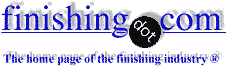
-----
Plating Aluminum Sand Casting Requiring Electrical Conductivity
April 4, 2017
Q. Greetings,
I am designing a part (~30in x 30in x 4in) that is aluminum (A356-T6) sand cast. The part is structural and electrical (needs to pass 400 Amps at 300 VDC). This part will be in an assembly that will be in building, but will see heat (-30 to 50 °C) and humidity. The part is not in a contact wearing situation, but I could imagine some micro-shifting due to thermal expansion/cycling. The part will have a service life of 30 years.
I have been researching the proper plating for this application (on this site and others) and this is what I have concluded so far:
- Tin and silver will diffuse into a cast aluminum part over time
- Nickel has better electrical conductivity than tin, better corrosion resistance than tin, and is good for wear applications
- Electroless nickel in general seems better than electroplating for this application since it is less magnetic
- Electrical conductivity is closely related to the phosphorous content in the nickel plating (less phosphorous, higher conductivity)
- To prevent tarnishing of nickel, use a chromate post dip (electrochemical is best)
- Nickel followed by silver would provide a long lasting conductive surface
So my conclusion is to plate the part with low-phosphorous electroless nickel, but I have the following questions:
1) From what I have said above, do you agree with this conclusion? Would you do anything different?
2) What thickness of nickel would you recommend?
3) Assuming the nickel plating stays intact for life of the part, would the conductivity decrease with time? Tarnishing issues?
4) Would you selectively plate silver over the nickel in the just the electrical contact areas for a better elec. conductive surface? Would you worry about the silver tarnish decreasing the conductivity over time (I am thinking 30 years here).
5) Would you use the chromate post dip?
Regards,
Steve
Product Designer - Somerville, Massachusetts, USA
Hi Steve. The first thing I would do is reconsider whether it's practical to machine this thing out of billet aluminum because trying to protect an aluminum sand casting from corrosion for 30 years with a conductive plating is a very tall order.
All materials (except precious metals) tarnish, but such oxide films will probably be no issue at your current and voltage. Electroless nickel plating is quite expensive compared to most electrolytic plating, but it's probably ideal, and is widely used for contacts. If this is not an appearance item, the chromate post treatment probably isn't necessary. Good luck.
Regards,
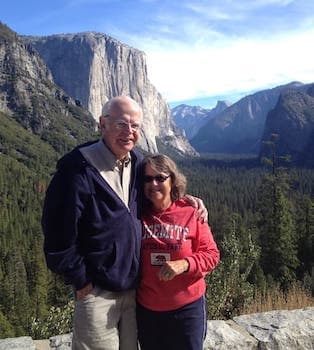
Ted Mooney, P.E. RET
Striving to live Aloha
finishing.com - Pine Beach, New Jersey
April 2017
Q, A, or Comment on THIS thread -or- Start a NEW Thread