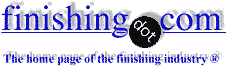
-----
Powder coating pre-treatment per needs, not competitor number/assumptions
April 17, 2017
Q. Hi, My Name is Anup, and searching the correct logical answer to my questions (also affirmation to answers I hold in me :) ). I want to know this as I believe too many thumb of rules are there but I love logic, as what's the fun in understanding without logic?
So bringing the courteous best in me, which engineers lack, at least my part of world :), I define my problem --
1) I have to coat electrical enclosure with moc as 1.6 mm CRC Sheet ms.
2) These enclosures will be mostly indoor application, with NEMA 4x benchmark just in case.
3) I have opted for powder coating in an automated spray booth.
4) The conveyor speed I computed is 0.5 m/min ,
5) I want adequate corrosion protection, not over or under (concern 1)
6) Adequate - translates to just the right number of processes. So more easier to maintain and control. Also lesser consumables and utility.
There is not a single weld as of now in our component to be powder coated.
Do I need 9 stage or I am happier with 5 stage, pre cleaning? (concern 2)
Also zinc phosphate conversion/nano /iron phosphate conversion (concern 3)
Please guide me for three of my concerns as highlighted.
1) What is base line -- I am planning in a bench mark which says (min 200 hrs salt spray test and max 300 hrs) so in case there is an overkill system, the upper limit will be higher but I don't need it. The lower limit is based out of NEMA rating.
2) The lesser the easier to clean and maintain nozzles, also how long a tunnel would I need for spray systems at the specified speed?
3) Zinc vs. nano vs. iron , which is best suited for my need?
Thanks in Advance.
Designer - Vadodara, Gujarat , India
A. Hi Anup. Whether most of your enclosures are for indoor use or not, that doesn't mean you can process them all for adequate indoor corrosion resistance and just let the ones installed outdoors fail -- you must design for real-world corrosion resistance. If you wish to not design based on competitor assumptions, then don't base your treatment system on salt spray hours, as that's not what corrosion resistance is really about, nor what salt spray testing is for ... and to try to NOT exceed 300 hours salt spray resistance is just plain silly :-)
Iron phosphate followed by powder coating will be adequate for indoor use and 200+ hours of salt spray resistance. It's hard to say whether it will be good enough for outdoors because conditions vary. If there is no substantial exposure to chemicals (acid rain, industrial atmospheres, lawn fertilizer, de-icing salt) it should be okay. Iron phosphate is cheaper and simpler than zinc phosphate, and 3 stages may be enough. Although we understand what nano technology means, all such pretreatments are proprietary, so it's difficult to say how complex/simple and expensive/cheap they are; but one thing is fairly sure: they are not going to sell them for less than they have to -- which means if they are simpler than iron phosphate, you can count on them being more expensive :-)
But I am a bit confused about your intentions as I understand that NEMA 4x enclosures are built of stainless steel, aluminum, or plastic -- not mild steel. A mild steel enclosure passing 200 hours of salt spray does not mean it meets the NEMA 4X "benchmark", and it certainly doesn't mean that it has equivalent corrosion resistance :-(
Regards,
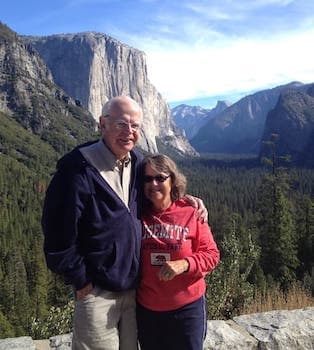
Ted Mooney, P.E. RET
Striving to live Aloha
finishing.com - Pine Beach, New Jersey
April 2017
April 18, 2017
Q. Thanks Mr Mooney, For being so Quick in your reply,
1) Ok I understood to actually environment test and not base on salt test, will study and revert back if any queries.
2) Although being Plain silly,
I had kept a number of 300 hrs as upper limit - so as to avoid Expensive and excess system as to my need, so this would have made this reasonable. When I say expensive, I can spend any amount when needed, but not waste a penny without application or give to someone who sticks me a standard sized systemwithout evaluating my need.
So I'd like to know, what upper limit bench mark should I set and what units?
3) The Nano coating offers the advantage of more coverage and more thickness over conventional coating, apart from also saving the energy cost of one heating oven, as said by some suppliers. Hence we are investigating Nano, and also it is relatively more environmental friendly, is what I am being told. Again cost of the above saving against cost of nano, needs to be adjusted once I understand,
4) Nema 4X is not Stainless Steel specific, anyways, let's hope I have read NEMA guidelines well.
5) Also, how do you know what size of spray cleaning booth is adequate.
as I need to compare two suppliers, with different size, engineering has to be similar with a margin of deviation based on preferences and FOS but these deviate 50%,
These question I feel will be helpful to all, and I shall document them well so all can understand and share.
Also Mr. Mooney deserves an appreciation for this wonderful Endeavor.
Regards
Anup
- Vadodara, Gujarat, India
Thanks for the kind thoughts, Anup.
2). Here's the thing. A properly designed and operated system of even simple design like a 3-stage iron phosphate pretreatment might, on a good day, deliver 300 hours of salt spray resistance with a competent powder coating. So what do you do then: operate it poorly and out of balance, so it won't exceed 300 hours? Rather, I think the answer is that you need a properly operated 3-stage iron phosphate system (unless you go with nano instead), and it must consistently deliver 200 hours salt spray resistance, but if it happens to deliver a lot more, good. Yet another factor is that there can be a large variation in salt spray performance from cabinet to cabinet, operator to operator, etc., so if you manage 400 hours it can just be extra insurance that you'll always get 200 hours.
Things may be a bit different in India than in the USA, but here we generally don't design a system based on theory and first principles. Rather, the phosphate process suppliers or powder coating material suppliers run test parts through their labs to identify a proper sequence and to get an early heads-up if something doesn't go as hoped because of poor rinse-ability, air pockets, Faraday cage effects, difficult to clean steel, etc.
5). The size of the phosphating cabinet is based on the treatment time, as implied in your first posting (length of cabinet divided by speed of conveyor = treatment time). But I don't know the treatment time for the proprietary nano chemistry and would prefer not to guess at a good treatment time for the iron phosphate.
As for 50% variation in cabinet size between vendors, it is difficult to say what size is truly "necessary". Although you understandably want to spend no more than necessary, the general fact remains that 'robustness' of the treatment cycle doesn't really fit a "go/no-go" model. The vendor who proposes a 50% larger cabinet is probably allowing more insurance against clogged nozzles, accidental temperature drop, occasional loads of dirtier steel, etc., causing a corrosion failure ... it's very hard to quantify the value of such robustness, let alone reduce the issue to necessary/unnecessary. A "perfect" design is unlikely on your hundredth process line, let alone the first :-)
Luck and Regards,
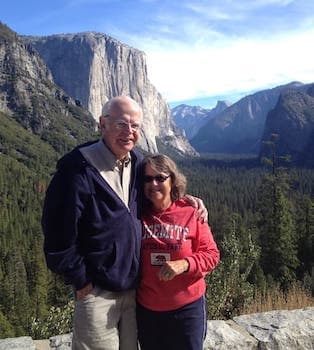
Ted Mooney, P.E. RET
Striving to live Aloha
finishing.com - Pine Beach, New Jersey
Q, A, or Comment on THIS thread -or- Start a NEW Thread