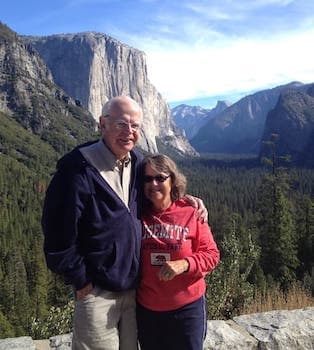
Curated with aloha by
Ted Mooney, P.E. RET
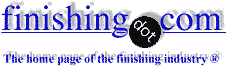
The authoritative public forum
for Metal Finishing 1989-2025
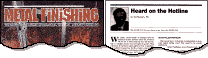
-----
Passivation of Corrosion Resistant Steels
2000
I'm a Manufacturing and Process Engineer for a large Aerospace firm. Lately it seems I can relate well with "one crying in the wilderness". I've been trying for the past 20 months to get our Specification Custodians and Materials Technology folks to provide an open mind for citric acid based passivate. I know there is at least one company producing citric acid formulations that far exceed the capabilities of Nitric Acid. It also seems that ASTM A967 is superior to AMS2700 with respect to content and control.
I'm having major difficulty getting the aforementioned folks to
"step beyond their box" and recognize there is a better way to passivate and a better specification that governs it. Many have inferred that "You're favoring a single potential supplier with no tangible evidence to support the claims made by personnel of this company".
I'm asking for assistance with the following;
1. Can anyone provide me with contacts to companies that produce citric acid Formulations for the purpose of passivating Corrosion Resistant Steels?
2. Can anyone provide me with test and "in-service" data related to parts they have passivated using citric acid Formulations? Please include references to spec's, too.
3. Are there any suppliers out there who currently provide any citric acid passivated components to the aerospace industry? If so, please provide your contact information and experience using Citric vs. Nitric solutions.
4. Has anyone documented any savings, in terms of time, money, and facilities, regarding their use of Citric formulations vs. Nitric, whether you produce or procure said parts? Please share this information.
5. Is ASTM A967 superior to AMS2700, as it appears to me to be? Why or why not?
Your assistance with all of the above, and any other suggestions you have is greatly appreciated.
- Seattle, Washington, USA
2000
Why don't you go to several suppliers of citric acid formulations, then you can't be accused of going to only one source. See the
Chemicals directory for suppliers.
Like the theory of the ether, most physicists of the time would show how the theory explained the mounting evidence against it, until the theory collapsed of its own weight. But the real reason we don't believe in the ether is because all the old physicists are dead, and the new ones believe in something else.
Passivation of steel is done to meet the specification sometimes, and does nothing to improve the corrosion properties in some cases. But the parts have been dipped according to the rule, so dry them off and put them in the box, becomes good enough until a corrosion failure happens.
I am not being critical or pessimistic, it is just funny to me that we fight change only because we are used to the problems we already have.
If this doesn't work, try wearing a camel hair loincloth, and switch your diet to locusts and wild honey. Crunchy, but the original health food.


Tom Pullizzi
Falls Township, Pennsylvania
2000
Dear Colleague,
There does seem to be a focus in USA to use citric acid as a passivating agent.
An effective passivating agent for stainless steel, high performance nickel alloys, titanium etc. needs to be a good oxidising agent.
citric acid is NOT an oxidising agent.
Oxidising agents necessary to passivate these alloys are nitric acid, phosphoric acid and of course oxygen.
Whilst I appreciate the zealous search for "green" products in USA, you cannot replace established technology necessary to achieve effective passivation.
citric acid is cleverly marketed for passivation because it removes free iron on the surface of the stainless steel by directly chelating iron.
However, passivation is subsequently achieved through a reaction with atmospheric oxygen.
If the work environment is subject to airborne contaminants such as iron oxide, iron chloride, sodium chloride and other pollutants, then there is no guarantee that passivation will reach a level to guarantee corrosion resistance, especially when the stainless steel is exposed to high corrosion environments.
My company is a specialist in this field, and manufacture products for pickling and passivation of stainless steel, nickel alloys and titanium.
We are pleased to provide advise for problems associated with fabrication or restoration of these alloys.
Best regards,
- Australia
Ed. note: We at finishing.com have been amazed at how people have managed to stay civil here through more than 30,000 responses to more than 6400 letters for more than 11 years. Take a look at the sci.chem newsgroup to see by contrast just how lucky we have been due to the diplomacy of our writers, and how ugly it can quickly get.
John, you are welcome to your opinions, and as welcome as anyone else to your vested interests, but the phrase "cleverly marketed" is incendiary, at least in U.S. English, and we would ask everybody to be diplomatic when challenging someone else's response.
Dear Sir, You need to evaluate the how good the citric acid based passivation solutions will work for you and what standards you need to achieve. The citric acid based solutions do not meet the military specs, only the ASTM's specifications. If you only need to meet the ASTM's standards, then the citric acid solution still needs to pass a test.
Thank you,
- Easley, South Carolina
2000
2001
With all due respect, there are a lot of misconceptions and disagreements about what passivation really is, and how it happens. The bottom line is that passivation of stainless (and "passivation" of other metals) is meant to improve corrosion resistance. If the test results show that corrosion resistance is improved, then the effect is achieved.
There are hundreds of tests by many companies which show that citric acid formulations not only achieve equal results to nitric and phosphoric acid passivation, but superior results.
An oxidizing acid IS NOT necessary to effectively passivate stainless steel. As noted, oxygen in the air very effectively forms the oxide layer once the surface is prepared adequately by removing as much iron and other exogenous materials as possible. The key to good corrosion resistance is to get the free iron off the surface AND enhance the chromium content of the surface. The higher chromium content in the surface forms the protective chrome oxide layer.
Citric formulations, just like any other chemistry, are not perfect solutions to all problems. However, for MOST passivation applications it will give you equal or superior results to the nitric acid formulations that have been used since the horse and buggy. While we respect the established technologies of the past, we need to move ahead if we are to IMPROVE the state of the art. This is not just a U.S. thing, it is being used all over the world in progressive shops.
The chelation of the iron by citric acid formulations is one of the reasons why the chrome oxide ratio on the surface is higher than what can be attained by nitric formulations. It effectively removes the iron from the surface without allowing it to be redeposited.
The old military standard,
QQ-P-35C
[from DLA]
has been cancelled in favor of ASTM A967 by DOD, which includes citric acid formulations, and is now the government & military standard for all applications except aerospace, which uses the AMS standards at this time. AMS2700 includes the use of citric acid , but it must be approved by the customer for use. The AMS standards are still in the process of development.
Anyone interested in learning more about citric formulations to achieve improved performance can contact us.
Regards,
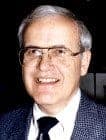

Lee Kremer
Stellar Solutions, Inc.

McHenry, Illinois
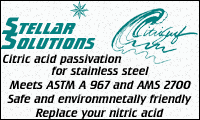
Dear Kurt,
Passivation can also be accomplished during the electropolishing process, along with smoother, brighter, and cleaner surfaces.
- Cleveland, Ohio USA
2001
We are also looking into using citric acid passivating to replace our nitric based passivate solution. My questions is this: Will these citric passivates also dissolve a copper coating? We passivate fasteners that have this copper coating on them which helps add lubricity during the heading process.
Michael Adams- Rockford, Illinois
2001
I'm curious as to what degree corrosion resistance of 316L SS is improved by doing both electropolishing and post-EP passivation. In the medical device industry I have seen several companies claiming that electropolishing alone does not increase the passivation layer breakdown potential enough, and so they do a post-EP nitric acid passivation as well.
I'd also like to know if anyone out there knows the max passivation layer possible to achieve on a 316L SS surface and what is a good minimum for acceptance criteria when the end use is human body implantation.
- Pleasanton, California, USA
2001
First of all, citric acid does not passivate.
Before to attempt to passivate a metallic surface, it must be thoroughly clean; citric acid is one chemical, among others, used for cleaning purposes.
There is a chemical treatment wherein citric acid is added at a given stage of the process to remove soluble Iron Oxides and, in conjunction with other chemicals, to remove Copper. Followed by the addition of other chemicals, wherein citric acid was previously added, it is accomplished the Passivation of the metallic surface under the chemical treatment. But the passivation is not produced by the citric acid .
The advantages of using the above generally outlined process over using Nitric Acid, are that (1) Nitric Acid is specific to passivate S. S., while (2)the above process can be applied to S. S and to other metals. (3) it is safer to apply the above process rather than applying Nitric Acid. (4)citric acid solutions wherein passivation takes place (Not by the citric acid itself, but by other chemicals used in the all treatment ) are easily disposed off.
- Nuevo Leon, Mexico
2002

this text gets replaced with bannerText
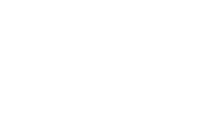
Q, A, or Comment on THIS thread -or- Start a NEW Thread