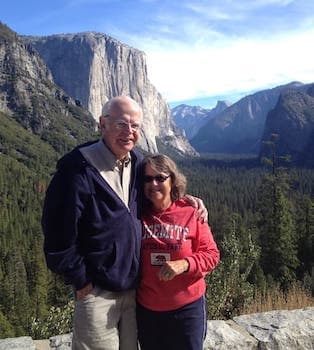
Curated with aloha by
Ted Mooney, P.E. RET
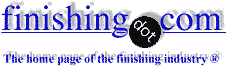
The authoritative public forum
for Metal Finishing 1989-2025
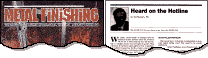
-----
Electroless Nickel Plating issue on A360 Aluminium diecast chassis
November 25, 2015
Q. Dear finishing experts:
I am a buyer sourcing a bowl-like part in shape with A360 Aluminum die cast as base material, wire brushing as surface treatment, and electroless nickel plating as the final finish in order to achieve the minimum requirement of passing 96H neutral salt spray test per ASTM B117.
The part is first cast/screw hole machined/wire brushed on outside surface/washed by the die cast supplier and then sent to the plating supplier to do nickel plating. It is a high phosphorous Electroless Nickel process. The supplier has many years of plating experience on Aluminum die cast parts.
The problem we are facing on this part now is that the inside surface (concave side) has many tiny pin holes or tiny alien objects stuck on the surface after plating and you can feel them by your finger. After investigations, we found the alien objects appear after the zincate process. We changed the Nickel plating solution tank with a fresh solution, but the issue is still there. We are planning to change the zincate solution tank as well to see if the impurity of the zincate tank could be the factor of the issue.
Do you have any experience on this kind of issue and can you help direct to someone who might be able to help explain why this is happening and how to resolve it?
with the best regards.
Dylan
- Toronto, Ontario, Canada
November 26, 2015
A. Good day Dylan.
I have some questions for you. What is the cleaning process?
Are you using the tri-acid (bomb) prior to zincate?
What is the concentration/baumé of the zincate?
Are you doing a single or a double zincate?
Are you using copper with the process?
I'm sure other replies will be helpful, if you can provide more info.
Regards,
Aerotek Mfg. Ltd. - Whitby, Ont., Canada.
December 3, 2015
Q. What is the cleaning process?
answer: chemical degrease first, then high temperature degrease, then Negative pole electrolizing degrease, with rinse in the middle of them.
Are you using the tri-acid (bomb) prior to zincate?
answer: immerse in Base after Negative pole electrolizing degrease , then immerse in base in Zinc (Tri)
What is the concentration/baumé of the zincate?
answer: 500±10 ml/l
Are you doing a single or a double zincate?
answer: double
Are you using copper with the process?
answer: no
- Toronto, Ontario, Canada
A. Hi,
If the measurement the zincate by Baumé and that is 500 ml and what?
I suggest to change the zincate to Bondal zincate from Macdermid.
You say there is a double zincate for the part. Skip it and use only one zincate for 50-60 seconds.
You say nothing about the pretreatment. Remember in the alloy there is some few percent Mg in it so the part should avoid a nitric treatment as a last step before zincate.
Best regards,
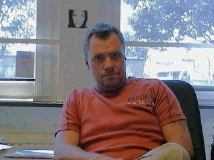
Anders Sundman
4th Generation Surface Engineering
Consultant - Arvika,
Sweden
January 8, 2016
Q, A, or Comment on THIS thread -or- Start a NEW Thread