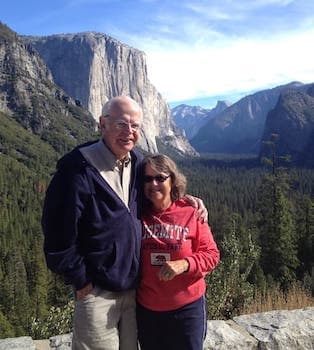
Curated with aloha by
Ted Mooney, P.E. RET
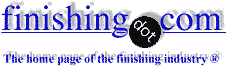
The authoritative public forum
for Metal Finishing 1989-2025
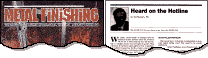
-----
How to electrodeposit Tungsten, Tantalum, and/or Iridium

Q. Hi, everyone!
Recently, I am trying to synthesize Ni-W coatings with a high W content using DC electrodeposition. Now, cracking is the main problem. I want to know whether there is any effective additives to inhibit cracking in Ni-W electroplating with a high W content? Also I want to know what the cracking mechanism for Ni-W electrodeposition is -- residual stress or hydrogen release?
Thanks!
- Wuhan China
March 30, 2022
⇩ Related postings, oldest first ⇩
Q. Dear Friends, is there any information available for plating Tungsten on steel or aluminium?
TJ Sharpe- Lewisville, Texas
1999
A. Hi TJ
Pure tungsten cannot be deposited from a conventional aqueous plating bath. Your options include co-depositing it from a cobalt or other plating metal, plating it from an organic or molten salt electrolyte, or using a vacuum deposition process. Good luck.
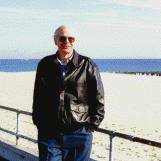
Ted Mooney, P.E.
Striving to live Aloha
finishing.com - Pine Beach, New Jersey
Q. I am hoping to find a viable way to plate Tungsten, Tantalum, and or Iridium to Aluminum. We are having difficulties with the aluminum oxide conundrum! Dave
David Millerscience consultant - Port Townsend, Washington USA
December 28, 2016
A. Hi David. The "aluminum oxide conundrum" is a relatively minor problem, requiring an immersion plating of zinc from a zincate bath as the first metal layer. The major problem is that tungsten and tantalum cannot be electrodeposited from conventional aqueous electroplating baths, and iridium deposition can only just barely be done, and only onto a gold plated substrate and with some other unusual requirements.
What are you trying to accomplish and what have you tried, and with what results? Are you open to organic plating baths, Fused cyanide salt baths, PVD coatings? Thanks.
Regards,
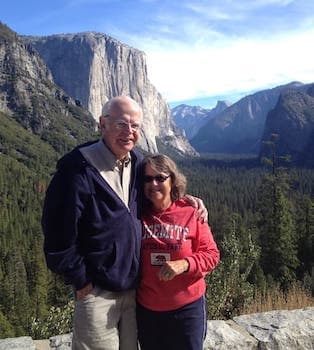
Ted Mooney, P.E. RET
Striving to live Aloha
finishing.com - Pine Beach, New Jersey
Q. We are attempting to plate these metals to the inside of a 12 inch aluminum cylinder. The inside diameter is just under four inches. We would like to do platinum and rhenium as well. I am unfamiliar with the organic baths you mentioned or the cyanide salt baths. I'd like to hear more about those! One method we are considering is peen plating. We are hoping to use a mix of these metal powders (1-5 micron size) and peen them into the aluminum at relatively high temperatures. We are thinking of using gallium as a way of removing the aluminum oxide. We need to have the metals fairly evenly distributed and with a final thickness of 6 microns. Thanks for your help with this! Dave
David Miller [returning]science consultant - Port Townsend, Washington USA
A. Hi again. The overwhelming majority of electroplating is done from water-based plating baths and many metals can be electroplated in this way. But some metals cannot be electroplated in that fashion for reasons such as water decomposing more readily than their ions reducing. So there are a few metals like aluminum which can be plated out of organic solutions but not water, and there are other metals which can only be electroplated from melted salts of the metal.
Decades ago there was a plating jobshop in New Jersey which specialized in plating from fused salts, but I don't currently know anyone with experience or expertise in that subject (safety and environmental regs probably make it difficult for a jobshop like that to exist in the USA today).
by Abner Brenner
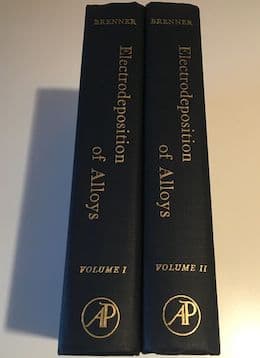
on AbeBooks
or eBay or
Amazon
(affil links)
A search of the metal finishing literature could be conducted by Finishing Publications / Metal Finishing Information Service [England] or perhaps others. Alternately "The Electrodeposition of Alloys" ⇨
talks a bit about such subjects, and offers references to papers about it.
As for peen plating, Tom Rochester [of Plating Systems & Technology, a finishing.com supporting advertiser] frequents these pages, and he may be the foremost expert on the subject.
I have nothing beyond 10 minutes of google knowledge about the gallium & aluminum combination, but it's my understanding that the gallium will form an amalgam and ruin the aluminum. So you might consider zincating as the first step instead. Good luck.
Regards,
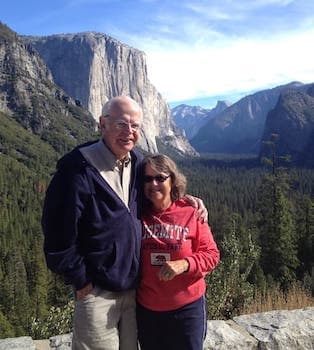
Ted Mooney, P.E. RET
Striving to live Aloha
finishing.com - Pine Beach, New Jersey
A. Hi,
I worked at an electroplating plant for 2 years, small batch work, fast turn around, no little stuff, we had a barrel system setup but rarely used.
Vast majority of our work was zinc plating, for which we had a big, 30 ft x 8 ft x 5 ft deep double sided tank, which could take 4 bars if needed. Our everyday plating mix was zinc - tungsten mix, at various combinations, but usually about 4 - 1 zinc/tungsten in baskets, but we could take that right through to opposite mix 4:1 tungsten/zinc.
About 2 tons of cyanide in tank, I could never get over how much cyanide would just vanish into tank, dozens of 20 kl containers when making fresh mix up.
One of the more interesting jobs I've had; but unfortunately the plant was victorian, non-updated and worn out, with an employer with victorian ideas of servitude.
Plant manager of 26 years decided I had learned/was learning so fast he could finally walk out knowing plant would still run OK.
Nobody told me he'd left, I got thrown in at deep end. Monday morning got into work, found all the electric off, about 3 nasty chemical floods about to happen, plating tanks cold, and boss accepting ultra rush jobs, i.e., done in front of customer at maximum haste ... and then boss decided to accept some parts from oval workshop, cast iron with steel inserts, wanted/needed steel plating, but not allowed to remove from cast iron casting, had to be plated in situ ...
Try explaining that it's impossible, without affecting the cast iron too, which won't plate but will get weakened, got first attempt wrong, stripped, second attempt, local area power cut half way through, third attempt and cast iron is looking a bit grey, but steel buts plated up OK; so pacified it quick, and cast looked normal again.
Bloke turned up for box of bits, turned out it was the brakes for an ultra rare Ferrari Le Man's special from 1958 being rebuilt, worth millions -- £7.4 m I think it sold for a few years later, brakes absolutely unique, if I'd cooked the cast trying to plate, they would have had to be totally recast, using fresh metal, devaluing car slightly. Things got so bad in factory that nobody would insure it, so I went back to nice clean, peaceful gardening instead.
But yes, tungsten plates OK when mixed with zinc.
- London
March 30, 2024
Fascinating info, Ted, even Brenner's 1400-page "Electrodeposition of Alloys" ⇦[this on
Amazon,
eBay, &
AbeBooks affil links]
doesn't mention that possibility. And the story of the Ferrari brakes is amazing. Thanks!
Regards,
Ted Mooney, P.E. RET
Striving to live Aloha
finishing.com - Pine Beach, New Jersey
• Topic 27089 "Electrodeposition of Tungsten or other Very Hard Material"
Q, A, or Comment on THIS thread -or- Start a NEW Thread