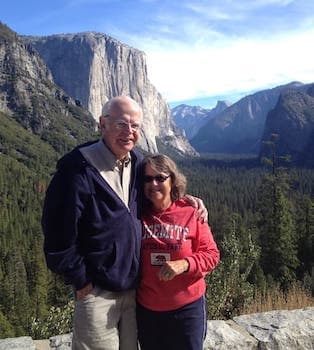
Curated with aloha by
Ted Mooney, P.E. RET
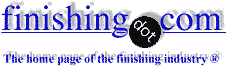
The authoritative public forum
for Metal Finishing 1989-2025
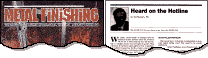
-----
Plating onto Aluminium without zincate or stannate
(to provide context, hopefully helping readers more quickly understand the Q&A's)
It is not possible to electroplate directly onto aluminum because aluminum instantly acquires an oxide skin. The most common method employed is to first put the aluminum parts into a zincate solution (a strong caustic solution with a high zinc content), whereby zinc will immersion deposit onto the aluminum by a displacement process ... then you can plate onto the zinc surface.
There can be variations or a little more to it, for example it is sometimes found to be more reliable to do a 'double zincate' (form the zinc coating in a zincate solution, strip the zinc in strong nitric acid, then re-do it); and there are proprietary processes, for example with nickel additions which are claimed to make the process more robust. And when tin plating will be done on the aluminum, a tin-based 'stannate' immersion plating may be used rather than the zincate process.
! I was reading some patents and found that along with zincate & stannate there is also a type of Plumbate (Potassium Plumbate) immersion coating. it coats aluminum with lead.
Marvin Sevilla- Managua Nicaragua
October 3, 2021
A. Hi all. I remember decades ago that a shop I worked with claimed to be doing electroless nickel directly on aluminum without zincate.
I would expect the adhesion to not be very good, and for the process to not be very robust, and I don't know whether or not they had to 'spark' it to initiate the process, but it doesn't sound impossible.
Luck & Regards,
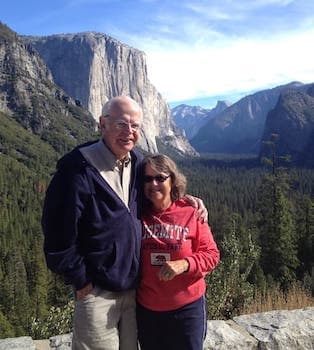
Ted Mooney, P.E. RET
Striving to live Aloha
finishing.com - Pine Beach, New Jersey
October 2021
⇩ Related postings, oldest first ⇩
sometimes on
AbeBooks or Amazon
(affil links)
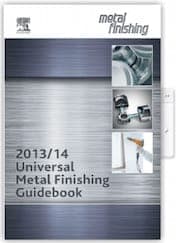
free pdf is currently available from academia.edu
Q. Hello.
I have a question about an article in the Metal Finishing Guidebook for 2013, page 243, on the internet. Is there anyone who has plated on aluminium per this description according to ASTM B253? I don't have the latest issue of B253. But what I read in the Metal Finishing Guidebook they said that you can plate on Aluminium without zincate or stannate, instead using ammonium before plating, and that should be as the part is put like an anode in the plating bath for a few minutes. Please any input from someone have be very interested.
Best Regards to you all and I wish all people a nice peaceful and good start at the New Year.
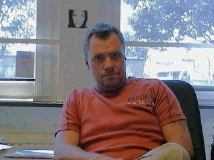
Anders Sundman
4th Generation Surface Engineering
Consultant - Arvika,
Sweden
January 9, 2017
A. Many, many years ago I did some work on this. I no longer remember the details, but essentially the process was alkaline cleaning and etching, desmutting in an acidic fluoride, reverse current for a few minutes in a low pH nickel sulphate solution, then direct current to deposit a continuous nickel layer for a few minutes, followed by conventional nickel plating.
We achieved good adhesion.
The theory was that the oxide coating formed in the reverse current step contained nickel ions which then converted to nickel metal in the cathodic step, leaving a thin but mechanically adherent nickel layer which could be overplated in a conventional nickel bath.
We didn't pursue it further because it offered no particular advantage over the conventional zincate process.
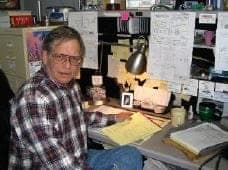
Jeffrey Holmes, CEF
Spartanburg, South Carolina
January 27, 2017
Q. Hi,
I found a little more information on the internet; there is a chemical called SafeGround plating Catalys seal 3400 #2.
Thanks Jeffrey, Did you know if the you used the part like an anode in the pretreatment?
Regards,
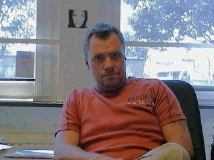
Anders Sundman
4th Generation Surface Engineering
Consultant - Arvika,
Sweden
January 28, 2017
A. Yes, Anders. The aluminum part was anodic first to form a thin oxide layer (like anodizing but much thinner) then cathode to deposit a layer of nickel which apparently interlocked with the aluminum oxide.
That was the theory anyway.
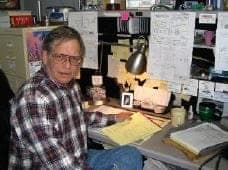
Jeffrey Holmes, CEF
Spartanburg, South Carolina
January 29, 2017
Q, A, or Comment on THIS thread -or- Start a NEW Thread