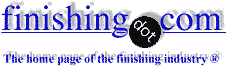
-----
U-shape vs in-line zinc electroplating
Q. My situation: We are currently operating a straight electroplating line with racking and un-racking at the same end. We are considering to re-configure our line in U-shape. Has anyone done this? What are the main advantages to go to U-shape line?
Frank RouthierCrd Placage - Drummondville, Qc, Can
June 4, 2018
A. Hi Frank. Please tell us whether this is an automatic vs. a manual line, whether it is rack vs. barrel plating, and whether your shop has one or two plating lines vs. a dozen.
But regardless, a U-shape line involves more equipment and is more expensive, but will offer higher production, more loading/unloading flexibility, and less potential for dragover contamination. The only time I think U-shaped lines are the wrong approach is if you have a whole bunch of plating lines which you could align in neat rows of straight lines, loaded and unloaded in a neat row but where U-shape lines vs. building shape would necessitate arranging lines with load-unload areas scattered in different orientations, which is a logistical problem.
Regards,
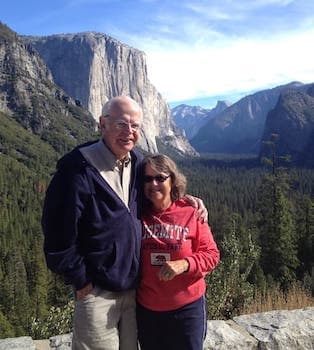
Ted Mooney, P.E. RET
Striving to live Aloha
finishing.com - Pine Beach, New Jersey
June 2018
Q. Thanks Ted,
It's a single manual rack line.
I would assume the increase in cost is mostly due to the hoist. Also, the transfer between cleaning side and electroplating/finishing.
Why the U-shape gives more production?
Thanks again.
Crd Placage - Drummondville, Qc, Can
A. Hi Frank. The higher production with one manual hoist is probably minimal, due just to the fact that the work only has to be carried forward and never backward, for a more efficient time-motion diagram. Try drawing a time-motion diagram for conveying the work through the line with the correct immersion time range in each tank and estimate the productivity if the hoist keeps moving.
But if you add a second hoist, or automate, the hoists not being in each other's way helps productivity too. With an automated line you would use at least one hoist on each side, and would use a transfer shuttles on the back end of the line as well as the front, rather than a U-shaped track.
Regards,
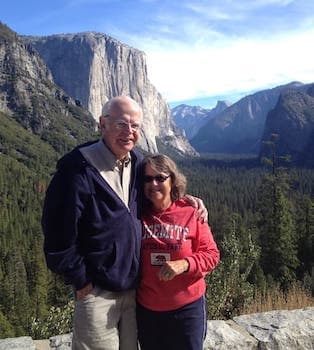
Ted Mooney, P.E. RET
Striving to live Aloha
finishing.com - Pine Beach, New Jersey
Q, A, or Comment on THIS thread -or- Start a NEW Thread