they do not care so much about the Radius at the elbow.
We've tried roller burnishing, ballizing, lapping, etc... with not much luck. Main issue is we cannot achieve at least the appearance 5-10 finish at the bottom of the long hole due to deflection once it breaks through.
Is there anything we could be doing in house to achieve this? We are trying to bring the process in-house to meet our customer's demand.
Parts are Electropolished at the end.
- San Jose, California, United States
May 8, 2020
Hello Jerome
This product I assume is 316 SST or 304 SST Material.
This surface finish can be created on the CNC mill without honing.
The key is a combination of the end mill corner radius, feeds and speeds and coolant lubricity.
The part is rough drilled and then finished with a 0.180" 3 or 4 flute end mill with a 0.010"-0.025" corner radius. A 3 flute end mill is self centering.
The other critical component is the cutting fluid. If you are using oil it should come easy. If you are using water soluble coolant and its concentration is 7%-10%, increase the concentration. It may be necessary to try other coolant types and manufacturers.
Good Luck
Kurt
- Lexington Massachusetts
Q. WOULD A BALL EM WORK IN THE SAME FASHION? I'M HAVING HARD TIME LOCATING A 4.5MM 3 FLUTE END MILL LET ALONE WITH A TIP RADIUS. CURRENTLY USING FLOOD COOLANT AT ABOUT 10-12% (BLASER 6000). PRE-DRILL IS A .169" HSS JOBBER DRILL THEN FOLLOWED BY A .175" CARBIDE REAMER. I'M ASSUMING IT WOULD BE BETTER TO LEAVE A BIT MORE STOCK TO KEEP IT FROM BOUNCING AROUND THE WALLS?
ALL I HAVE IS A 4FLT BALL EM WHICH DID NOT WORK SO WELL BUT A LOCAL SUPPLIER DOES HAVE A 3FLT IN STOCK. RUNNING AT 80SFM WITH A .002" CHIP LOAD PER REVOLUTION (.0005" PER FLUTE). WE HAVE A PORT THROUGH OUR JAWS WHICH ACTUALLY SHOOTS COOLANT UP AND OUT OF THE HOLE SO NOT SURE IF THAT HELPS OR HURTS YET. MADE SURE THE RUNOUT WAS WITHIN .0001" AS WELL.
- SAN JOSE, California
May 13, 2020
Junior Sales Representative - Resintech, Camden, NJ
Nadcap Chemical Processing Auditor - PRI, traveling
Process Engineer / Chemist - Denver Metal Finishing, Colorado
Q, A, or Comment on THIS thread -or- Start a NEW Thread