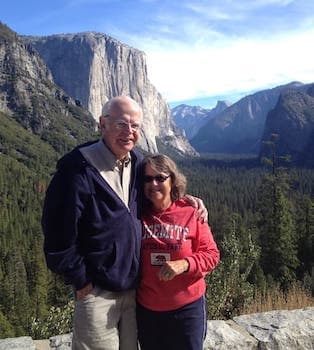
Curated with aloha by
Ted Mooney, P.E. RET
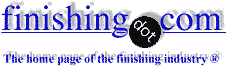
The authoritative public forum
for Metal Finishing 1989-2025
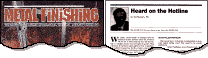
-----
Multiple small cells in one plating tank
Q. I am working on plating some relatively small items, little desktop award kind of things, and our final plate takes much longer than the preceding steps. What I was thinking about designing was a common tank with four cells inside it.
The process would looking something like: pretreat piece 1 start plating in cell 1 and start a timer, pretreat piece 2 plate in cell 2 and start a timer, and so on until the timer for cell 1 ends and it can be removed and piece 5 would then enter cell 1. My questions are: Is an idea like this even possible, or will it cause problems having a common bath? Will this cause inconsistent plating thicknesses? Will it damage the power supply to have cells essentially turning off while other cells are still running?
Ray WalkerChemical Engineer (new to plating) - Salt Lake City, Utah, USA
January 16, 2019
A. Hi Ray. The simplest approach, all anodes tied together and all cathodes tied together, usually works fine. There are a few exceptions:
- you can't anodize that way because anodizing requires gradual ramp up of voltage,
- alkaline tin plating might experience some anode filming problems,
- a few processes benefit from a 'hot lead' (electricity applied as the parts enter the tank)
- probably a few other special cases that aren't coming to mind immediately.
But in general, job shop platers work this way all the time, putting work into a tank that's already running, and taking it out with the rectifier on.
Regards,
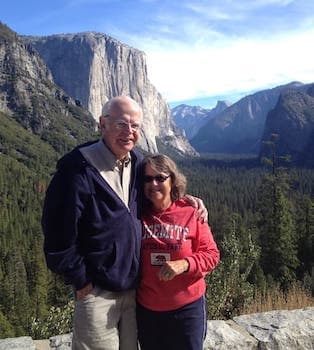
Ted Mooney, P.E. RET
Striving to live Aloha
finishing.com - Pine Beach, New Jersey
January 2019
Q. Thank you very much for the fast response Ted. A follow up question for you about power supply sizing... when trialing I've been getting great results with 4 amps as my target current, with all cells running I'm worried that if I have a power supply that provides "just enough" amps it may put unneeded stress on the supply. Would you recommend I up-size my power supply, or is "just enough" truly enough?
Ray Walker [returning]- Salt Lake City, Utah, USA
January 16, 2019
A. Hi Ray. DC plating power supplies take incoming 60 Hertz power and try to smooth it to DC; they tend to provide the 'cleanest' (ripple-free) and best power when operating near the top end of their capacity; on the other hand, power supplies generate heat and their electronics and other components are heat sensitive such that longer life can probably be expected if they're not constantly operating at max capacity.
I guess I'd venture a guess that power supplies operating fairly near their capacity but not constantly red-lined are best.
Regards,
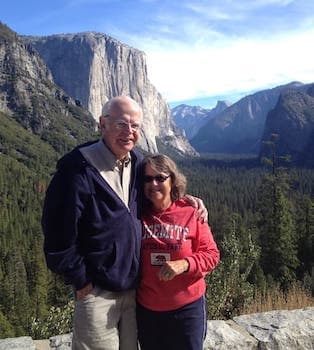
Ted Mooney, P.E. RET
Striving to live Aloha
finishing.com - Pine Beach, New Jersey
January 2019
Awesome, thank you so much for your help Ted!
- Salt Lake City, Utah, USA
January 16, 2019
A. Hi Ray
I ran gold plating baths for years with common anodes and a separate supply for each cell without problems.
You may find it better to have the cells in a line rather than grouped as four; less reach for the platers and less run off of plating solution on to the anode bars.
But there is much more to designing a plating cell; heating, filtration (with anti siphon), fume extract, etc. -- not to mention efficient rinsing, drag-out (counter flow, etc.)
Good luck but a little specialist advice could save you a lot of potential problems
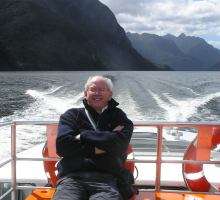
Geoff Smith
Hampshire, England
January 17, 2019
Thank you for your feedback Geoff, I hadn't thought about having the cells in line. I do plan on consulting a specialist before we do the final design, I've just been trying to get an idea of what is even possible so I know what to describe to the specialist. Answers tend to be a lot better when you know the right questions! :) On the "physical" aspect of the cell I am more confident, I've done process design, but my current role is my first leap into the fascinating world of electro-chemistry.
Thanks again for your insight!
- Salt Lake City, Utah, USA
January 17, 2019
Q, A, or Comment on THIS thread -or- Start a NEW Thread