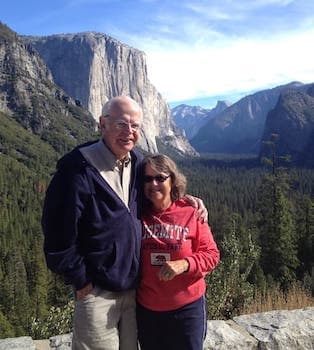
Curated with aloha by
Ted Mooney, P.E. RET
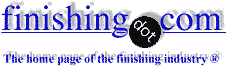
The authoritative public forum
for Metal Finishing 1989-2025
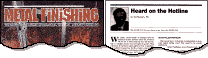
-----
Need High Rez Pictures of Aluminum Anodize Finishes
July 3, 2016

Q. Hey everyone, a few questions and a backstory. I can't seem to find any quality photos of various types of aluminum anodize finishes online that match my curiosity. I've visited several finishing shops local to my area, but it seems that nobody keeps a consistent portfolio on hand to help with this endeavor and asking for individual samples of multiple material finishes myself would be cost prohibitive.
I'm an avid DIYer and love the look of metal for electronic enclosures. A gentleman running a group purchase online is making Model F reproduction keyboards and saw one of my designs. He's looking for the right aesthetic for an aluminum keyboard case (5xxx or 6xxx) he's offering. Does anybody know the best place to source pictures so we can compare various finishes?
After asking the community, the consensus is lifetime-level high durability and scratch resistance. From my understanding, a properly executed Type III hardcoat is the way to go. I personally love the look of my bead blast + bright dip + Type II Anodize amplifier shown here. Is it possible to chemically polish / pretreat / bright dip prior to a Type III hardcoat to bring back luster and minimize the frostiness of matte anodizes, similar to that of Apple products? The colors we're looking for are "clear" (coloration from the Type III anodize is fine), gray, gray-green, and black.
Any pictures or resources to help us would be wonderful. Thanks in advance!
Hobbyist: Mechanical Keyboards, Amplifiers - Carlsbad, California, USA
![]() |
Your type 3 coatings (if dyed) generally will not be as bight or vivid as type 2. Prior to dyeing, type 3 coatings are darker, and thicker..which can lead to challenges in dyed work (except black). I've not done dyed work for many years, but dyed type 3 was always duller than type 2 in my experience. For bight work, thinner is always better as the luster disappears as the coating gets thicker. ![]() Marc Green anodizer - Boise, Idaho July 4, 2016 My experience has been anodizing (TypeII) parts made from 2xxx, 5xxx, 6xxx and 7xxx for various customers, and from this I can say that pictures will be of little use to you, and this is because it is quite difficult to make photos of different finishes, you need to make these pictures using identical settings on camera using the same lighting conditions, and even then the shape of the part may exaggerate or hide some specific detail of a particular finish. - Riga, Latvia July 4, 2016 |
Q, A, or Comment on THIS thread -or- Start a NEW Thread