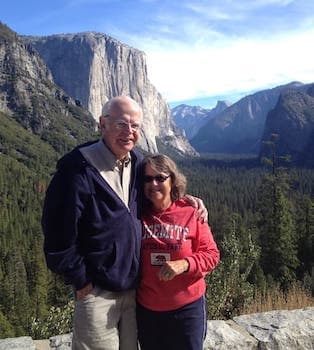
Curated with aloha by
Ted Mooney, P.E. RET
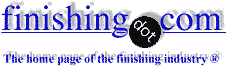
The authoritative public forum
for Metal Finishing 1989-2025
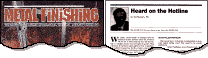
-----
Madsnell Etch
Q. Can anyone provide literature or sources for information regarding a Madsnell^Madsenell etch? Bath chemistry, operating temperatures, current densities, etc.? I would appreciate it a great deal.
Process Engineer - Urbana, Illinois, United States
January 26, 2017
A. Hi Alex. Let's make it a bit more interesting: Why do you ask?
I remember the name Madsnell^Madsenell Etch from back in the days when I was a young plating equipment engineer and, if I recall correctly, it was sometimes used on bumper plating lines, perhaps to activate medium strength steel ... my memory of it is dim. I believe it was a strong sulfuric acid bath, but again, I wasn't involved in the chemistry back in those days.
Strangely, I find no reference to it with google, google scholar, the Metal Finishing Information Service search of metal finishing literature, nor the indices of any of my go-to plating books. Help us out here, somebody, there IS a Madsnell^Madsenell Etch!
Regards,
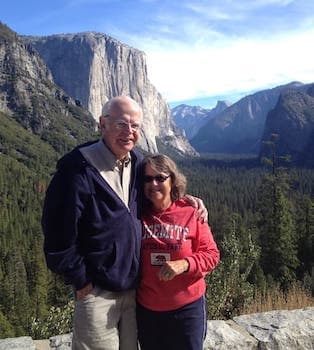
Ted Mooney, P.E. RET
Striving to live Aloha
finishing.com - Pine Beach, New Jersey
January 2017
----
Ed. note July 2017: We were misspelling Madsenell. With the correct spelling, info can be found.
Q. I also had difficulty finding any information in the usual suspects. Let's just say it's either this or another messy process. From what I was able to glean, I believe the bath is an anodic etch in high concentration (>70%) Sulfuric acid but I've also heard whisperings of Fluorides as well. The consensus seems to be that it's a really nasty process, hard on equipment and very fastidious. It should be noted that all of the above information is anecdotal as I have yet to encounter any scientific articles on the subject.
Alex Anderson [returning]- Urbana, Illinois, United States
January 27, 2017
A. Hi Alex,
Perhaps you would be interested in the etch process documented by PJ Holmes and JE Snell in 1966. The process involves an HF vapor etch at 20-30 °C with an Ar carrier gas. In order to achieve liquid phase etch rates, the vapor must condensate on the target. Don't try this at home kids!
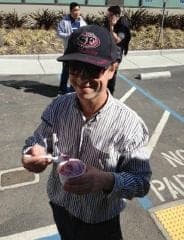
Blake Kneedler
Feather Hollow Eng. - Stockton, California
February 5, 2017
Q, A, or Comment on THIS thread -or- Start a NEW Thread