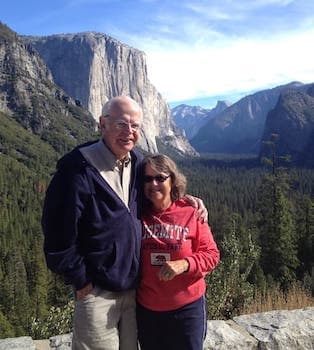
Curated with aloha by
Ted Mooney, P.E. RET
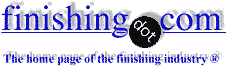
The authoritative public forum
for Metal Finishing 1989-2025
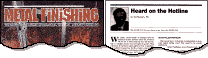
-----
Coating for threaded holes
February 20, 2018
Q. Hello Finishing Ninja,
I have a 12L14 steel automotive component that has a blind threaded (M6 x 1 6G) hole in it. The surface of the part is painted. We do not paint the hole/threads. We would like to protect the threads from flash corrosion until the fastener is installed at the OEM. Exposure could be up to 45 days. Part is shipped in containers with lids but not under a controlled climate. They are kept dry.
We have trialed:
* E-coating - processes available to our supplier are not conducive to even coating in the threads. Also forces a nonstandard tap to compensate for the film build. We do not want to use this coating.
* Black Oxide (hot process I believe as the part has a smooth finish and almost looks it is anodized alum) - the lack of film build is appealing. We have some part in our salt spray booth for preliminary testing.
We have ruled out:
* Zinc coatings - our pretreat baths (paintline) remove the zinc coatings, stripping the protection from the part and souring the baths.
What are your recommendations for a coating that will provide some limited flash corrosion protection, does not increase surface friction (for bolt run down) and can survive a caustic bath?
I am pinch hitting for the product engineer - Hamilton, Ohio USA
A. After painting, dip in a partially dry-to-touch black oxide oil.
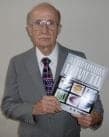
Robert H Probert
Robert H Probert Technical Services

Garner, North Carolina
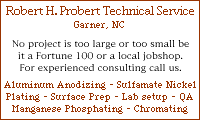
February 21, 2018
February 21, 2018
A. Probably an obvious suggestion but could you metal finish before painting? I would think Electroless Nickel would provide ample protection and the advantage of this process is that it forms evenly on uneven surfaces making it ideal for threaded parts. You would only need 1-2 µm all over to protect the part for the conditions described, this can also be painted on top of.
Assuming that's not an option, chemical blacking is certainly an option although as above you might want to add sealants/oil to further prevent against corrosion.
I would also consider a dry lubricant with Molybdenum Disulphide (MoS2) at its base. There are a number of different brands; without wishing to upsell anything I have used Everslik, Molykote and Moly mist in the past for various applications. Most of these can be applied by brush and offer low friction and high load capacity.
Hope that is helpful.
- Bradford, West Yorkshire, UK
February 21, 2018
ACRONYMS:
CapEx = Capital expenditure
PFMEA = Process Failure Mode and Effects Analysis
Q. Thank you Robert and Oliver. I appreciate your efforts to share some knowledge.
More details on my part:
The cap in question is part of a much larger assembly.
Any treatment to the cap would be before assembly and before painting.
Our paint pretreat bath is zinc phosphate.
Robert - I will need to research this oil. I am unfamiliar with it. I did want to stay away from CapEx and don't believe a manual application would satisfy my PFMEA.
Oliver - I considered electroless nickel. I wasn't sure about the paintability of the part though.
- Hamilton, Ohio USA
A. Here's an old platers' trick: When platers have articles that have been cleaned and are ready for plating but for some reason aren't going to be plated immediately, the platers sometimes dip them in a weak alkaline solution (often an alkaline cleaner rinse) and dry without rinsing. This also helps to protect the articles from the often acidic fumes in a plating shop, by leaving a weak alkali on the surface of the articles. Steel corrodes very, very slowly in an alkaline environment, and very rapidly in a neutral or acidic environment. Today a number of metal finishing suppliers offer similar compounded products (with amines, surfactants, nitrites, etc.) that perform this function even more effectively. I'd recommend that you contact a few of them and see what they have to offer. It would seem to be an efficient, cost-effective solution to your issue.
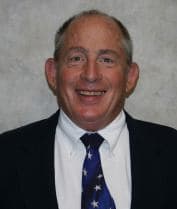
Tom Rochester
CTO - Jackson, Michigan, USA
Plating Systems & Technologies, Inc.

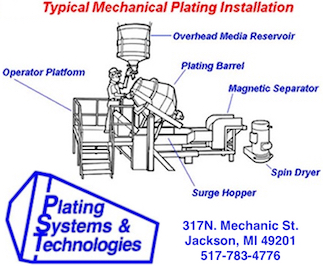
February 25, 2018
Q, A, or Comment on THIS thread -or- Start a NEW Thread