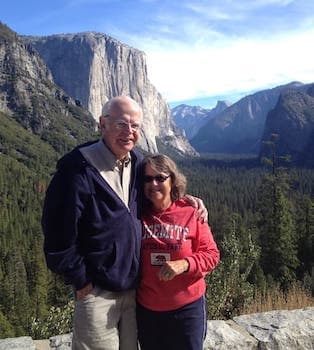
Curated with aloha by
Ted Mooney, P.E. RET
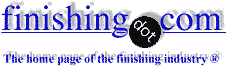
The authoritative public forum
for Metal Finishing 1989-2025
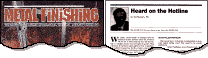
-----
PVD Coating (TiN) of Firearm Slides
April 19, 2016
Q. Good Day Everyone:
I am involved in TiN coating firearms components regularly. The problem is black pinhead popping around the edges and radii. Our typical process is:
1) Sand blast with 550 grit
2) Muriatic acid bath in 31% conc. for 30 minutes
3) Water wash
4) Ultrasound for 1 hour
5) Miele industrial dishwasher wash with MDX and Protex 16
6) Alcohol wipe down
7) PVD TiN coating with strong etch.
Is there something different we should be trying to eliminate the pinhead popping?
Thanks;
Mike
- Greenville, South Carolina
A. Hi Mike. Someone with specific TiN and/or firearm slide experience can probably answer better than me, but I've never heard of a prep process in that order. In plating, anodizing, galvanizing, phosphating, conversion coating, and just about every process I've ever seen: you alkaline clean first, THEN you acid activate, not the reverse as you are doing, because the surface is no longer "active" after you've done all that cleaning.
Further, your process times seem extraordinary. I've never heard of anything close to a half-hour in strong hydrochloric acid. I've rarely heard of an hour of cleaning, and certainly not after sand blasting. Have you ever tried: blast, 5 minutes ultrasound alkaline clean, rinse, 2 minutes muriatic acid, rinse, D.I. rinse, PVD?
Regards,
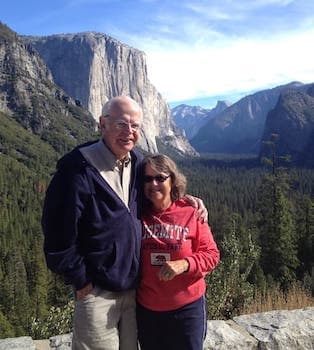
Ted Mooney, P.E. RET
Striving to live Aloha
finishing.com - Pine Beach, New Jersey
April 2016
April 19, 2016
I with Ted on the cleaning process -- seems a bit excessive. I've been involved in TiN coating the Magnum Research Desert Eagles without such extensive cleaning. In fact, never used any acid at all. We had a standard Crest aqueous cleaning line with ultrasonics.
Problem could be in the PVD process itself. Not sure what you call black pinhead popping, but it does seem like a compressive stress problem. Might want to lower your deposition bias, raise the deposition temperature, or apply a thinner coating.
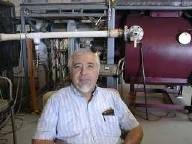
Jim Treglio - scwineryreview.com
PVD Consultant & Wine Lover
San Diego, California
A. Results depend, in addition to cleaning and coating process, on the nature of the components - geometry, basic material, previous surface treatment like plating, etc. - being coated. Could you throw some light on these aspects? What exactly is "strong etching"? Sharp edges pose no problem for PVD as cutting tools are routinely TiN coated all over the world. What is the PD process being used?
H.R. Prabhakara - ConsultantBangalore Plasmatek - Bangalore Karnataka India
May 1, 2016
Q, A, or Comment on THIS thread -or- Start a NEW Thread