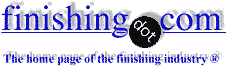
-----
Anodizing: Pitting/Blistering after Seal
December 7, 2015
Q. We are a sulfuric anodizing house that mainly runs aftermarket parts for the firearms industry. 95% of our work is media blasted parts for black Hardcoat.
We are having huge problems with our parts coming out of the seal with pitting/blistering with "salt" build-up on the sharp edges. See attached pictures. If we pull the load off the line before it hits the seal and examine the product we see no sings of this pitting/blistering that we are getting after the seal.
We are using a mid-temp nickel acetate running 6% concentration with a 5.6 pH. We run an automated line where the parts sit in the seal for 30-ish mins at a time.
We use filtered city water for our rinse tanks with 1.5 gals per minute of flow. Rinse time as of now is 6 mins in each rinse before the dye and seal. We have counter flow rinse tanks so the bar is rinsed in two tanks before it hits a chemical tank.
Due to limited room I am not able to introduce a nitric/neutralization rinse after HC and before dye.
I have been banging my head against these tanks for weeks now and need help figuring what I am missing. Any feedback would be appreciated.
- Keene, New Hampshire USA
A. You did not state the alloy or the thickness of the hardcoat. so we will assume 7075 and 0.002 inch. the white krud seems to be on sharp edges or 90 degree corners. Hardcoat builds perpendicular to the surface, so on a 90 degree corner there is very little coating and bare aluminum is converting to white aluminum oxide and white aluminum sulphate, which you do not see until the heat of the mid-temp seal flushes it out to the surface. The Mil Spec spells out a recommended corner radius for four specific thicknesses (the same is also listed in my book). A 5% nitric acid dip (which you cannot afford) ahead of the dye would help flush out trapped aluminum sulphate and sulfuric acid.
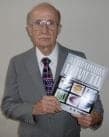
Robert H Probert
Robert H Probert Technical Services

Garner, North Carolina
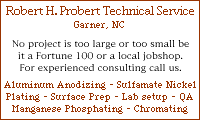
December 18, 2015