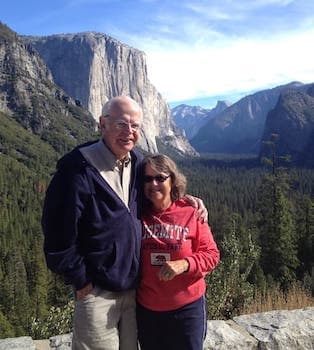
Curated with aloha by
Ted Mooney, P.E. RET
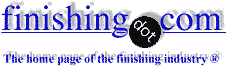
The authoritative public forum
for Metal Finishing 1989-2025
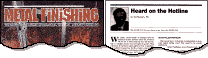
-----
PVA and Adhesive Electroplating Issues
(to provide context, hopefully helping readers more quickly understand the Q&A's)
Electroplating must deposit directly on metal, not on metal oxides for proper adhesion -- but stainless steel instantly oxidizes. The usual resolution is to start with a Wood's Nickel Strike which is dilute but highly acidic, so it simultaneously removes the oxide film and applies a thin coating of nickel.
Q. I want to deposit Nickel on SS sheet, the deposit should adhere to the sheet even under peel test. Can you suggest a pretreatment a (dip system) we do not want to use the Wood's Nickel system which destroys the photo resist coating.
Ravinder Singh- New Delhi, India
2007
2007
? What is your photoresist? Many resists are quite capable of taking the pH of Woods nickel.
A. Try polyvinyl alcohol that is crosslinked by exposure to UV light using sodium dichromate as the promoter. It is a well tried system that has been around for many years.
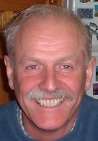
Trevor Crichton
R&D practical scientist
Chesham, Bucks, UK
A. PVA resists are hydrophillic and I would not expect them to stand up to aggressive plating solutions; not to mention the possibility of dichromate contamination of the nickel tank. This is one of the reasons they were obsolete in the 1970s.
Modern commercial negative resists are based on rubber (poly cis-isoprene ) or co-polymer (poly-vinyl cinnamate). Either should stand plating. The positive resists based on the Kalle patent are less resistant.
The critical stage of any resist process is the UV exposure and this must be controlled. The best way is by using an optical step wedge (ask your supplier). Alternatively determine the correct exposure by trial. Remember that photo exposures must double each time. 1, 2, 4, 8 minutes, seconds etc depending on your light source. Many operators try to speed up the process by reducing the exposure. The resist is not completely cross linked and is liable to be attacked by the plating bath. Note: if the bath has been attacking the resist, it will probably need a carbon treatment before you can expect good results.
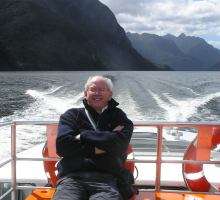
Geoff Smith
Hampshire, England
2007
Adhesive for paper converter reported to cause corrosion in chrome plated roller
Q. WE SUPPLY TO A PAPER CONVERTER A PVA-OH CLAY FILLED ADHESIVE WITH A 5.30 pH VALUE FOR SOLID FIBER LAMINATION, AND OUR CUSTOMER SAYS THAT THIS IS CAUSING DAMAGE OR CORROSION PROBLEMS. THIS DAMAGE LOOKS LIKE PEELING SPOTS AND SOME OTHERS LIKE SCALE.
COULD YOU SUGGEST US SOME METHOD TO MEASURE THIS?
Gerardo Vazqueztechnical support - Monterrey, NL Mexico
May 28, 2010
A. There could be many reasons but the ester groups of the PVA glue (polyvinyl acetate) react to alkaline substances producing polyvinyl alcohol and acetic acid ⇦ this on eBay or Amazon [affil links] . Perhaps the clay you are adding is promoting this reaction. On the other hand, it is well known that hard chrome is not very corrosion resistant, specially in acidic humid environments. If the problem proves to be corrosion, a nickel undercoat will help.
Guillermo MarrufoMonterrey, NL, Mexico
June 2, 2010
Making lace cotton fabric rigid enough for electroplating
March 14, 2019Q. Hi guys, I wandered away from doing the electroplating end of things for a while, but my mother has developed enough of an interest for me to start looking into doing some copper and nickel plating on her behalf.
Her idea, currently, is to plate small sections of lace into bracelets. I've got a solid grasp on plating onto metals, but here's my stumbling block, for this to work I think such a piece would need to be semi-rigid prior to plating, never mind the conductive coating. Currently I've looked at several glues and resins with an eye towards this goal, however I'm having trouble thinking through what would be a reasonable match for, at minimum, making the lace about as flexible as a glue stick; harder would be better, but I'll take what I can get. I have seen videos on youtube of folk using acrylic paint and graphite as conductive coatings, but I've also encountered folk recommending polyvinyl acetate (PVA) based graphite inks. Either way my worry is significant contamination of the plating bath.
So are there any thoughts for rigidizing the fabric for plating?
My small batch test with PVA glue have yielded failure.
I'm using an acid copper bath of the following formulation:
CuSO4·5H2O 200 g/l
H2SO4 70g/l
Brightener will be added to the actual plating bath.
The aim here is to electroplate lace and other fabrics for jewelry, so epoxy resins will not provide the resolution needed.
Blacksmith - Boone, North Carolina
A. Hi Marc. I know you said you failed by using PVA glue but I decades ago used Elmers brand very successfully many times. I mixed it with water 50/50 and soaked the fabric overnight in the mixture. Let dry thoroughly over a shaped mandrel and it will be very hard with no lose of detail. I've done this with sand dollars, too, with success.
Neil BellAlbuquerque, New Mexico
March 14, 2019
March 16, 2019
As stated previously PVA glue did not yield success in the last attempt, I'll follow your recommendation and see if I get better results.
In the interim I did see good results using clear polyurethane finish. Samples remained fairly rigid after 2 hours in the test plating bath.
Water based clear acrylic also yielded poor results, becoming flexible again in the first hour of immersion.
I'll be making some conductive coating for plating things next, either nano-particle copper (ascorbic acid + copper sulphate
⇦ this on
eBay or
Amazon [affil links] to precipitate very fine copper powder) or graphite.
Blacksmith/Machinist/Busybody. - Boone, North Carolina

Q, A, or Comment on THIS thread -or- Start a NEW Thread