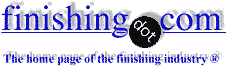
-----
Waste Treatment Solution Needed
I have just recently been put in charge of the Haz-Mat program in my company. We are a sheet metal mfg. and our processing room's current waste treatment process I find unsatisfactory. It dumps about
100 GPD into various floor tanks, these are then pumped to a 2000 gal tank & the CR6 is precipitated to a Cr3 (trivalent) state. The water is then sent through our carbon and DI exchange system. What I find wrong with this is that because of the solids still in the treated waste stream only around 100-200 gallons can pass through each DI column. This is rather costly as we pay over $200 for each column to be recharged. I am currently measuring a conductivity of
5.4 millisiemens in our treated waste stream. The lower the conductivity, the more I am able to pump through each DI column.
I need a better system, but I am unsure what to use. Due to the fact that all process tanks are dumped into floor tanks then added together for treatment, my understanding tells me that RO won't work(it is waste stream particular).
I have thought about purchasing a small evaporator to send the waste stream through. The concentrate recovered could not be reused,but would have to be disposed of. However, I could then run tap water through the DI exchange system and run around 3000 gallons per bottle.
Any help here would be greatly appreciated!
- Ponderay, Idaho, USA
2000
A couple ideas
First, depending upon the chrome levels present in the water before you reduce and precipitate the chrome, why not pump it directly to through the IX. This way you avoid having to remove the salts you just put in the water to treat it. Is your conductivity higher or lower before chrome reduction? I imagine there is got to be a lot of sodium and sulphate left in the water from the chrome reduction.
Second, are you unable to discharge? If so run the sludge and water through a small filter press and follow with a chelator resin to polish the water. The treated water could be collected in a holding tank which is released to drain after verifying discharge limits. You will need to make sure all your hex has been reduced prior to precipitation.
Third, can the solution be isolated and returned to the tanks it originated from? Are there rinsing steps in your process after the chrome? If so how is this handled?
Hope this is of some help.
- Illinois
2000
Ben:
Assumption: Appropriate pre-filter treatment leaves no hazardous metal in solution. All hazardous metals are as particulate fine sand/or hydroxides.
Sounds like you just need a course filtering to remove majority of solids before putting through Carbon/DI filter. 5-10 micron filtering should do the trick. There have be successes using filter presses,cartridge filters and centrifugal separators before final micro-filtration or Carbon/DI filtering.
Evaporators also work. The ones I know of reduce the waste volume approximately 90%. If they are more efficient ones available, maybe someone will let you know. In both cases, filtering and evaporating,you will still have a hazardous sludge or concentrate to dispose of.
Good luck.
Houghton International - Raleigh, North Carolina
2000
The conductivity is much higher before treatment. Due to the contents of the waste stream, it is sent through a carbon filter which would take out the chrome before it got to the IX and would rapidly deplete.
We are able to discharge, however, due to the fact that each of our waste streams vary... the sewer requires testing of the waste stream for each discharge. As the costs of the tests are around 500 a shot to discharge 1500 gallons, I would have only decreased disposal/treatment cost per gallon by to approximately $1 per gallon.While this is better than $2-3 per gallon, I feel we can do better.
Every process tank has it's own dragout rinse, and each set of tanks have a rinse (i.e. all alkali tanks have their own dragouts,but share the same rinse, Alodine tanks have their own...). As all tanks are transferred to the same waste treatment tank, I do not see how any reclamation of chemicals can be economically accomplished.
I don't feel that designing a separate reclamation system for each process tank would give me a comparable payback. So I am looking for a non-wastestream specific device to either filter out (at a low cost)all contaminants for reuse of the water, or simply dispose of water and give us a concentrate to have hauled away (i.e. an evaporator).
Thanks for the ideas though John!
- Ponderay, Idaho, USA
2000
First of three simultaneous responses--
The cheapest immediate help, would be to put in a 5,000 gal cylindrical storage tank with appropriate containment. This has several benefits, first, the cost of testing is the same, but you test only 1/3 as often. Second, you decrease the amount of any given regulated ion, by basically diluting the amount of any of the bad guys with other bad guys,with a net lesser amount of each.
Large plastic tanks are quite cheap as tanks go.
You have not mentioned a filter press. It would be well worth the purchase of an appropriate sized one after reduction to trivalent and adjustment of pH. This will lighten the load on the DI system.
pH adjustment, filtration, ultra filtration and RO on the nonchrome rinses and recycling would very probably be cost effective.Floor space is frequently a problem in most shops. As the old adv. went, pay me now or pay me later.
- Navarre, Florida
2000
Second of three simultaneous responses-- 2000
Ben.
The mooted idea of a coarse filter makes sense. Maybe a preliminary VERY coarse filter followed by finer filters to protect the expensive carbon filters. You can get PP filters from l00 down to around l micron. Suggest, perhaps, l00 micron coarse prefilter followed by a smaller one.
The other option of evaporation has one big negative. BTU's and the sheer cost of heat evaporation.
- What about a simple 'packed section' horizontal scrubber evaporator using ambient air?
- l. Use an inexpensive centrifugal mild steel 'push' fan. .
- 2. Make up a 'box' using, say, 2" packing, Tripack or similar
- 3. Have the 'push' air come in horizontally.
- 4. Make the box of mild steel. Cheap. At the top of the 'box', have a liquid distributor. To get good distribution, ensure that, say, you have a least 4" min of packing height above which is that 'distributor'. The distributor could be spray pipes but I prefer a better (technical) solution. A perforated plate, easily removable, will distribute the 'liquid' over the entire packing surface and just need a simple 'liquid' inlet above it. In other words this 'box' would resemble internally a horizontal mass transfer scrubber.
- 5. Pump. You'd need a pump to recirculate the liquid. The liquid will, of course, in time become sluggish as the evaporation process continues.
- 2. Make up a 'box' using, say, 2" packing, Tripack or similar
I have seen this used successfully for concentrating hard chrome waste. A Company called ALLANCO near Vancouver, B.C. but I think that they used PVC for the 'box'. The end user being Molectro hard chromeCo. At the end of this unit was, I believe, a single PVC mist eliminator blade bank, probably good for 15 to 20 micron capture,depending on design speed.
Anyhow, food for thought. Cheers!
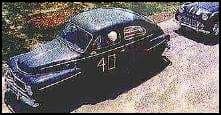
Freeman Newton [deceased]
(It is our sad duty to advise that Freeman passed away
April 21, 2012. R.I.P. old friend).
Third of three simultaneous responses--
Assuming you send your water to an outside service, have you looked into testing the water yourself with a HACH test kit or picking up a used AA to make the analysis less painful? Otherwise, besides getting a much larger holding tank to cut the costs on analysis, evaporation sounds like the best option considering your volume. May be a large capital investment depending upon the needed materials of construction. Out of my realm of expertise however.
Good luck
- Wheaton, Illinois
2000
Q, A, or Comment on THIS thread -or- Start a NEW Thread