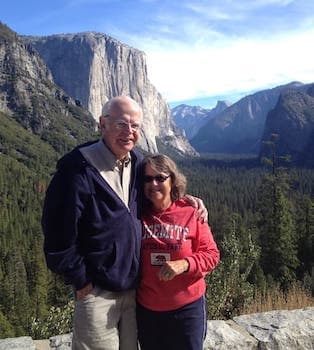
Curated with aloha by
Ted Mooney, P.E. RET
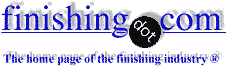
The authoritative public forum
for Metal Finishing 1989-2025
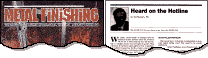
-----
Polished Aluminum vs Undercoated Aluminum
November 4, 2016
Q. Hi all,
I would like to know if there is any best practices regarding plating and/or painting of aluminum parts exposed to free weathering? Is there any standard or handbook that might cover that or any information that would help?
I have been working on the galvanic compatibility of various metallic materials and encountered a particular doubt. I understand that aluminum and nobler materials such as copper and stainless steels are not really compatible; for that reason I would like to ask the following: Can someone explain:
1. What are the differences between undercoated and polished aluminum? Is undercoated the same as primed? If yes, undercoated and primed refer to conversion coatings on aluminum?
2. Secondly, if coupled with copper or stainless steel, which performs better polished aluminum or undercoated/primed aluminum? Any reasons?
Many thanks in advance,
Angel
Product Development Engineer - Materials - Swindon UK
Treatment &
Finishing of
Aluminium and
Its Alloys"
by Wernick, Pinner
& Sheasby
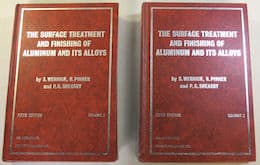
(note: this book is two volumes)
on eBay or
AbeBooks
or Amazon
(affil links)
A. Hi Angel. That's a very broad subject, and the most complete reference is probably Werner, Pinner, and Sheasby's "The Surface Finishing and Treatment of Aluminum & Its Alloys".
I don't know exactly what you mean by "undercoated", but let's try a quick tutorial ...
Aluminum is a very active metal -- meaning that it oxidizes almost instantly, and will be the anode (the component that corrodes) when joined with a more noble metal (most metals are more noble). Fortunately, the oxide / corrosion product of aluminum is more adherent and impervious than the oxide product of steel (rust), so there are some cases where just polishing the aluminum will yield enough corrosion protection for non-critical, non-aesthetic, mild exposures.
Aluminum (polished or not) is often anodized, which is an almost transparent electrochemical treatment to build an engineered oxide on the surface, which is far more stable than the naturally occurring oxidation. This is usually adequate even for outdoor exposure.
As alternatives, aluminum can receive an organic coating like paint or powder coating, but this is usually preceded by chromate conversion coating. Or it can receive just the chromate conversion coating. Or it can be electroplated with another metal. In short, almost any surface treatment is possible, and may be useful.
Aluminum should NOT be coupled with other metals if there is a practical way around it. Coupling with stainless is sometimes unavoidable, and often not fatal because of the anodized or natural oxide layers on both stainless and aluminum which tend to lessen galvanic currents. Coupling aluminum with copper would almost always be completely unsatisfactory: these pages are replete with stories of copper shards corroding aluminum structures, copper dust ruining automobile wheels, etc.
If you post an actual situation, experienced readers can probably advise you about what corrosion prevention measures will be most practical. But they probably will not be able to help you to become quickly able to make such decisions for yourself because, as mentioned, it's a reasonably deep subject and you'll need to invest a lot of time to become proficient at it. Good luck.
Regards,
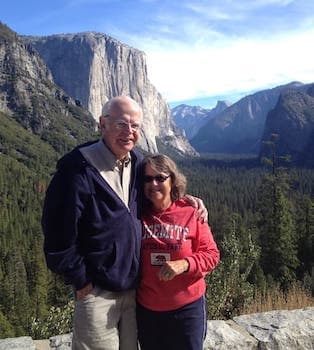
Ted Mooney, P.E. RET
Striving to live Aloha
finishing.com - Pine Beach, New Jersey
Q, A, or Comment on THIS thread -or- Start a NEW Thread