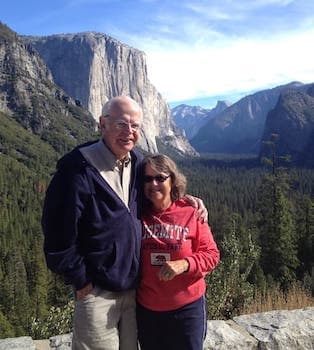
Curated with aloha by
Ted Mooney, P.E. RET
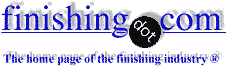
The authoritative public forum
for Metal Finishing 1989-2025
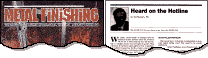
-----
Coating System for Corrosion Category 5 Structures
November 29, 2017
Q. Hello,
Can you suggest a best protection method for open area steel structures at 18-35 ppt salinity zones (Corrosion Category 5)
Mass and thickness loss at location as mentioned below for 25 years of life --
For steel 37500 g/m2 and 5.0 mm
For zinc 1500 g/m2 and 0.21 mm
If we use steel structures with painting, how many hours test needs to be done for salt spray test.
For making 210 micron zinc coating on the steel material is very tough for 2 mm or 3 mm base material thickness -- material may deform during dipping process.
Thanks,
Designer - Tirupathi, Andhra Pradesh & India
A. Hi Giriprasad. You are probably right that hot dip galvanizing presents a warpage risk for materials of 2 mm and 3 mm thickness. Hopefully an experienced galvanizer will weigh in on that issue.
I see that there are applicable codes for the coating of such structures, and it looks to me like you can comply with those codes via sandblasting and phosphatizing, in lieu of galvanizing, but I have not studied them sufficiently to assert that authoritatively. It seems, but I'm not sure, that you can alternately promise a 15 or 20 year life for the coating system instead of 25 years.
Salt spray testing is properly applied as a QA method, not as a predictor of real life, but you might double check whether the applicable codes require a particular salt spray endurance. Probably 1000 hours is not excessive.
Regards,
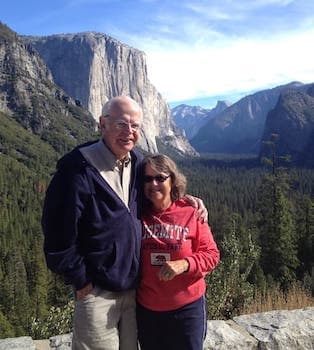
Ted Mooney, P.E. RET
Striving to live Aloha
finishing.com - Pine Beach, New Jersey
December 2017
December 14, 2017
A. Hello Mr Giriprasad,
For the salinity that you are describing, I would suggest a duplex coating of a sacrificial zinc or zinc alloy metal held in neutral state with another coat of Marine paint that uses the salinity of the area to further keep hardening the paint layer over the years of exposure.
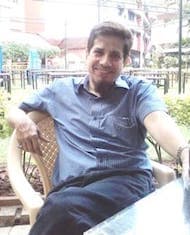
Khozem Vahaanwala
Saify Ind

Bengaluru, India
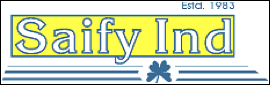
Q, A, or Comment on THIS thread -or- Start a NEW Thread