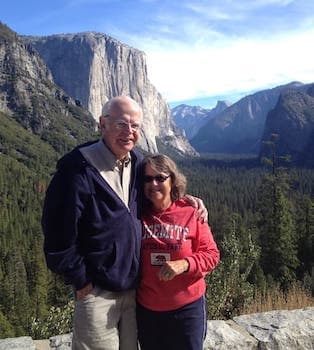
Curated with aloha by
Ted Mooney, P.E. RET
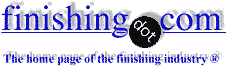
The authoritative public forum
for Metal Finishing 1989-2025
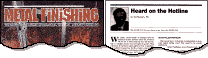
-----
Copper - Nickel interface adhesion problem
September 16, 2016
Q. Hi Ted,
At our facility we have a brass part that is first copper flashed in a cyanide copper solution, then a nickel flashed in a Sulphamate bath followed by plated to 3 to 5 tenths in cyanide cadmium plate and dichromate passivated.
The customer fits these parts to a sub-assembly were the tabs at the ends get bent up. Normally this is OK. But the most recent batch has peeled at the copper nickel interface.
Can any of the great contributors please help, as we have pressure on us, naturally, to fix this.
Thanks and best regards,
Company Chemist - Isle of Man Great Britain
![]() |
A. Check the free cyanide concentration in your CuCN strike. ![]() Dave Wichern Consultant - The Bronx, New York September 23, 2016 A. The copper surface was tarnished, or had a residual alkaline film. ![]() Jeffrey Holmes, CEF Spartanburg, South Carolina September 23, 2016 A. Hello Mark, adhesion problems often rear their ugly head when the underplate surface is not active enough. Before sulphamate Ni, the Cu surface should be activated in a sulfuric acid dip, or an acid dip that you commonly use. If the acid dip concentration is too low or the activator is not dumped per schedule, the activation becomes ineffective. Have a full analysis done on the Cu strike. Make sure all rinses are fresh and rinse times are adequate. Change the acid dip and keep the concentration at 10% (if you are using a sulfuric acid dip). I have seen cases where there is inadequate rinsing after CNCu strike and even minor drag-in will result in neutralization of the activator. If using city water rinses, check them for TDS (total dissolved solids). A full analysis of the Ni sulphamate bath should also be done including ph. Go in to the Ni bath with live current. I know this is extensive, but all possible causes should be addressed. Good luck and hope your down time is short. Mark BakerProcess Engineer - Phoenix Arizona September 23, 2016 |
A. It is difficult to tell from the photos if the copper strike or the nickel is peeling. If it is the copper layer that is peeling, then inadequate surface preparation , or insufficient free cyanide in the strike bath are the likely causes. It is also helpful to enter the strike bath live (with current).
Lyle KirmanConsultant - Cleveland Heights
September 25, 2016
September 27, 2016
Thanks guys for your input, there are some useful ideas there that you have mentioned; I will be focusing on the rinsing after copper flash and the activation of the surface as a first focus point. I'll keep you posted.
Best regards
Mark
Aerospace - Isle of Man, Great Britain
A. Good day Mark.
I would like to suggest that you add fluorides to your 10 % sulfuric acid dip, or ammonium persulphate for a micro etch. This acid dip will work for adhesion issues with brass as substrate material and subsequent copper plating etc..... Maybe check TOC value for the nickel solution.
Almost forgot to mention, check for water break after each and every water rinse during your process.
It's a habit for me!
Them's the breaks!
Good luck.
Regards,
Aerotek Mfg. Ltd. - Whitby, Ontario, Canada
Q, A, or Comment on THIS thread -or- Start a NEW Thread